Emerson Launches Pressure Relief Valves That Improve Performance and Emissions
Emerson has announced the release of two new-to-the-world technologies for the Crosby J-Series pressure relief valve (PRV) product line.
#pressure-relief #VMAnews
Emerson has announced the release of two new-to-the-world technologies for the Crosby J-Series pressure relief valve (PRV) product line. The first is a balanced diaphragm, which eliminates the need for bellows in PRVs, while providing balanced operation against backpressure to lower cost of ownership and enhance performance. The second technology is bellows leak detection, enabling remote detection of bellows ruptures in PRVs, with the capability to reduce and accurately calculate volumetric emissions in real-time.
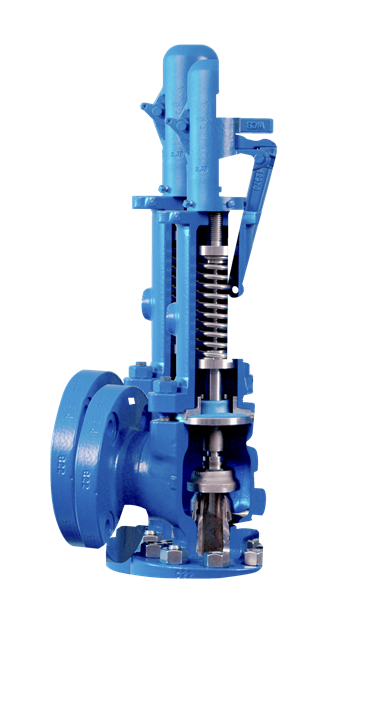
Crosby J-Series PRV with balanced diaphragm.
Photo Credit: Emerson
Where backpressure is present, spring-loaded PRVs often utilize bellows to ensure balanced operation. Data analysis from 30,000 PRV service records across different industries and valve brands shows a bellows failure rate between 2% to 6%. In other words, a plant with 1,000 bellows PRVs may have between 20 to 60 PRVs continuously operating with damaged bellows. The most common causes of bellows failures are excessive backpressure and rapid cycling. Ruptured bellows will cause fugitive emissions and may prevent valve operation at the designed set pressure, with the risk of catastrophic overpressure events.
The Crosby balanced diaphragm can replace bellows in PRV applications to address these and other issues. Its innovative design extends the backpressure limits from 60% to 80% and increases the Kb backpressure correction factor by up to 15%, expanding the application range of spring-loaded PRVs. The Kb factor is used to size PRVs when they are installed in closed systems subject to backpressure. Extending the backpressure limit and increasing the Kb factor often permits the use of smaller valves. In addition, diaphragms are inherently more resilient than bellows for higher backpressures and rapid cycling applications. Upgrading to a balanced diaphragm therefore lowers maintenance costs, improves reliability, and increases stability.
The second technology, Bellows leak detection, addresses the problem of bellows failures, which are challenging to detect and often remain unnoticed for years until removal of the valve for periodic service. Leak detection and repair (LDAR) programs may include PRVs, but their target sources for leakage detection are flanges or valve seats, so bellows ruptures will generate fugitive emissions through the PRV bonnet vent that may not be in the LDAR scope. In addition, PRV installations are often difficult to access and in hazardous locations, making leak detection difficult.
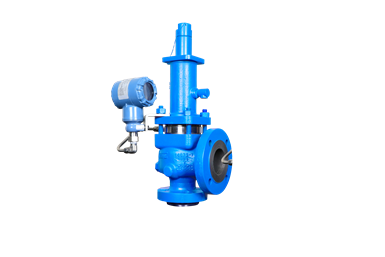
Crosby J-series bellows leak detection
Photo Credit: Emerson
The Bellows Leak Detection solution is a safer and more efficient method for detecting bellows failures and emissions. It consists of a backup piston and a Roesemount wireless or wired pressure transmitter. The backup piston can reduce emissions by over 90% in the event of a bellows rupture because it has a much smaller clearance than a standard bonnet vent, and it ensures balanced operation. The pressure transmitter provides instant timestamped notification of bellows faiture and emissions volume data in real time.
Upgrade kits for existing Crosby J-Series PRVs are available for both new technologies, and new PRVs can be purchased with these features pre-installed.
"With the growing global emphasis on sustainability, an increasing number of PRVs that currently vent to the atmosphere will require connections to flare systems to curb emissions. The resulting higher backpressures will push the limits of existing PRV designs, and the Balanced Diaphragm and Bellows Leak Detection breakthrough innovations will help our customers address this need," said Judson Duncan, president of Emerson’s pressure management business.
RELATED CONTENT
-
The Mighty Steam Trap
The steam trap is the device primarily responsible for automatic discharge of condensate from steam systems. It’s the same today as it was in the early days.
-
Pressure Relief Valve Basics – Spring-Loaded Safety Relief Valves
Learn for the first time or brush up on this common valve product.
-
CASE STUDY: Predictive Maintenance with Retrofitted Electraulic Actuation
Electraulic Actuation is a brand of electro-hydraulic actuation unique to REXA. It combines the simplicity of electric operation, the power of hydraulics, the reliability of solid state electronics, and the flexibility of user-configured control.