ITT Releases the i-ALERT3 Sensor to Expand Machine Health Protection
The sensor is designed to monitor and log the vibration and temperature of any rotating machine more quickly, accurately and cost-efficiently.
#VMAnews
Edited by Margo Ellis
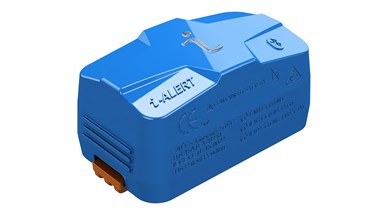
ITT Inc. has launched a new generation of technology for its i-ALERT total machine health monitoring ecosystem. It identifies and diagnoses mechanical and electrical failures in pumps, motors and other industrial machines before they occur by using a wider vibration frequency range.
The i-ALERT3 sensor upgrades i-ALERT's condition-based monitoring solution, including the i-ALERT mobile app, i-ALERT gateway, and i-ALERT Ai Platform, with best-in-class automated machine health diagnostics. The new sensor includes a field-replaceable battery to minimize replacement time and cost. Other features include robust wireless software updates that seamlessly add new features and enhance existing ones, a new magnetic flux sensor that includes electrical health analysis capabilities for motors, accurate run speed and load trending, and faster wireless data speeds using the latest Bluetooth technology (BLE 5.0) to reduce data download times with the mobile app.
“With unpredictability at an all-time high in industrial facilities, it's important for plant managers to stay agile, proactive and productive when managing equipment and processes,” said Bo Jaynes, executive director, Strategy and Monitoring and Control. “i-ALERT3's expanded capabilities enable our customers to diagnose electrical and mechanical issues much earlier, significantly improving their plant reliability and reducing unplanned downtime.”
Unplanned downtime decreases productivity and drives up costs within industrial facilities. The i-ALERT solution, an Industrial Internet of Things (IIoT) asset intelligence platform, solves these challenges using proprietary automated diagnostics to securely monitor and assess the health of machines. Either locally or remotely, the system analyzes vibration, temperature, pressure and other data to detect and resolve issues that can cause equipment breakdowns.
For more information, visit www.i-alert.com.
RELATED CONTENT
-
CASE STUDY: Stainless-steel Piping Solutions for Remote Mine Sites
Stainless-steel piping has a long history on mine sites. The robust, corrosion-resistant material is ideal for mine process piping systems that are designed to provide a long service life.
-
Valves in Oxygen Service
In his presentation at VMA’s 2017 Technical Seminar, Kurt Larson, a process control engineer for Air Products, spoke about the inherent danger of the oxygen production business and how it is particularly important for end users and valve manufacturers to work closely together.
-
ValvTechnologies and Severn Form Strategic Partnership
ValvTechnologies and Severn Glocon have reached a partnership agreement that will see collaboration between two of the world’s leading engineering and manufacturing companies specializing in innovative, high-end, severe-service valves.