Improving the Reliability of Valves with Embedded Features of Today’s Smart Actuators
Texas plant expansion will achieve 320 million gallons per day of treated water capacity.
#actuators #iiot #controls
As drought conditions continue to plague the western and southwestern U.S., cities and municipalities across the country are working to address the repercussions, but groundwater reliance isn’t going to solve the problem. In Texas’ Houston-Galveston region, The Texas Living Waters Project reports that groundwater withdrawals were deemed to have caused about 3,200 square miles to sink, or subside, more than 1 foot — up to 13 feet in some places — since the area was first measured in 1836. And aquifers have lost between 300 and 400 feet, causing some land to collapse.
In response, the Texas legislature established a subsidence district in 1975 to reduce or minimize further issues with sinking. One of the main issues that comes with the subsidence is the proclivity for the low-lying areas to be prone to flooding. Other regions followed suit, enacting their own steps and regulations to prevent further subsiding in their locales. According to Greater Houston Water, surface water currently supplies about 30% of the region’s water demand; that number is anticipated to increase to 60% by January 2025 and 80% by 2035.
To help combat this regionally, the city of Houston is working with neighboring agencies to expand its new Northeast Water Purification Plant, drawing water from Lake Houston to treat and supply water for residents. Begun in 2018, a phased approach to construction and bringing the facility online has kept the project on schedule to be completely operational in 2025. More than 200 smart valves and actuators represent only a portion of the technologies that will keep this plant operating smoothly for years to come.
Aerial view of the existing plant (left) and area where expansion is currently underway.
Photo Credit: Greaterhoustonwater.com
The goal of the expansion project is to triple the output of freshwater from the plant to 320 million gallons per day at an estimated cost of more than $1 billion USD. The city of Houston has partnered with the North Harris County Regional Water Authority, the West Harris County Regional Water Authority, the Central Harris County Regional Water Authority and the North Fort Bend Water Authority to share the costs of this huge undertaking.
According to the Houston Waterworks Team website, the plant expansion will include: “conventional treatment processes like the existing plant that helps coagulate, settle, filter, and then disinfect the water to a quality that exceeds requirements set forth by the Texas Commission on Environmental Quality. In addition, an advanced oxidation process called ozonation will be constructed. Ozonation is a very powerful process for disinfecting water to help ensure that harmful organisms such as Giardia and Cryptosporidium are eliminated. Ozonation also helps eliminate taste- and odor-causing compounds, which improves the aesthetic quality of the water supplied by the plant.”
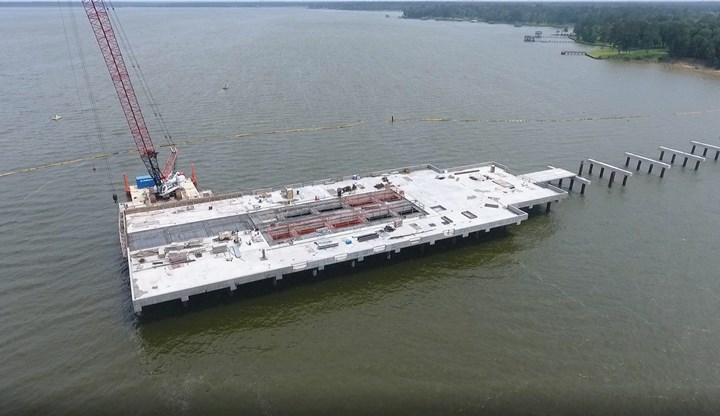
Lake Houston water is particularly difficult to treat because the lake is shallow. The new intake will alleviate some of the water quality challenges by withdrawing from a slightly deeper depth than the existing intake.
Photo Credit: Greaterhoustonwater.com
The project includes large pipes up to 120 inches in diameter, each requiring valves and actuators, some of which necessitate more than 1.7 million inch-pounds (192 kNm) of torque to operate. The valves and actuators in this plant will serve critical roles in controlling flow during the various treatment processes. Taking into account the size of the plant and the critical nature of its operations, predictive diagnostics tools are being installed to continuously detect and diagnose abnormalities before they become malfunctions. For this particular project, the software provides digital communications for system operations and diagnostic updates, helping the plant to operate flow control systems efficiently with long-term reliability. The more than 200 smart actuators installed in the system so far include Profibus digital communications for system operations.
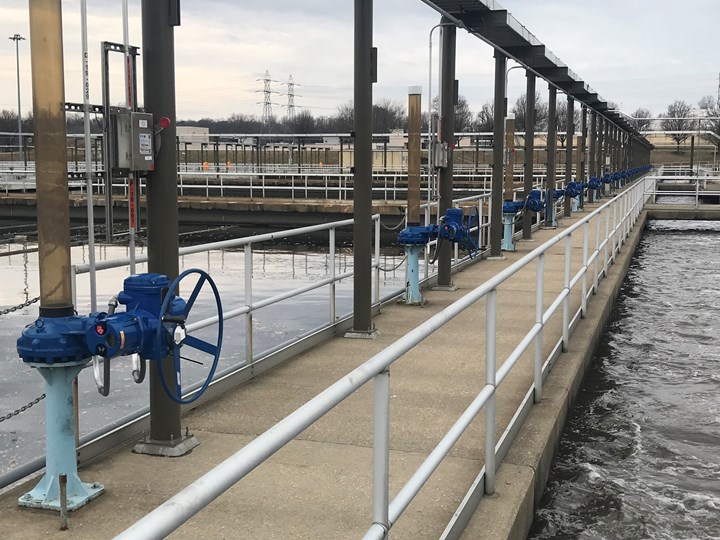
Some of the actuators installed as part of the plant expansion.
Photo Credit: Flowserve.
The actuators include built-in-self-test (BIST) features and a diagnostic engine software component that transform historical operational data into diagnostic testing of both the valve and actuator as a continuous process, performed integrally within the electric actuator. Three key operating parameters — actuator torque trends during valve travel, valve cycle counts and monitoring the valve’s span of travel versus time — serve as indicators of each actuator’s health relative to critical components such as the electric motor, mechanical gearing, position encoder, torque sensor and the motor controller. In addition, several embedded diagnostic tests can be performed, including partial stroke and emergency shutdown (ESD) tests. The primary reason for utilizing these smart systems is to inform operators of potential conditions that could hinder or prevent valve performance.
By utilizing either of the two integrated diagnostic platforms, maintenance and asset managers can receive detailed diagnostic data through the actuator’s Profibus DP digital communication network in a clear, precise and timely manner so they can take the appropriate actions to avoid unplanned shutdown conditions, prioritize maintenance during scheduled outages, and increase the facility’s efficiency. With fewer people responsible for running each plant today, it is operationally imperative to keep systems maintained. Advanced features like these aid in this process, and thus have become equally beneficial and critical.
DAVID WILLIAMS is the sales manager for USA and Canada for Flowserve Corporation. He has more than 40 years of experience in valve automation, and has worked with Flowserve Limitorque for 24 years. He can be reached at daviwilliams@flowserve.com.
SCOTT WILKERSON is the southeast regional sales manager for Flowserve Corporation. He has been with Flowserve for 17 years and has worked in the industry for 23 years. He is a certified PROFIBUS engineer and project management professional. He can be reached at swilkerson@flowserve.com.
RELATED CONTENT
-
Monitoring Valve Health via the Internet
Most valve end users are already using smart valve positioners on some control valves, but they may not have time to check the valve diagnostics software to notice if any valves are developing problems.
-
IMI Critical Engineering Launches New Steam Trap Monitoring Solution
Compact design is easy to install on either side of the steam trap.
-
Flowserve Launches New Limitorque QX Series B Quarter-Turn Smart Electric Actuator
New actuator streamlines user experience and accelerates commissioning.