Advances in Pressure Regulator Technology Helps Boost Semiconductor Fabrication Yields
In addition to product innovations, supplier relationships is key to keeping fabs operating at peak production levels.
#pressure-relief #components
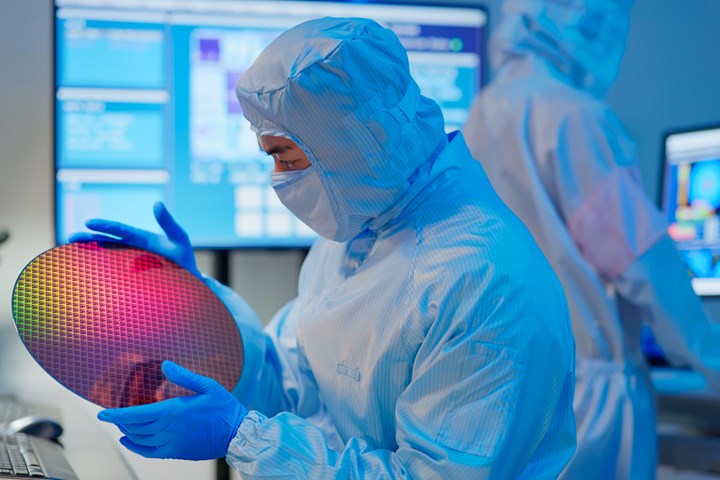
Demand for virtually every kind of semiconductor chip continues to grow as digital technology is woven more deeply into every aspect of our modern world. That demand places unrelenting pressure on fabs to increase production yields, challenging manufacturers to find new technologies and solutions to boost productivity while simultaneously improving manufacturing quality. For the semiconductor industry, this can be a complex and costly challenge. When manufacturers have well-established, multibillion-dollar production systems and controls, it can be difficult to convince them to invest in integrating new production, automation and data analysis tools. However, there are incremental technologies becoming available, such as innovative new gas delivery components, that offer ways to improve semiconductor efficiency and productivity, one pressure regulator at a time.
Upgrade key gas delivery system components to improve yield
Updating or modifying any part of an established chip manufacturing process is challenging. First, it can be extremely expensive in terms of engineering and equipment costs. New system integration can also prove cumbersome and present costly disruptions to the larger operation. These challenges often lead manufacturers and their suppliers to examine smaller systems and components within the process to try to identify opportunities for yield improvement, and one system and component that are getting a lot of attention are the gas delivery system and the pressure regulator.
Because there are so many gas delivery systems involved in semiconductor manufacturing, the pressure regulators that control gas flow have taken center stage as a critical component in the battle for better yields. The more precise pressure and flow control and improved cycle times afforded by newer pressure regulator designs are helping manufacturers more tightly control gas delivery, which is directly tied to higher product quality and higher yield. In the bigger picture, these component-level improvements can also assist in reducing material waste and equipment wear and tear, all of which contribute to alleviating the semiconductor shortage that manufacturers are working so hard to resolve.
Critical value of high-purity components in gas cabinet designs
To understand the positive impact a high-purity pressure regulator can have on a semiconductor manufacturing operation and its yield, consider a typical gas cabinet within the larger context of gas delivery systems. Gas lines start out 100% clean and free of impurities, so regulators that are introduced into the process must also be 100% clean. This means regulator suppliers must do their part during the manufacturing of high-purity regulators to ensure no impurities are introduced into the process once the regulator is installed. For example, some pressure control regulators are manufactured specifically for high-purity applications and are assembled in an ISO 4 clean room and vacuum bagged to protect cleanliness from the point of manufacturing through transport and installation into the system.
Cleanliness, however, is only part of the story of a pressure regulator’s impact on yield. Equally important is the regulator’s ability to deliver precise flow control. When the gas supply reaches the gas cabinet, the regulator is responsible for controlling the flow of the gases that are distributed to the valve manifold boxes that feed clean room tools. Once gases reach the clean room, flow precision is absolutely critical for delivering the high product quality that results in high yields, and any fluctuations in pressure or flow can compromise this quality.
Recognizing the critical role of regulators and their potential to impact yields, industry-leading suppliers like Emerson have focused their engineering expertise on advancing regulator technology to control flow more precisely. As a result, newer sensor-equipped pressure regulators are now available that enable manufacturers to capture, analyze and respond to regulator data automatically without operator intervention. Additionally, advances in the pressure regulator’s internal design, such as reductions in volumes and modifications to the diaphragm, have improved cycle times by reducing the amount of time required to purge the regulator during changeover.
Digital pressure regulators upgrade precision and control
Continuing with the gas cabinet example, a common scenario in this area of gas delivery is for personnel to check pressures by reading gauges inside the cabinet and manually recording the readings. This traditional approach introduces at least three opportunities for error into the manufacturing process. First, there is an opportunity for human error in recording the pressure data. Second, there is an inherent delay between when the operator records the data and when action is taken in response to the data. Lastly, it requires the operator to come in close proximity to the gas cabinet to read the pressure gauges, and in some cases the operator must open the cabinet to make pressure adjustments. Each of these steps adds unnecessary risks into the process, which can be resolved by integrating modern pressure regulator technology.
For example, small changes in pressure over time may go unnoticed when data is captured manually, and minor fluctuations are often not identified and corrected until after they have negatively impacted chip quality and reduced yield. Comparatively, digitized pressure regulators can be directed to respond to minute pressure deviations and to automatically make corrections without operator intervention. This removes the time delay associated with traditional troubleshooting and manual control, and it prevents out-of-spec conditions from persisting to the point where they impact quality and yield. Applying automation to pressure regulators in this way also minimizes operator safety risks by reducing or eliminating the need for them to come in contact with the gas cabinet.
Incremental digitization of components like pressure regulators and subsequent digitalization of the larger gas delivery systems can present a variety of new opportunities for process improvement and safety in the future. In addition to truly optimizing yields, manufacturers will also be able to instantly identify and correct root causes of processing issues, make processes inherently safer by distancing operators from dangerous gasses and equipment and extend equipment life through better preventive maintenance. Semiconductor manufacturing of the future will also allow facility managers to plan downtime using predictive maintenance tools informed by real-time performance data.
Advances in pressure regulator mechanical features
While digitization of pressure regulators is an important part of high-precision gas delivery, as illustrated by the gas cabinet example, there have been other equally important innovations in the mechanical features of regulators that are also helping to control contamination.
For instance, new regulator designs include springless and threadless models with lower internal volumes and fewer media contact points to minimize particle accumulation and contamination. Regulators may also feature a tied diaphragm design that creates a positive seal in the event of internal leakage at the outlet. And leak integrity within the regulator body has been improved with newer metal-on-metal diaphragm-to-body seals. These updated mechanical features allow pressure regulators to deliver safer and more reliable performance and contamination control in many types of ultrahigh-purity gas delivery systems, including bulk specialty gas systems, gas cabinets, valve manifold boxes and other tool hookup and pressure control systems. The standardized part numbers also make selection easier for distributors and end users.
Key criteria for selecting component suppliers
For manufacturers who need to replace failing pressure regulators within their gas delivery systems or who wish to update their regulators to these newer designs, partnering with a knowledgeable supplier that has semiconductor manufacturing expertise and experience is critical to success.
First, find a supplier that has ISO-rated clean rooms to ensure that the regulators you purchase have been manufactured in an ultra-clean environment using an ultra-clean manufacturing process. Also, make sure your supplier has a readily available supply of products that meet industry standards and that have a reputation for performance and reliability. This will expedite access to repair and replacement parts, which is essential for avoiding prolonged downtime.
Next, local support from a supplier can prove invaluable, as it allows the supplier to become familiar with a manufacturing operation, and it enables the manufacturer to become familiar with the supplier's product families. This aspect of the manufacturer-supplier relationship is beneficial for both parties, enabling them to work in harmony to quickly resolve short-term issues as well as focus on longer-term process improvement goals. Engaging a supplier in manufacturing challenges and goals can also lead to advances in control technologies that are beneficial for the manufacturer as well as for the industry at large.
Lastly, attention to supply chain disruptions and raw material shortages should also play a role in choosing a supplier. Those who are knowledgeable about raw material resources and supply dynamics and who proactively prepare and plan for disruptions may offer a higher level of supply security.
Every component counts
Innovations in pressure regulators are just one example of how a broad range of components are being modernized to meet the digitalization needs of today’s manufacturers. By fully digitalizing the entire manufacturing process, with components such as pressure regulators becoming “smarter,” more precise and more responsive, manufacturers have significantly improved ability to monitor and control processes in real time. They can respond to issues faster, before they slow down production or impact quality — a crucial need for semiconductor manufacturers to sustain their yields and meet unprecedented demand.
As industries continue to invest in digital transformation, small changes with improved, digital pressure regulators can create big improvements, creating momentum that moves manufacturing forward. This approach is a more manageable way to reap the benefits in quality, safety and yield that new component-level technologies offer.
RELATED CONTENT
-
The Dos and Don’ts of Isolating Pressure Relief Valves
Typically, isolation valves are used to block off a pressure safety valve (PSV) from system pressure, so that maintenance on the valve or related equipment can be conducted without a shut down.
-
Operational Basics of Safety Valves
These spring-loaded valves provide overpressure protection for downstream equipment.
-
Introduction to Pressure Relief Devices - Part 1
When the pressure inside equipment such as boilers or pressure vessels increases beyond a specified value, the excess pressure may result in a catastrophic failure.