Nuclear Component Testing: The Impact of Stress Wave Testing on Safety Relief Valves
Cold bar testing reveals a qualitative pass/fail status for valves, but more confirmation is needed for these critical components.
#maintenance-repair
To extend the useful life of today’s nuclear reactors and prepare for license renewals that may extend as long as 80 years, maintenance technicians must pay careful attention to the risk of deteriorating valve performance, potential leaks, and efficiency losses, especially within the steam cycle. Constant monitoring of safety relief valves (SRVs) is an important maintenance item to ensure safe and efficient power production. SRV monitoring and maintenance technology can improve performance at all power plants, not just nuclear.
All plants perform cold bar testing to verify that a refurbished valve has been repaired properly and is operating correctly prior to installation. While the valve is under steam pressure, a cold bar is inserted downstream of the valve to see whether moisture droplets form on the surface of the cold bar to detect a seat leak. Unfortunately, traditional cold bar testing only reveals a qualitative “pass/fail” status for each valve at the time of testing. Sometimes, a valve will pass a cold bar test after refurbishment, and then develop a steam leak while in service. A leaky valve can lead to lost generation, increased fuel costs, and sometimes an expensive unscheduled maintenance outage is required to replace the leaking valve.
To gather quantitative data about the status of seat tightness and potential leakage on SRVs, some power plants use an ultrasonic leak detection system that measures stress waves —vibroacoustic, structure-borne signals that are correlated to the natural frequency of the associated material. Being able to detect and monitor this shear wave energy (SWE) is an effective way to identify valve seat leakage quantitatively and identify valve internal degradation in its early stages.
This article describes how a sensor-based, vibro-acoustic monitoring system — in conjunction with cycle isolation and smart software platforms — can help power plants to detect generation losses, reduce carbon emissions, reduce the risk of forced outages and cut costs.
About the SWE Methodology
The SWE methodology combines advanced pattern recognition software, predictive technology, historical maintenance data, and routine testing to provide a basis for extending valve maintenance and testing intervals, as well as a means of early detection of valve seat leakage. Optimum spring characteristics, seat geometry and seat surface finishes are critical to valve seating tightness and subsequent leakage parameters. SWE testing can quantify these maintenance practices into a number that can be trended and analyzed.
For example, tightly seated valves typically have SWE readings that are less than the defined upper control limit (UCL) criteria, and leaky valves have UCLs greater than the defined criteria. Since the UCL is a continuous measurement of valve performance, engineers can develop a comparison trend between this data and performance data. Proper attention to these SWE measurements enables power plants to quantify maintenance practices and valve sealing ability so that reliable valve performance can be achieved consistently.
This methodology has the unique ability to not only accurately gauge seat tightness of an SRV, but also help engineers and maintenance experts determine the safety margin to cold bar failure. Inputs include thermal imaging data, valve information, data on fuel costs and thermal efficiency calculations. Outputs include heat loss calculations plus estimated monetary losses based on cost per megawatt.
The Unique Attributes of Stress Wave Testing
Stress wave measurements study seat tightness conditions all the time, such as minute quantities of steam escaping through a faulty valve seat. Unlike other forms of condition monitoring, which measure vibration, stress waves reveal minute vibroacoustic energy changes created by the relative motion of two objects. These readings can detect internal mechanical damage that is valuable for operational mitigation and maintenance planning purposes. An increase in stress waves indicates an increase in component friction and impact events, which can be an early indicator of potential issues such as high energy process leakage across valve seating surfaces.
This type of stress wave monitoring can detect valve leakage that bypasses the generation process when combined with a complete cycle isolation program. In some cases, leaking steam cycle valves can result in many megawatts of lost generation. These losses are compounded by the undetected valve leakage continuously damaging the valve, increasing the leak, and leading to additional losses in generation and increased heat rate.
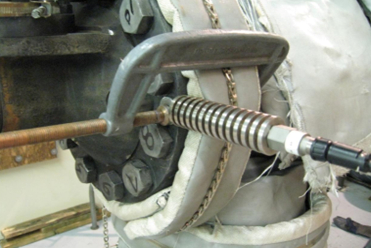
Fig. 1: Example of SWE sensor location.
Photo Credit: Curtiss-Wright
To detect stress waves, a specially designed sensor that is tuned to a specific ultrasonic frequency range is attached to the valve’s surface (see Figure 1). The energy can be measured anywhere along the acoustic path that the energy traverses. When steam escapes around the seating surfaces of a valve, it creates stress wave energy, immediately detected by the SWE sensor. This data can be combined with other plant process data, such as pressure, temperature and flow, to detect leaks at an early stageand quantify cycle losses and thermal efficiencies.
To analyze the data, a complete Valve Maintenance Optimization Program (VMOP) includes a pattern recognition software application that acquires data from DCS systems, historians, and other monitoring systems, as shown in Figure 2. The program may also use Equipment Anomaly Detection (EAD) software to diagnose equipment behavior.
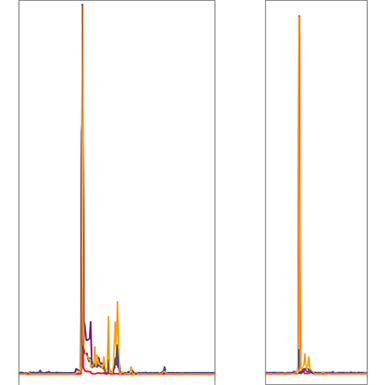
Fig 2: Example of loosely seated or simmering valve on the left and tightly sealed valve on the right.
Photo Credit: Curtiss-Wright
Case in Point: Constellation Energy
Constellation Energy is the nation’s largest producer of carbon-free energy and the leading competitive retail supplier of power and energy products and services for homes and businesses across the United States. Constellation’s nuclear fleet includes 21 reactors at 12 stations. Each reactor includes from eight to 20 safety relief valves (SRVs) in main-steam service, for a total population of more than 300 SRVs.
Over the last 15 years, Constellation has used SWE testing and cycle-isolation technology to detect and eliminate leaks throughout its nuclear fleet. The company has conducted over 1,500 valve as-left certification tests with piezoelectric sensors, in conjunction with advanced pattern recognition software to compare historic data to current test results.
SWE technology was developed as a tool to help identify potential problems before they become significant leaks. In 2007, following a refueling outage at Constellation’s Peach Bottom Atomic Power Station, a TR 3-Stage SRV began to leak excessively within a 24-hour period, about six months after it had been refurbished, passed a cold bar test, and been installed. The leaking SRV was removed and replaced with a newly repaired and as-left certified SRV during the maintenance outage. Maintenance technicians at a vendor disassembled the leaking valve to determine what went wrong. When they put the valve on the test stand, a significant leak was discovered on the pilot valve, even though the previous cold bar test certified that the valve had been operating leak tight six months before.
Remember, cold bar tests merely indicate the pass/fail status of the entire valve at the time of testing; they don’t determine the potential for future leak-free performance. SWE technology can provide individual sensor data on which of the three seats in the valve are acceptable based on historical test performance data. In this case, without supplemental stress wave data, the maintenance team would have had to repair and retest all three seats and all three disks in the valve, possibly expending unnecessary time and effort. Instead, to measure seat integrity in this valve, the Constellation team mounted piezoelectric sensors near each of the three seats. These sensors detect shock-induced stress waves at ultrasonic frequencies — a telltale sign that steam is escaping around the seating surfaces of the valve. The resulting data yielded quantitative insight into how each of the seats performed during each certification, allowing the team to focus on the SRV components that needed maintenance, as well as minimize maintenance costs for valve seats that are deemed acceptable.
Over a 15-year period, from 2008 through 2023 YTD, Constellation has tested five different types of relief valves designed for main steam service, with set pressures ranging from 250 PSIG to 2,500 PSIG, and representing a wide range of seat diameters, pressure profiles and valve seat configurations. As the results became more numerous, the knowledge of how to predict future reliable valve performance has become more accurate. This has allowed Constellation’s engineering team to determine the optimal data ‘fingerprint’ based on thousands of stress wave reports, and to evaluate the health of various types of valves against proven as-left certification baselines.
Conclusion: The Value of Continuous Monitoring
Having greater insight into the health of safety relief valves through SWE testing and advanced cycle isolation software can significantly improve power plants’ operating performance by detecting and correcting potential leaks prior to installation. This proven testing method maximizes operating efficiency, and can potentially eliminate generation losses due to leaking valves, from breaker to breaker. Early detection of potential issues makes stress wave testing an effective tool to determine spurious mechanical conditions before these conditions reach a critical damage point. A leaking valve can lead to significant power generation loss, increased fuel costs, and sometimes an expensive unscheduled maintenance outage. At fossil plants, these efficiency gains have the additional benefit of reducing the carbon footprint.
SWE technology has a proven track record when used during the refurbishment process and will prove to be invaluable when utilized for continuous monitoring. Insights gained from SWE testing activities can be applied to procedures for online monitoring of valves, while they are in operation continuously. The long-term goal is to achieve continuous monitoring of all high-energy valves throughout the entire lifecycle of those valves.
Jeremy Stevens is the manager of valve condition monitoring at Curtiss-Wright’s Nuclear Division. Phillip Twaddle is a corporate engineering safety relief valve and check valve specialist at Constellation Energy, with responsibility for overseeing the company’s SRV program.
EDITOR’S NOTE: Note: In the print edition of this article, the figure caption for Figure 2 is reversed. It is correct in this online version.
RELATED CONTENT
-
Latest Launches
Real-time valve monitoring; high-pressure severe service check valve; wireless 8-channel transmitter.
-
Safety-Relief Valve FAQ
Our company routinely receives inquiries from end users about their safety-relief valves.
-
The Rise and Fall and Rise Again of Nuclear Power
As some countries have worked to phase it out for other sustainable renewables, others find it to be the most efficient and best choice for their systems.