Direct-Sealing Diaphragm Valves Offer Novel Approach
As modern industries such as hydrogen electrolysis and biotech make dramatic technical advances, engineers and researchers must sometimes turn to nontraditional process control systems.
#controls #automation #pressure-relief
As modern industries such as hydrogen electrolysis and biotech make dramatic technical advances, engineers and researchers must sometimes turn to nontraditional process control systems. A common challenge is to find precise fluid control methods that perform reliably and are easily automated despite widely fluctuating flow rates, wide pressure ranges, extreme temperatures, mixed-phase flow and harsh chemicals.
For complex systems with particularly difficult combinations of challenges, a direct-sealing diaphragm valve or regulator is often a good choice.
BACKGROUND
Traditional dome-loaded valves, which have been available for many years, use a fluid pressure on top of a sensing element to provide a setpoint pressure. The sensing element is typically either a diaphragm for lower pressures or a piston for higher pressures. A single sensing element separates the process fluid from the dome fluid so that the pressure imbalance places the valve in the desired position.
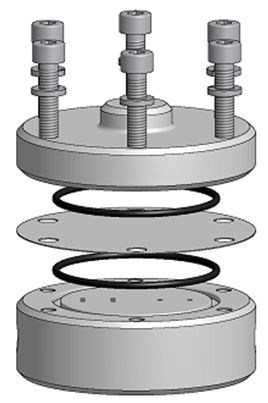
Figure 1. Exploded view of a direct-sealing diaphragm valve showing cap, O-rings, diaphragm and body with field of parallel orifices. Photo credit: Equilibar
Dome-loaded valves are pilot operated, which means that the pressure of the fluid fed to the dome is set by a second regulator called a pilot regulator. For some applications, the pilot regulator is a manual air regulator. For computer-automated applications, an electronic pressure regulator usually makes more sense. The electronic pressure regulator takes the input signal from the computer and translates it into a pressure that is fed to the dome.
In addition to being easy to use with computer automation, dome-loaded valves and regulators also tend to improve precision by delivering a more constant pressure as the valve position varies. Some dome-loaded designs benefit from the complete elimination of O-ring friction and hysteresis.
A direct-sealing diaphragm valve is a newer iteration of dome-loaded fluid control technology. Also known as a dome-loaded multiple orifice valve, it uses a novel design in which a diaphragm covers a field of parallel orifices located in the body of the valve or regulator. As fluids flow through the unit, the diaphragm lifts off the orifices to release pressure. When flow is minimal, only a portion of one orifice opens to release the pressure. When flow is high, the diaphragm is pushed up to engage all the orifices.
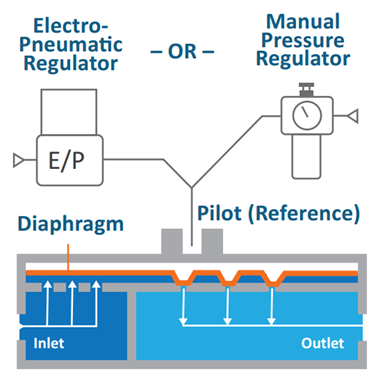
Figure 2. Schematic showing how a direct-sealing diaphragm valve works. Photo credit: Equilibar
The flexibility of this design results in an exceptionally wide flow rate range that can provide solutions for some of the most extreme fluid and pressure control scenarios. The design can hold pressure stable across ranges of 1,000:1 and even up to 100,000:1 for many processes. The frictionless diaphragm avoids all hysteresis, allowing for highly precise control in manual, open-loop or closed-loop control systems. Moreover, its reaction time is virtually instantaneous.
CATALYSIS RESEARCH DEMONSTRATES POTENTIAL BENEFITS
Catalysis research is a fast-growing field of inquiry, partly due to its value in discovering ways to make cleaner fuels and reduce emissions related to the combustion of carbon-based fuels.
A single catalysis research application can be highly complex, involving harsh chemistries, extreme temperatures, unusually high or low pressures, automation, the mixed-phase flow of gasses and liquids together and a need for stable control despite ultra-wide flow rate ranges. High precision, instantaneous adjustment and smooth operation are often required for the research to be successful.
Direct-sealing diaphragm technology can capably handle these types of applications due to synergistic design elements. These valves and regulators provide reliably stable pressure control because they are dome-loaded. Since the diaphragm is the only moving part, there is no hysteresis. At the same time, the multiple orifice design’s wide flow rate range makes it ideal for mixed-phase flow.
The valve’s body, O-ring, diaphragm, and bolts can be made from virtually any material, which means that direct-sealing valves can be customized for applications with extremely high or low temperatures and severe chemistries such as hydrofluoric acid.
VACUUM CONTROL OPTIONS
Direct-sealing valves and regulators were first used to control back pressure in the early 2000s. More recently, engineers and scientists have successfully used them to provide exceptionally precise and sensitive vacuum control as well as flow control.
For vacuum control systems, a vacuum pilot regulator is used to set a vacuum setpoint on the direct-sealing primary valve. It behaves like a back pressure regulator because the pressure is controlled at its inlet port. The vacuum regulator closes to increase absolute system pressure or reduce vacuum level. In essence, this vacuum control setup is a mirror image of the back pressure control setup. The pilot vacuum on the dome may be regulated using a manual or an electronic vacuum regulator and may be operated in open loop or closed-loop control schemes.
The system directly controls vacuum pressure by throttling flow between the vacuum supply pump and the process to precisely control the process vacuum to a specific setpoint. It is important to note that the direct-sealing vacuum valve is a non-relieving regulator intended for processes where at least a tiny gas flow is present at all times. It is not a vacuum breaker, which lets gas into the system to control pressure.
Glovebox pressure control, which can present multiple challenges for traditional vacuum valves and regulators, is an example of the complex types of processes that could benefit from direct-sealing vacuum technology.
Figure 4. Schematic of glovebox vacuum control using a direct-sealing diaphragm valve. Photo credit: Equilibar
In many glovebox situations, it is desirable to control pressure differential so that the dexterity of the operator’s gloves is not compromised. At the same time, it is important to provide for much stronger vacuum supply in the event of a compromised glove or opened hatch. This is exceedingly important due to the combination of extreme conditions and hazardous materials. A vacuum control failure could have catastrophic results.
Direct-sealing vacuum regulators are especially well suited for these situations. Their reaction time is virtually instantaneous and they are capable of controlling vacuum pressure in a glovebox down to the range of 1 inH2O (2 mbar). As the glovebox falls below the vacuum setpoint, the direct-sealing diaphragm lifts rapidly to increase flow and restore glovebox vacuum pressure, averting dangerous situations. Conversely, if the glovebox vacuum becomes too high, the diaphragm lowers, restricting flow and rebalancing the glovebox pressure.
Other vacuum processes that may require direct-sealing technology include work-holding applications where flow rate and pressure vary significantly during start-up and as disruptions occur in the manufacturing process. While some of these applications are tolerant of this pressure variation, others require more consistent vacuum control. Semiconductor and electronic circuit board manufacturing, for example, often require engineers to consider methods to protect the delicate materials involved. Maximum sensitivity is a must.
FLOW CONTROL SCENARIOS
The same advantages that make direct-sealing technology useful for back pressure and vacuum control make it advantageous for flow control as well.
Direct-sealing valves and regulators offer flow coefficient ranges many times wider than traditional valves and also work well in demanding applications such as corrosive chemicals or sanitary systems. Combined, these advantages make them appealing for cutting edge flow control applications such as applications requiring extremely wide flow rate ranges or experiments involving phase change.
In the flow control setup, the valve serves as a flow control valve rather than a back pressure regulator or vacuum control valve. When the diaphragm sealing the orifices is pressed against the body of the valve, flow is blocked. By adjusting the pressure against the diaphragm, the flow is also adjusted.
For example, in a standard research setup, a flow sensor with onboard proportional-integral-derivative (PID) controller is connected to an electro-pneumatic pressure regulator (EP), which in turn is integrated with the dome-loaded direct-sealing diaphragm valve. As the flow meter indicates a need for higher flow, the electro-pneumatic controller lowers the gas pressure on the dome of the direct-sealing diaphragm valve, which in turn increases the flow.
This innovative flow control approach is not indicated for most traditional flow control applications, but it has demonstrated value in applications with highly varying differential pressure, highly corrosive environments, applications with compact space requirements where a bulky actuator is not possible and in hygienic applications requiring compliance with biopharmaceutical engineering standards.
CONCLUSION
Direct-sealing fluid control technology is more complex than traditional fluid control options. It involves using an instrument gas supply equal to the supply pressure of the fluid being controlled and a separate manual or electronic pilot regulator. For many traditional processes, a globe valve or other familiar technology is the most logical choice.
For especially demanding applications, however, direct-sealing valves and regulators can often provide fluid control solutions that were previously not possible. As a result, they have been proven to perform capably in the following difficult conditions:
- Exceptionally wide flow and valve coefficient range
- Highly corrosive gasses and liquids
- Extremely high temperatures up to 932ºF (500ºC)
- Cryogenic temperatures
- Extremely low flow rates (controls Cv down to 1E-9)
Because of their unique capabilities, direct-sealing diaphragm valves have successfully contributed to disruptive technologies around the world. They have proven themselves in hydrogen electrolysis systems, fuel cell research, NASA’s Artemis Mission, and continuous flow chemistry setups used to manufacture life-saving medicines. There is no reason to believe the technology will not continue to expand as more and more engineers and researchers become familiar with it.
ABOUT THE AUTHOR
Jeff Jennings, PE, BSME, is founder of Equilibar, a manufacturer of direct-sealing diaphragm valves near Asheville, NC, and Vice President of Innovation for Richards Industrials, Equilibar’s parent company. He invented the technology behind direct-sealing diaphragm valves and holds multiple international patents. His passion is inventing and developing fluid control technology to make radical changes to improve the world.
Contact him at jeff.jennings@equilibar.com or visit the website at www.equilibar.com
RELATED CONTENT
-
Proper Care of Knife Gate and Slurry Valves
How to resolve—and avoid—field failures of knife gate and slurry valves
-
Ball Valve Basics
Welcome to the first in a series of Valve Basics articles, each focused on a major product type and written especially for newcomers to the industries that use and make valves and related products.
-
Piping Codes and Valve Standards
As with every intended use for valves, piping carries its own set of standards that valve companies and users need to understand.