CUTTING TOOLS
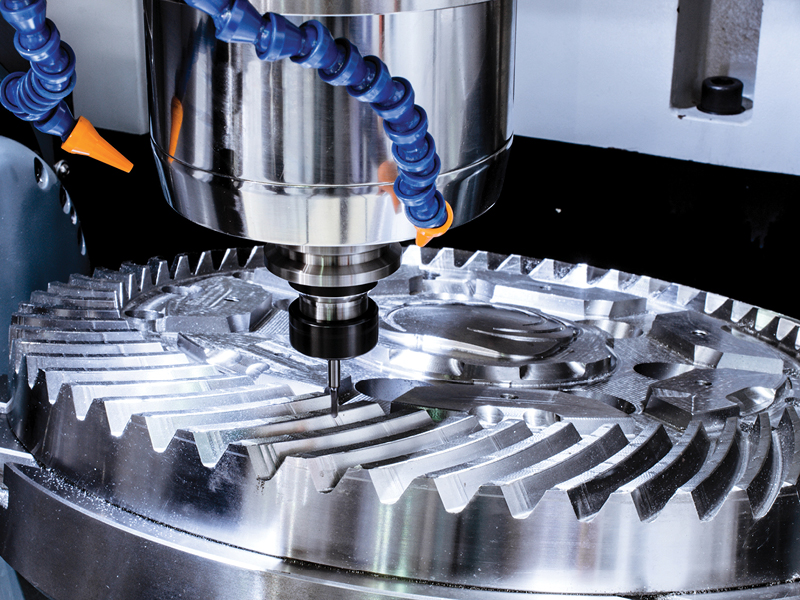
Drills, taps, end mills, grooving tools, form tools and turning tools continue to be redesigned with new geometries and coatings to maximize material removal rates and surface finish of machined parts.
Narrow by Cutting Tools Product Category
FAQ: Cutting Tools
What is a chamfered edge?
A Chamfer or deburring tool is used to create a bevel or furrow on the end of a bolt.
What is a chamfering tool?
A Chamfer or deburring tool is used to create a bevel or furrow on the end of a bolt.
What is a collet?
A collet utilizes clamping pressure by forming a collar around the object being held, holding it securely in place. While there are varying designs, all collet types operate by being pressed over the element to be held, resulting in both accurate alignment and static friction. Source: T.M. Smith Tool Inc.
What is a counterbore?
A counterbore is a drilled hole that has a flat-bottomed enlargement at its mouth. Source: Oxford Languages
What is countersinking?
To countersink is to enlarge the and bevel the rim of a drilled hole so a screw, nail or bolt can be inserted. Source: Oxford Languages
How do you countersink screws?
To drill a countersink, place the countersink bit in your drill and push down lightly on the pilot hole. Drill down a little at a time until your desired depth. Source: DIY Doctor
What is the best drill (or mill) for stainless steel?
The right balance between hardness and toughness is the most crucial factor when selecting a grade for a particular application. Picking a grade that is too hard can lead to micro breakages along the cutting edge or even catastrophic failure. At the same time, a grade that is too tough will wear out fast or require decreasing the cutting speed, thus reducing productivity.
In drilling, the center of the drill always has a cutting speed of zero, while the periphery has a cutting speed that depends on the drill diameter and spindle speed. Grades optimized for high cutting speeds will fail, and therefore should not be used. Most suppliers will offer just a handful of grades.
In milling, the range of grades on offer is small. Due to the application’s fundamentally interrupted nature, milling tools require tough grades with high impact resistance. For the same reason, the coating layer must be thin — otherwise, it will not withstand the impacts.
Most suppliers will use a tough substrate and a variety of coatings for milling different material groups.
(Source: Choosing Your Carbide Grade: A Guide)
What is the best tool (or insert) for titanium?
For milling operations, go with a medium hardness grade. For turning operations, use the following:
-
- Continuous turning: very hard
- Light interrupted: hard
- Heavy interrupted: medium hard
(Source: Choosing Your Carbide Grade: A Guide)
How can I increase tool life?
The key to being able to cut faster and improve tool life is to keep a constant force load on the cutter. This reduces the shocks and vibration that occur when material engagement changes abruptly, for example, when a tool hits the corner of a pocket. In high efficiency machining this is most often accomplished by manipulating the tool path to keep tool stepover and feed rate constant, which can result in highly variable chip thickness and force load on the tool. Because the process requires a climb cut, this can also create a lot of air cutting time when repetitive unidirectional passes are required. And it tends to limit use of the technique to certain open features of the part.
Get Listed!
Thousands of people visit this Supplier Guide every day to source equipment and materials. Get in front of them with a free company profile.