New Valve Stem Packing Design Makes Reducing Fugitive Emissions Easier
Fugitive emissions commonly occur in the plant environment through equipment leaks, flaring, evaporation and spills.
#VMAnews #controls
With valves accounting for up to 70% of fugitive emissions (FE) from plants and refineries, tackling leakage is among the biggest obstacles to US industry achieving net zero by 2050.
Identified as the loss of volatile organic compounds (VOCs), FE commonly occurs in the plant environment through equipment leaks, flaring, evaporation and spills. As 1% of the total of installed valves may be responsible for most of a plant’s emissions, effective component stem packing designs are vital to addressing this growing concern.
This is the view of Ronald Simon, principal engineer for oil & gas at CCI Valve Technology GmbH in Austria (IMI CCI), who is emphasizing the importance of effective FE valve stem packing designs in reducing potential plant greenhouse gas (GHG) emissions, including methane and CO2. Specifically, he is urging facility stakeholders to review existing on-site packing solutions to ensure they meet the most up-to-date industry standards for FE and control valve qualification.
“Control valves are among the most prevalent components that contribute to fugitive emissions in an industrial setting, with rising stem control valves proving especially susceptible to leakage,” explains Ronald. “Considering that fugitive emissions can account for up to 70% of total plant and refinery emissions, action must be taken to minimize the levels of greenhouse gases (GHGs) currently emitted. Reviewing existing equipment, as well as specifying efficient and effective packing solutions that meet the highest possible standards, should therefore be a priority for plant equipment specifiers.”
To resolve this issue, IMI CCI has developed the EEEasy-Seal emission packing solution, which provides up to ISO Class AM FE leakage protection and is third-party certified to ISO 15848-1, the industrial standard for FE control valve testing. In contrast to conventional packing set designs with external springs, the EEEasy-Seal is live loaded via an internal spring utilizing the internal hydraulic pressure to optimally energize the seal, resulting in a closed, low-maintenance design.
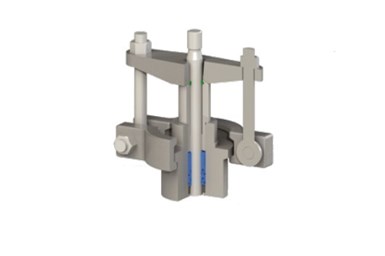
“Maintenance and Plant Integrity teams have multiple demands on their time, including keeping all plant equipment operational and safe,” Ronald concludes.
“With this in mind, traditional low-emission packing solutions may pose a problem, as they could wear faster due to higher friction and require frequent maintenance on site. They require more upkeep and monitoring from increasingly time-poor maintenance teams and give further cause for concern on unmanned platforms or vibration-sensitive systems.
“By developing technologies that use internal springs, this issue can be negated while also reducing the seal contact area, further reducing friction. As the IMI CCI EEEasy-Seal can be installed in a compact, fireproof packing box without external live loading or requiring continuous maintenance, it is well placed to tackle FE leakage concerns efficiently and effectively.”
For more information on the IMI CCI EEEasy-Seal, visit the company’s website.
RELATED CONTENT
-
Solenoid Valves: Direct Acting vs. Pilot-Operated
While presenting in a recent VMA Valve Basics 101 Course in Houston, I found myself in a familiar role: explaining solenoid valves (SOVs) to attendees. (I work with solenoids so much that one VMA member at that conference joked that I needed to be wearing an I Heart Solenoids t-shirt). During the hands-on “petting zoo” portion of the program, which involves smaller groups of attendees, one of the most frequently asked questions I get from people came up: What’s the difference between direct-acting and pilot-operated SOVs, and how do we make a choice?
-
Virtual Valve Forum and Basics Event Draws Attendees from Across the Industry
More than 200 people from across the valve industry participated virtually in the VMA Valve Forum and Valve Basics event, which included 4 days of presentations on technical, manufacturing, management and marketing, valves 101, and valve repair.
-
New Requirements for Actuator Sizing
After decades of confusion, the American Water Works Association has created new standards for actuator sizing that clear up some of the confusion and also provide guidance on where safety factors need to be applied.