Advances in Offshore Safety
Valves are a key part of new systems to safeguard operations.
Even in 2023, there’s still something otherworldly and futuristic about offshore drilling. Drilling deep under the ocean into the seabed to extract hydrocarbons that can be refined and turned into everything from oil to plastic products — it’s a testament to sheer ingenuity!
Offshore drilling and exploration occur in some of the harshest conditions. The risks are great for both human health and safety and environmental protection. Systems continually evolve to protect all aspects of the offshore production environment. Among these are continuous electronic monitoring systems of pumps and valves, as well as other production equipment. One of the most critical of these systems is the high intensity pressure protection system (HIPPS), sometimes called the last line of defense against an overpressure event at the wellhead.
HIPPS defined
Subsea High Intensity Pressure Protection Systems (HIPPS) have increasingly become a viable safety-instrumented system response to protect downstream flowlines, flowline jumpers and other subsea production system equipment from overpressure, as well as to protect the wider environment. As upstream systems continue to reach[JD1] higher pressure and higher temperature conditions due to deeper reservoir discoveries offshore, production costs to develop these wells have increased. Operators are turning to implementing HIPPS to extend the life of existing assets. HIPPS allows the high-pressure flowlines of an existing system to be safely derated between the manifold and host platform by reliably isolating the high-pressure product before the break of the lower pressure rated flowline. Proper HIPPS design focuses on the safety and reliability of the entire system from reservoir to topsides.
A typical HIPPS architecture consists of three pressure transmitters that constantly record the line pressure fed to a logic solver. In the event of an over-pressure condition, the logic solver initiates a shutdown operation of two consecutive fail-close valves installed on the same line, thereby shutting down fluid flow. Installation of a HIPPS may avoid blow off and flaring of carbon dioxide or other toxic gases, allowing companies to avoid incurring penalties for emissions. For SIL3 rated systems (see sidebar), at least two transmitters are required.
A SIL 3 quick exhaust valve in redundancy can be inserted into the system to open and dump hydraulic fluid, which reduces the pressure in the actuator that closes the HIPP valve[JD2] . By managing this fluid, this operation reduces over-pressurization and eliminates the potential of unplanned and unwanted release of hydraulic fluid.
Solenoids are typically used to control HIPPS valves, and can be powered hydraulically, pneumatically or with process gas. If the solenoid loses power, the valves automatically close. The time to close must be carefully set to prevent system or equipment damage.
HIPPS must be tested to meet multiple parameters, including the ability for the system valves not only to close, but to close in time to prevent catastrophic damage. Partial stroke testing is suitable for maintenance purposes, but full stroke tests must be undertaken to test the integrity of the system.
Well exit pressure can fluctuate, increasing exponentially throughout the lifecycle of the well, and can cause extremely hazardous conditions. Therefore, a HIPPS is one critical system for well safety. While operators may think that relief valves and flares that match the full capacity of wells are useful, this configuration can be very dangerous. HIPPS are better solutions to maintain safety of the system, with only a small relief valve required for manual depressurization of the system for maintenance.
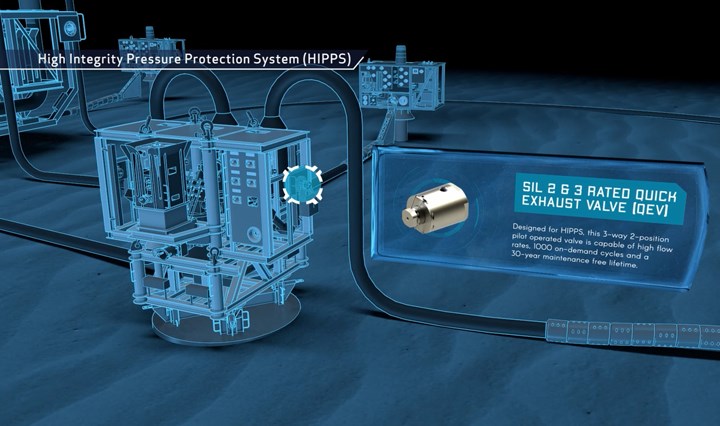
Rendering of a high-integrity pressure protection system (HIPPS).
Photo Credit: Gilmore
Other common subsea safety systems
Well control systems prevent uncontrolled, catastrophic release of fluids from the subsurface formations. These systems are comprised of a blowout preventer (BOP) and an accumulator. The BOP, also called a BOP stack, is an assembly of valves that are placed in redundant configurations, that are capable of isolating and controlling the high-pressure fluids from the well. There are a variety of valves on BOPs, including an annular preventer, pipe rams, blind rams and shear rams.
An annular preventer is a doughnut-shaped element to prevent fluid from flowing and to close the annular space. Pipe rams are notched and used for specific-sized pipe, and work by closing around the pipe to seal the annular space. Blind rams are less common and work by isolating the drill pipe and the annular space by crushing the pipe and pinching it closed. Shear rams work by shearing off and closing the pipe. BOPs also have accumulators which store compressed energy to operate the blowout prevents even if the power to the rig above is not operational. BOPs often have more than one accumulator.
The Deepwater Horizon failure occurred when the shear ram on the system punctured the pipe and sent oil and gas surging to the surface for almost 90 days until it was contained and controlled. The subsequent investigation found that the shear ram was prevented from functioning properly because the pipe buckled. There were also instances of backup battery failures and miswiring that would have had an affect on the shear ram. Since the 2010 event, the American Petroleum Institute has published more than 200 new or revised standards and recommended practices for offshore drilling exploration and production.
Even with the risk of subsea drilling and exploration, the risks offshore that are more likely to cause harm or loss of life include aircraft crashes when transporting people or supplies to rigs; diving accidents; in-water vessel collisions; crane accidents, and other equipment failure or spills.
Regulations and oversight increased
In addition to the Code, standard and regulatory changes, four major offshore operators founded the Marine Well Containment Company (MWCC) as an independent, non-profit with the mission of providing immediate response to any deepwater incidents in the Gulf of Mexico (GOM). MWCC offers containment systems and services to all member companies operating in the GOM, or to companies who name them as their well containment response provider on their drilling permit applications with BSEE. Another group of operators and non-operators have formed the Helix Well Containment Group (HWCG) to expand their capabilities in responding to subsea well containment to protect people, property and the environment.
The Marine Well Containment Company and Helix Well Control Group
To better prepare for a potential well control incident, four major operators founded the Marine Well Containment Company (MWCC)18 in 2010 as an independent, not-for-profit organization. MWCC’s overall mission is to be continuously ready in providing immediate response to a deepwater incident in the GOM to stop any unplanned discharges and capture the liquid aboard its vessels. With its membership now up to 10 operating companies, MWCC represents the majority of deepwater wells and production currently in the GOM. The organization’s containment system and services are available to any operator in the GOM that is a member, or once a nonmember company enters into an agreement designating MWCC as their well containment response provider when filing its drilling permit application with the Bureau of Safety and Environment Enforcements, an agency within the Department of the Interior (BSEE). In addition to MWCC, a consortium of GOM deepwater operators and non-operators have formed the Helix Well Containment Group (HWCG) with the common goal of expanding capabilities to respond to a subsea well containment event to protect people, property, and the environment.
The BSEE has spearheaded a number of changes since its inception, from well design and workplace safety regulations to enhancing corporate accountability. Among the most significant are:
- The 2010 Drilling Safety Rule that requires that permit applications for drilling projects meet heightened standards for well design, casing and cementing;
- An increased number of inspectors and engineering workforce to review permits and ensure compliance with standards;
- The 2010 Safety and Environmental Management System (SEMS) rule empowers field-level personnel with the ability to make safety management decisions and strengthens oversight by requiring third-party audits;
- Enhanced blowout preventer performance, testing and maintenance prior to drilling starting;
- Operators must demonstrate that they have the necessary equipment or a contract with a partner for subsea well control and containment, including a capping stack;
- More stringent regulations for future exploratory drilling in the U.S. Arctic outer continental shelf; and more.
Offshore exploration and drilling remain a challenging endeavor under any circumstances. But with the improvements in safety equipment, development and implementation of applicable Codes and standards, more industry and government collaboration and oversight, and continually emerging technologies, major advances have been made in recent years and will continue in the future.
RELATED CONTENT
-
Testing of Hydrogen Valves
Valves are used to control all types of fluids, and while some are easy to manage, others can be a challenge. At the top of the challenging list sits hydrogen, the smallest, lightest molecule known to man.
-
The Limits of Standard Manual Globe Valves for Throttling
A common practice in process services is to use manual globe valves with hand wheels for regulating flow.
-
The Role of Valves in HAZOP Studies
Process hazard analysis (PHA) is required by U.S.