Managing Valves in an EPC Project
Valves and fluid controls may need extra attention in EPC projects.
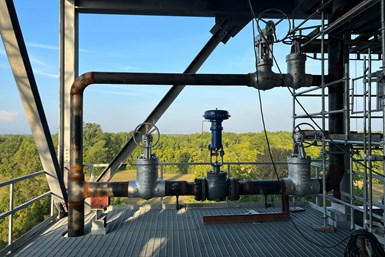
Piping system construction in progress.Source: IAC International
Piping systems in industrial plants such as oil and gas facilities, chemical and petrochemical plants, food and beverage manufacturers, mining or water/wastewater plants all require detailed, application-specific information and engineering drawings before valves can be specified and ordered. This can take 20−25% of total engineering man hours and construction work in projects. Piping systems connect equipment and components all over plants. Below are some of the considerations related to managing valves in an EPC project.
- The type of valves — as well as size, pressure class, material, end connections and other parameters — are selected through cooperation between process and valve engineers who work with piping and instrument diagrams (P&IDs).
- During the detail engineering phases, P&IDs are more mature and developed. At this phase, the list of valves named as first material take-off (MTO) are created and should contain size, pressure class, material, end connections and other special valve requirements such as bore types (full or reduced) for ball valves or any required coatings. General valve requirements such as factory acceptance tests (FAT), packing, preservation, documentation and more are provided in project specifications.
- The MTO, plus relevant valve specifications and datasheets, are sent to potential valve suppliers or manufacturers for purposes of soliciting technical and commercial quotations.
- Valve and actuator suppliers or manufacturers deliver their products with all relevant valve documents such as drawings, procedures, reports and more. Dimensional drawings are modeled in a software program such as a plant design management system (PDMS), similar to a 3D AutoCAD. This design software is used to make 3D models for piping and valves, equipment and structures. If different vendors are selected for supplying specific valves of the same size and pressure class, dealing with two different sets of drawings and other documents is challenging.
- Multiple valve manufacturers or suppliers as well as subsuppliers for forging or casting, machining, coating and more from different locations adds complexity to the project. Another consideration is actuator manufacturers. The actuator suppliers will make and supply the actuators to the valve manufacturers to complete assembly and test. Lack of communication and coordination between the valves and related actuation suppliers can delay the valve procurement process.
ACTUATOR SUPPLIER SELECTION STRATEGY
Generally, there are two ways of selecting actuator manufacturers. The first is to select directly from the end-user-approved vendor list. The other approach is to authorize valve suppliers to select suitable actuator suppliers from the approved vendor list of the client. While this approach can facilitate the communication and coordination between the valve and actuator manufacturers, it may lead to selecting more and more varied actuator suppliers for the project.
ORDERING SPECIAL VALVES
Special valves may include large-size and high-pressure class valves with special designs, based on the application. These valves are at higher risk of being delayed during procurement, often requiring longer lead times, sometimes more than a year from order to delivery. The complexity of these valves can be intensified if, for example, they are top entry and double isolation and bleed designs, if the pup and transition pieces are welded, if they will see a high frequency of pigging, if they face special transportation issues or if they have qualification test requirements. The number of subsuppliers for these special valves is high, which means constant monitoring and expediting.
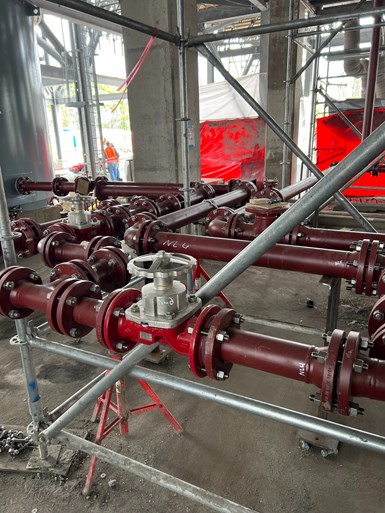
Specialty valves, actuators and other components may take extra time to procure. Source: IAC International
VALVE MANUFACTURER CAPACITY
The quantities of the valves might be high enough that a specific valve manufacturer may not have enough machining equipment, test bench capability or workers available to fulfill the order. Thus, the production capacity, as well as the engineering, procurement and manufacturing scheduling of the valve manufacturers should be checked before purchase orders are made. In some cases, the selected valve manufacturers might subcontract part or all of the work to other manufacturers, which increases the complexity and speed of valve supply within projects.
EARLY CONSTRUCTION SITE NEED DATES
Normally, larger valves have earlier site need dates because construction takes place on the larger lines before the smaller ones. Larger valves normally have longer procurement and delivery times as well. For instance, an earlier date may be required if the valve is weld-end rather than a flanged connection.
LATE-STAGE VALVE FAILURES AND PROBLEMS
Some valve problems and failures are discovered at a late stage at the construction site, which causes delays. Many issues can occur, such as a wrong direction of the actuator on the valve or insufficient clearance for installing the valves’ mating-flange fasteners. When possible, the valves should be returned to the valve supplier for further machining on the body end flanges, which can have a severe impact on the construction work schedule.
ORDERING VALVES WITH EXTRA OPTIONS
Some of the ordered valves will have added options such as coatings, stem extensions, specialty materials and more. Adding these options increases the variety within the project. For example, eight full-bore ball valves of 6 inches in Class 300 in 22 Cr duplex material might remain uncoated but two other ball valves with the same specification might be insulated and coated to avoid corrosion under the insulation. These valves would be differentiated from the other eight only by coating requirements.
There are many valve-related considerations in EPCM projects. Some of these can be tracked and guided through tools such as piping and instrument diagrams. The important point to remember is that, in the end, knowing the challenges enables those who supply and make the equipment to reach the ultimate goal: satisfied end users.
This is derived from a two-part article originally published in Valve in 2019 and authored by Karan Sotoodeh in his role as a lead/senior valve and actuator engineer for Baker Hughes. It has been edited for this republication.
RELATED CONTENT
-
Grease for Motor Actuator Maintenance
Maintaining the right amount of grease inside motor actuators that use grease for lubrication is a vital part of valve maintenance, and can save time and money by preventing problems before they happen.
-
The Nuts and Bolts of Nuts and Bolts
Repairing a valve usually means discarding old fasteners and replacing them with new ones.
-
Gaskets Are Not Created Equal
Gaskets are near the bottom of the food chain of valve components; trim, body materials and packing seem to get a lot more press.