Zero-Emissions, High-Power Demand Actuators in Off-Grid Locations
Alternatives to using process gas and electrically powered actuators are available.
#actuators
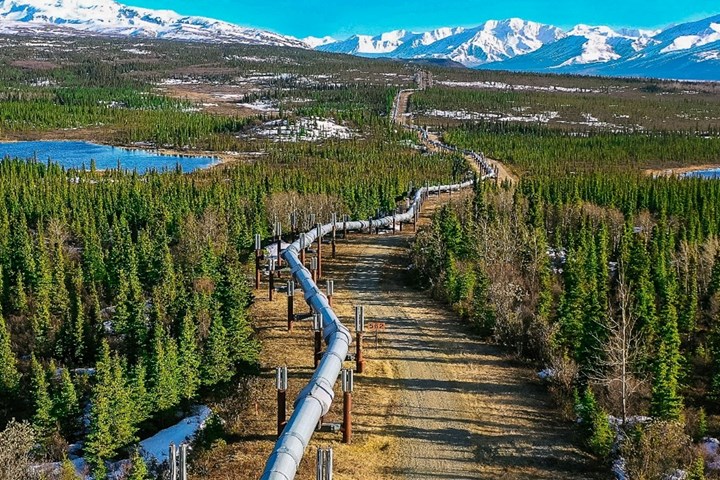
As the EPA’s (Environmental Protection Agency) upcoming restrictions for VOCs (volatile organic compounds) come into force in the coming months, users are evaluating different options to reduce or eliminate emissions from pneumatic controllers that have either a continuous or an intermittent bleed. This is relevant specifically to methane emissions from pneumatic controllers, including valve actuators. These emissions include those occurring from leaking equipment (also referred to as fugitive emissions) in all parts of the infrastructure, including primary production and processing equipment (e.g., separators or storage vessels) and individual components (e.g., valves or connectors). Although regulations are not the only factor for users to consider when looking for alternatives to reduce or eliminate emissions, operators’ safety in using these systems has always been a concern. Some process gases can be toxic or harmful to human health, and exposure to these gases can lead to respiratory problems, eye irritation and other health issues. In addition, accidents of injured operators have been reported because of explosions due to vented process gas from these controllers.
Why use process gas to power valve actuators?
The oil and gas sector extensively uses process gas as an energy source to power pneumatic controllers. Pneumatic controllers are widely used in these production facilities to control the operation of pumps, actuators and other equipment. These controllers utilize compressed air or process gas to function. Using process gas to pneumatically power controllers offers several advantages:
- The need for external air compressors or other compressed air sources, which can be expensive and require additional equipment and maintenance, can be eliminated.
- It helps reduce the facility’s overall energy consumption and, most importantly, provides an energy source in remote locations where no other source is readily available.
Alternatives to gas-powered valve actuator emissions
The industry offers several alternatives to replace or retrofit these actuators to reduce or eliminate the venting of methane emissions into the atmosphere. To choose one of these existing technologies or to develop a new technology to address this challenge, one must consider the multiple factors impacting the change to zero-emission controllers.
One of the least invasive alternatives to reduce emissions from pneumatic actuators is collecting and recirculating the exhausted gas. In systems like gas-over-oil actuators, the process gas is used to pressurize hydraulic fluid, which is later used to operate the actuator and also the valve. After the actuator is stroked, the gas is exhausted into the atmosphere.
An alternative solution is a system to capture and pressurize the exhausted gas so it is injected back into the process line. From an energy consumption point of view, this alternative does not provide an advantage. As stated previously, one of the main reasons for using process gas to power pneumatic controllers is that it eliminates the need for external power sources. In these actuator systems, energy is needed not only to pressurize the gas but also to pressurize it to a higher pressure so it can be reinjected into the pipeline. Why not use this energy to power the actuator directly? Moreover, such systems are complex, they require regular maintenance to ensure constant effective operation. This can be time consuming and costly, particularly for large-scale systems. If not appropriately maintained, these systems are still susceptible to gas emissions since they use process gas as a primary energy source.
Compressed air
In locations with a high pneumatic controller count, replacing the process gas with compressed dry clean air or another inert gas is perhaps the best alternative. The pressurization system requires a power source, preparation and storage system, which can lead to a high overall initial cost. However, the maintenance cost may be minimal compared to other alternatives, and almost no modifications would be needed to install the existing pneumatic controllers. In addition, changing from gas to clean air will prolong the service life and reliability of the pneumatic controllers. Different power sources, including electric utility power, can be used, but this will increase the overall power consumption and lead to higher operational costs.
For off-grid locations, one alternative is to use a gas generator to power the compressed air system. Even when the emissions are minimal, they may not be 100% eliminated. Using a generator will also have a higher initial cost and require regular maintenance to ensure proper operation and prevent emissions due to leaks in the system.
Moving away from using the process gas as the primary energy source will be a safer way to ensure a zero-emissions system. An alternative reliable energy source is needed to achieve this.
Electric actuators
In locations with a medium to low count of pneumatic actuators, using an electric power source to operate electric actuators is a cost-effective solution and provides other advantages, such as remote monitoring. This alternative, presents limitations in some applications, depending on the available electric power supply. Electric valve actuators may not be practical in facilities with limited electrical capacity or remote locations where access to electricity is limited, for example, via solar panels. Additionally, power outages or other disruptions to the electrical supply could cause a failure of valve control. Electric actuators have torque limitations, and because they depend on the electrical power supply, they are less reliable in the case of a power outage. By contrast, pneumatic or hydraulic actuators use pressurized fluid to generate force. This allows them to have a larger output capacity, especially in hydraulic actuators, and more reliable energy backup systems when power fails and actions cannot be achieved mechanically (springs).
Zero-emissions pipeline valve actuators in off-grid locations
Based on these considerations, the biggest challenge is finding a zero-emissions valve actuator for high power consumption applications in off-grid locations – the ideal candidate for process gas-powered actuators such as gas-over-oil actuators. An excellent example of these applications is emergency shutdown (ESD) valves.
Used in a variety of industries to quickly shut down a process in an emergency, ESD valves are typically spaced along a pipeline at intervals that are sufficient to provide an effective shutdown while also minimizing the potential impact on the overall operation. Because of the remoteness of these valves, applying large-scale solutions would not be the most cost-effective approach in these applications. Instead, the answer to finding zero-emissions valve actuators relies on a system capable of providing the force capacity, reliability, and simplicity of fluid-powered actuators with low power consumption, while using a reliable and available power source.
Low-power electrohydraulic actuators
Low-power electrohydraulic actuators use a low-consumption hydraulic power unit to drive the valve directly or to pressurize hydraulic fluid in accumulators, which allows for large force capacities. Actions during a power or signal failure are driven mechanically using springs. When the force required surpasses the capacities of the springs, a hydraulic spring system is added. Unlike a conventional accumulator backup system for failure action, the hydraulic spring uses the actuator movement to restore the hydraulic pressure. This eliminates downtime to recharge the accumulators, ensuring the valve action immediately upon failure.
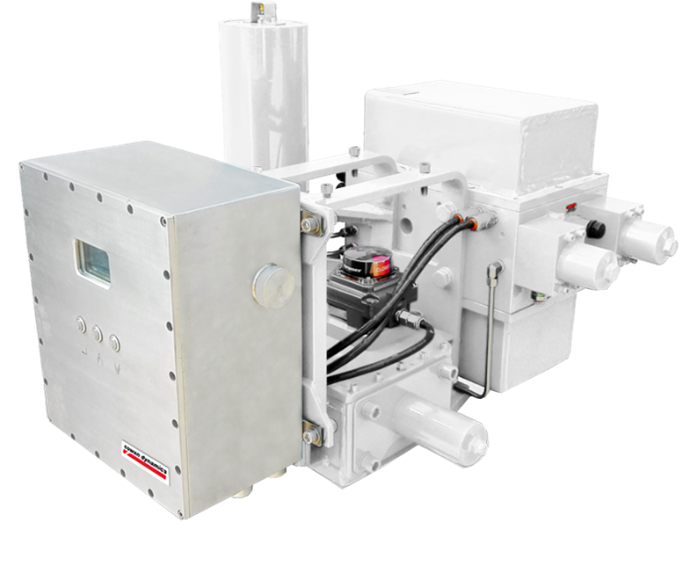
Cowan Dynamics Series E2H90 electrohydraulic actuator (solar power station not shown).
For off-grid locations, the hydraulic power unit of the actuator is powered by the actuator’s solar power station. Because of the reliability concerns of solar power, the power supply system can be backed-up with site electric power, or energy can be stored in accumulator systems to drive the actuator in case the power is not available or fails.
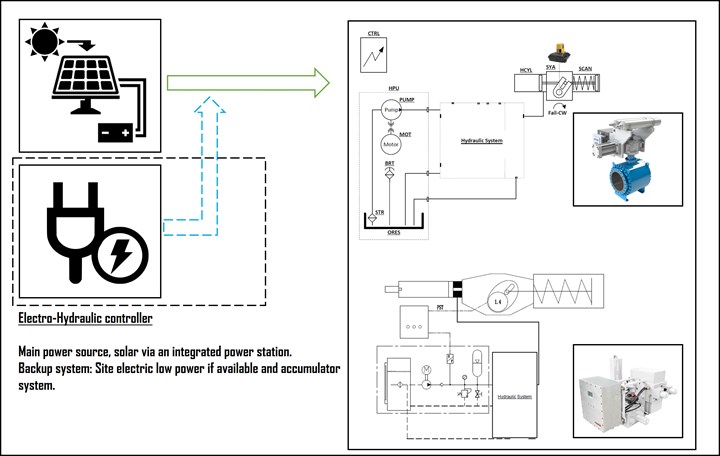
Solar-powered, low-power electrohydraulic actuators.
These systems offer several advantages because they are true zero-emissions actuators that completely replace the use of process gas as the source of energy. They have force capacities equal to or greater than a gas-over-oil system. They use solar power as the primary source of energy to drive a high-capacity hydraulic system, which ensures reliability of actuation upon power or signal failure. Implementing these systems may have a higher initial investment than the collection and recirculation systems previously discussed, however, they provide an energy-efficient design and a long-term solution.
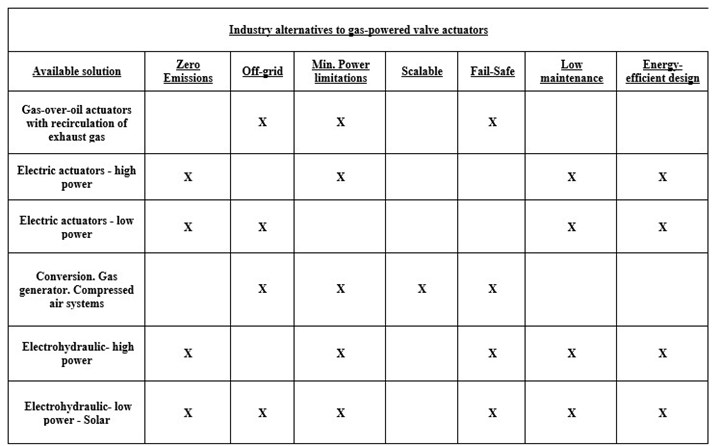
Factors:
- Zero emissions: There is no risk of emission. The system completely moves away from the use of process gas.
- Off-grid: No source of power is readily available. Low power for control systems may be available.
- Minimum power limitations: Actuators with high force capacities.
- Scalable: Solutions that focus on the source or energy and not on the replacement of the controllers.
- Fail-safe: Actuators with a backup system for operation after power supply failures.
- Low maintenance: Simpler systems, lower risk of failure.
- Energy-efficient design: Less energy consumption to provide the same levels of output force capacities.
Maria Aguirre is a professional mechanical engineer with a master’s degree in mechanical engineering and a master’s degree in environmental engineering, and she is a certified professional mechanical engineer. She is the director of business and product development for Cowan Dynamics and is a VALVE Magazine editorial advisory board member.
RELATED CONTENT
-
VMA News
VMA’s mission is to serve the growth and innovation of the U.S. and Canadian industrial valve industry globally by providing a forum that enhances a positive operating environment, increases knowledge, advances technology innovations and facilitates business and government connections for manufacturers, distributors and service providers of valves, actuators and controls.
-
Optimizing Actuator Performance in Harsh Mining Environments
How to overcome maintenance challenges and improve precision control in flotation applications for better performance and increased profitability.
-
Industry Profile: Jean Dockendorf
We recently asked Valve Magazine Editorial Advisory Board member some questions about what got her into this world of fluid controls, and what she does outside of the world of valves and actuators.