PLANT EQUIPMENT & SUPPLIES
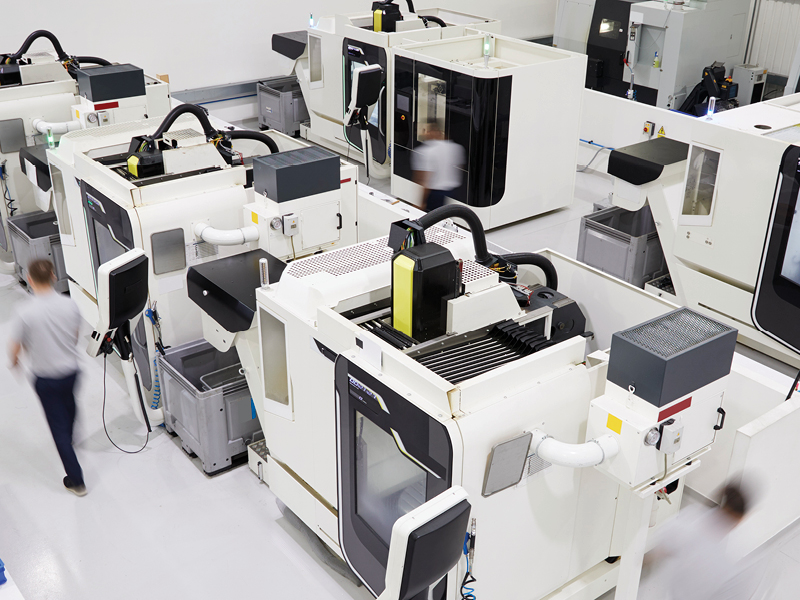
While machine tools represent the core of production machining businesses, it is also beneficial to have other processes in-house, such as anodizing, passivation, deburring, part marking and heat treatment.
Narrow by Plant Equipment & Supplies Product Category
-
Equipment
- Aqueous Cleaning & Degreasing Equipment
- Chip & Sludge Dragouts
- Cleaning Equipment
- Compressors
- Coolant Reclamation Equipment
- Dust Collectors & Air Filtration
- Electrical Switchgear, Enclosures & Components
- Furnishings, Shop & Office (Files, Desks, Benches, Cabinets, Tool Chests, Drawing Boards, etc.)
- Hand Tools of all Types
- Noise Abatement
- Oil Filtration & Treatment
- Plant Maintenance & Repair Equipment
- Pollution Control & Environmental Equipment
- Printers/Plotters/Drafting Machines
- Vapor Degreasing Equipment
- Voltage/Current Regulators, Transformers & Phase Converters
- Water Filtration & Treatment Equipment
- Metalworking Fluids
- Parts Cleaning
FAQ: Plant Equipment & Supplies
What coolant is best for titanium?
Water-based coolant is typically best for titanium. For better tool life, try to use through-spindle coolant (if you aren’t already) in order to get the coolant as close to the cutting edge/material interface as possible. Higher pressure is good, but higher coolant flow is also important.
(Sources: How Effective is MQL for Drilling Titanium/Aluminum Stacks? & Tool-Related Considerations for More Efficient Machining of Titanium)
How do I control coolant mist?
Manufacturers use mist collectors on machine tools to provide cleaner air and a better working environment for shopfloor employees. Mist collectors minimize the adverse effects of exposure to metalworking fluids and help shops comply with indoor air quality standards. They also improve in-process part quality by keeping work surfaces clean while reducing maintenance and housekeeping costs.
In general, all mist collectors coalesce tiny mist droplets into larger ones and drain the collected coolant to prevent the filtration system from becoming plugged. (Droplets generated during milling and turning operations range in diameter from 2 to 20 microns for water-soluble coolants and from 0.5 to 10 microns for oil-based coolants.) However, there are differences in the ways that particular mist collector systems remove droplets from an airstream. It’s important to consider these distinctions when determining what design is best-suited for a given application.
(Source: Mist Collector Design Fundamentals)
How do I reduce energy costs in my facility/shop/plant?
Over the past decade, an increasing number of machine tool end users have adopted specific targets to reduce energy costs and more importantly, carbon dioxide emissions. In recent years, the focus of this effort has shifted to data-driven manufacturing methods to achieve this. While it is important to monitor production throughput, downtime and energy consumption to get a real-time picture of shopfloor performance, it is equally important to optimize your manufacturing equipment right from the start. Ideally, such optimization should begin at the OEM level, or when upgrading or retooling equipment.
Developers of industrial control systems can play a major role in enabling suppliers of machine tools and other manufacturing equipment to reduce energy usage and improve efficiency from the ground up. In fact, control developers should be at the forefront of the energy-efficiency initiative, and it is important for end users to understand the technology now offered to support this initiative.
(Source: Optimize to Save Energy)
Get Listed!
Thousands of people visit this Supplier Guide every day to source equipment and materials. Get in front of them with a free company profile.