Achieving Sustainability Goals Through Efficient Valve Technology
From low-power valves to cloud devices, smart valve technologies are a critical part of net-zero strategies that can help reduce energy use and industrial emissions.
#iiot #controls #automation
While every industry is feeling pressure to decarbonize and improve the sustainability of their operations, some sectors have a greater opportunity than others to make a significant impact. According to the U.S. Department of Energy (DOE), 30% of primary energy-related carbon dioxide emissions are caused by industry, and just over half of that percentage is attributed to five industries: refining, chemicals, iron and steel, cement and food and beverage.
To reduce emissions, companies from these industries are setting decarbonization goals and developing strategies to achieve these goals. As they assess sustainable technologies, many companies are integrating efficient valve technologies.
As a component used in applications across industrial plants, valves might seem like a small piece of the net-zero puzzle. However, their prevalence, as well as advancements in smart valve technologies, makes them key opportunities to reduce energy use and overall emissions. Smart valve technologies are proven solutions that can reliably reduce industrial emissions and help organizations achieve net-zero goals.
Incorporating low-power valves
Reducing emissions often starts in a fundamental way: using devices that draw less power, in this case, solenoid valves (SOVs). Process plants around the world rely on SOVs, using them as pilot valves to open and close larger ball or butterfly valves, as well as control valves for fail-safe air release during power outages.
While a single SOV uses only 6 watts (W) or less, the energy consumption of the total number of SOVs across a plant can be considerable. It’s in the best interest of a plant and the planet to use SOVs that consume the least amount of electricity possible while maintaining performance. Although low-power SOVs first debuted in the 1980s and significantly reduced power draw, they were difficult to manufacture and had low flow and low pressure ratings.
In contrast, the latest low power SOVs offer high performance as well as greater efficiency. These SOVs operate with as little as 0.55 W and feature larger orifices and standard filters that prevent clogging and allow valves to handle higher flows. Low power, high-performance SOVs are constructed with tighter tolerances and other mechanical and magnetic optimizations to further improve performance.
Unlocking energy insights through smart valve systems
While reducing energy use through low-power devices is the first step to greater sustainability, organizations can go even further by unlocking data across the plant floor to gain insights into equipment efficiency and health. Old and worn valves can go unnoticed until there is failure and pull more amperage than needed for processes in the interim. The digitalization of valve manifolds allows organizations to continuously track valve performance and device health to identify issues before failure, optimize energy use and improve sustainability. Smart valve platforms can help digitally transform processes by providing the connectivity that helps operators access device data to track real-time equipment efficiency and health.
While digital transformation may be familiar to some organizations, it may be new to others. It’s a process that a facility, system or piece of equipment undergoes that allows operators to access real-time data and use it to make decisions and act based on those decisions, improving the speed and accuracy of decision-making. For sustainability, digital transformation of valve systems can allow operators to access insights about energy use and take actions that improve efficiency and reduce emissions.
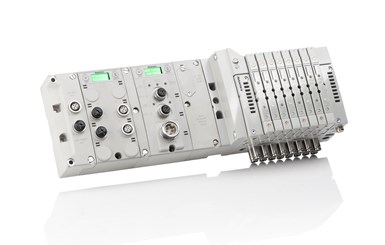
Example of an electronic fieldbus valve system that integrates communication interfaces to pneumatic valve systems, allowing PLCs to efficiently turn valves off and on.
All photos courtesy of Emerson.
Smart valve systems come in a range of options that can effectively scale connectivity to meet an organization’s needs and communicate with an existing industrial internet of things (IIoT) system. Valve systems that support IO-Link can easily connect to a process control architecture and act as a hub that provides operational data and diagnostics to upper systems for visualization. Some systems include a graphic interface that makes configuration and commissioning easy. Such systems also allow operators to troubleshoot and access diagnostic data at the device as well as within the greater IIoT system.
Some advanced valve systems have integrated Open Platform Communications Unified Architecture (OPC UA) functionality. OPC UA is a platform-independent, information technology standard for sensor-to-cloud exchange that features integrated security. Valve systems with this functionality can simplify communication with upper systems and help organizations solve interoperability challenges since data and analytics are received via the valve system and can be communicated directly to an organization’s existing cloud systems and software. No gateway is necessary unless an organization requires deeper analysis or local dashboards, which means that engineers don’t have to change a whole system or architecture to access valve data, resulting in cost savings.
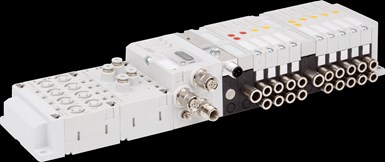
This device with OPC UA is a digital twin solution that solves interoperability challenges while improving productivity and efficiency.
OPC UA functionality can also expand the connected capabilities of a valve system and make it easier for organizations to monitor the valve system in real-time. Valve systems with integrated OPC UA capability can also allow for the integration of a digital twin. By using a digital twin, organizations can assess potential outcomes without affecting running processes, to optimize operations and improve efficiency and productivity.
Optimizing compressed air use with smart sensors
Compressed air monitoring is a significant opportunity for organizations to optimize energy use and reduce carbon emissions. Compressed air powers equipment and processes through many plants, and up to a third of the compressed air produced is wasted due to leakage. When leaks occur in pneumatic systems, the large compressors that produce compressed air must run continuously to supply enough air to power processes.
Many organizations check for leaks one machine at a time according to a schedule. This manual, periodic process gives leaks an opportunity to grow — and release compressed air — before they’re identified and addressed. This not only wastes energy, but it also comes with high labor costs of technicians and engineers to check each machine. Compressed air monitoring allows operators to remotely see what’s happening in a compressed air circuit in real time, quickly detect leaks and address them before much energy is lost.
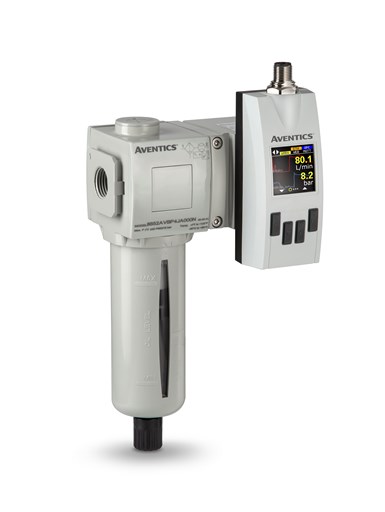
Smart pneumatic air flow sensors optimize energy consumption, prevent machine downtime and cut costs.
Some smart pneumatic sensors can continuously monitor airflow in pneumatic systems and large air lines, measuring up to eight process parameters, including energy use. These advanced sensors can act as stand-alone devices, providing actionable insights and detecting leaks in real-time, or connect to larger IIoT systems. When data is sent to hardware, such as an edge device, to be collected and contextualized and then visualized in a dashboard, operators can see trends, statistics and insights, as well as receive alerts when process parameters deviate from preset limits.
In addition to preventing leaks, organizations can also use compressed air monitoring to balance pneumatic devices to run more efficiently. Pneumatic devices have an optimal ratio of pressure to airflow, yet that ratio is often off, and processes consume more compressed air than required. By identifying that ratio and balancing pneumatic devices, processes only use the energy they need. As well as saving energy and improving sustainability, this kind of optimization can also improve production quality.
For organizations wanting to reduce consumption of additional resources, there are multimedia monitoring solutions for other utilities, including water, steam, other gases and electricity, as well.
Achieving greater control — from device to the cloud
If organizations have machines without monitoring, they have no way to track and understand how much energy is being used and why. If organizations have sensors that produce data but no way to contextualize it, that data doesn’t have much meaning. To see what’s happening on the plant floor, as well as understand why and how it affects an organization’s overall environmental impact, requires a device-to-cloud approach.
A device-to-cloud approach includes on-machine valves connected to industrial edge solutions and automation software. These scalable solutions can collect and combine multiple data streams, analyze them, present performance data and analytics through dashboards, and help organizations solve operational problems, from the machine level to plantwide.
A comprehensive device-to-cloud approach allows companies to access data and gain visibility into an operation or device that can predetermine its future state and provide clear insights into critical applications. Organizations can easily identify devices that are out of tolerance or need maintenance and quickly calibrate or service them before greater issues or failure can occur. Not only can this reduce resource use, but it can also improve OEE and safety.
As these smart technologies are highly scalable, organizations of all sizes and stages of digital transformation can begin optimizing from the device level up. A manageable yet meaningful approach is to start small. Companies can first identify the most critical applications with the greatest opportunity to improve sustainability. Then, they can install sensors to monitor performance and hardware, such as IO-link capable and OPC UA capable edge devices, to collect and report on operational activity, provide notification about inefficient operations, identify predetermined failures and more. Companies can then optimize accordingly, prove return on investment and scale up to meet their needs and sustainability goals.
Working together toward a more sustainable future
As companies set ambitious decarbonization targets and other sustainability goals, they require energy-efficient technologies and smart strategies to reach them. A comprehensive approach that starts at the valve and goes to the cloud provides great opportunity for organizations to gain a clear understanding about how their operations use energy and produce emissions and identify reliable ways to reduce their environmental impact.
Organizations ready to improve sustainability from the valve up can start by partnering with an experienced technology supplier with proven experience and a comprehensive portfolio of devices, hardware and software. That way they can receive a solution scaled to their needs and goals, as well as expert support every step of the way.
There is no single solution on the journey to a more sustainable planet. To achieve meaningful results across a plant requires multiple valve technologies working together to improve energy efficiency and reduce emissions. From low-power solenoids to smart valve islands, from compressed air monitoring to edge solutions, every technology plays a critical part that can ensure continued success — and a more sustainable future.
Andy Duffy serves as vice president of sales, America, discrete automation at Emerson. Andy has been with Emerson for 37 years, where he has held a number of sales and marketing positions spanning industrial automation. He holds a B.S. in mechanical engineering from Villanova University and an MBA from Seton Hall University.
RELATED CONTENT
-
CASE STUDY: Building the World’s Most Secure Data Center Inside a Mountain
Securing data is vital to a world that has come to depend on it. All options are on the table as long as they deliver added protection.
-
New Wireless Transmitter for Monitoring of Field Assets
Emerson’s new wireless transmitter enables remote asset control that helps cut costs, improve safety and increase productivity.
-
Pneumatic Valves: New Technology for a Digital Transformation
Principles built around the Industrial Internet of Things have guided the automation industry’s rapid adoption and mainstreaming of many production systems.