An Introduction to Axial Flow Check Valves
Check valves are self-actualizing devices that respond to both pressure and flow changes in a piping system.
#knowyourvalves #gate-globe-check
The primary purpose of check valves is to permit flow in one direction while prohibiting or stopping the flow in the opposite direction. The key point is that the normal resting state of a check valve is the closed position.
WHY IS A NON-SLAM CHECK VALVE USED?
When flow is reversed in a pipe, this can cause hydraulic shock waves to pass through (also known as water hammer). This can cause severe damage to equipment in the pipeline if measurements are not taken to prevent this. The introduction of the correct check valve, in a fully closed position during reverse flow can prevent this from occurring and causing severe issues at the site.
Valves that prevent water hammer and close rapidly without slamming are called non-slam check valves.
HOW ARE AXIAL FLOW CHECK VALVES USED?
Axial check valves are specifically designed for fast-reversing systems where backflow is a constant concern. It is categorized as a non-slam check valve as the valve closes without slamming meaning no excess pressure spikes are created. Most axial flow check valves are spring-loaded, with a single low-mass disc, which facilitates a fast, dynamic response to reduction in flow. Due to having a single disc and spring when the disc is opening, the force is balanced resulting in an even flow.
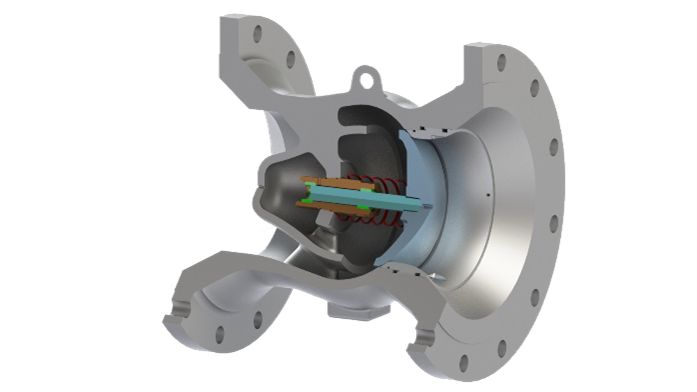
METHOD OF OPERATION
When pressure differential between the upstream and downstream side of the valve exceeds cracking pressure of the spring, the obturator will move and allow flow. The flow area of the valve decreases steadily down to the seat diameter; this is the venturi design.
As a result of the venturi design, the reduced flow area increases the kinetic pressure and reduces the static pressure allowing the valve to fully open quickly. The spring is selected so that the disc is fully opened and stable against its backstop under normal flow conditions.
When a noticeable reduction in flow occurs, the spring reacts early against the force of the reducing flow.
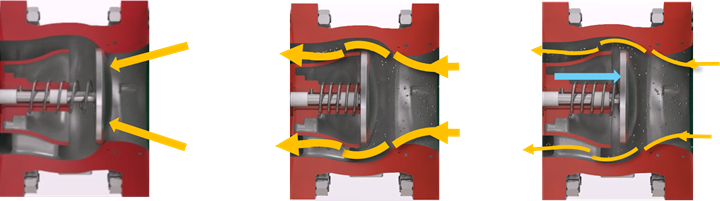
PRODUCT DYNAMIC PERFORMANCE COMPARISON
Simple conventional swing check valves tend to have a very poor response. Under dynamic conditions, relatively long response times are experienced. This yields high reverse velocities resulting in slam and unwanted pressure surges.
Dual plate spring-assisted valves versus conventional swing checks are designed with small plates, which have less inertia than a single thicker disc. Pre-loading with a spring provides a closing force at all angles, thus helping to reduce response time.
As mentioned, axial flow check valves have an excellent response and are recommended where a high-level performance is essential. As flow decelerates in the pipeline, the forces acting on the disc are reduced, and the spring is able to overcome these smaller forces causing the valve to close. Short displacement of the disc combined with axial spring assistance greatly reduces the response time giving a fast slam-free response with minimal reverse.
Axial flow valves:
- Cover any service conditions (lowest to highest deceleration systems)
- Have the fastest response time and are non-slam and mitigate against pressure surge or the impact of water hammer
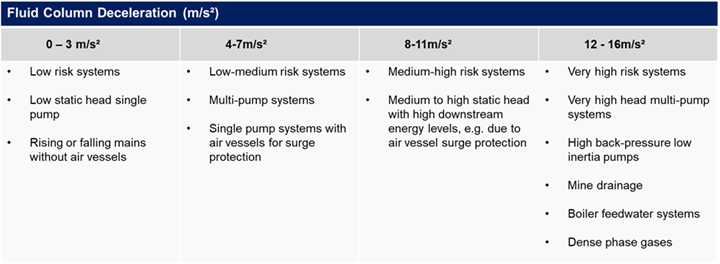
STANDARD FEATURES
The base valve design is available in various body configurations to suit the customers’ needs for industry standards, specification, weight and connection requirements. The majority of axial flow check valves will be sold as flanged.
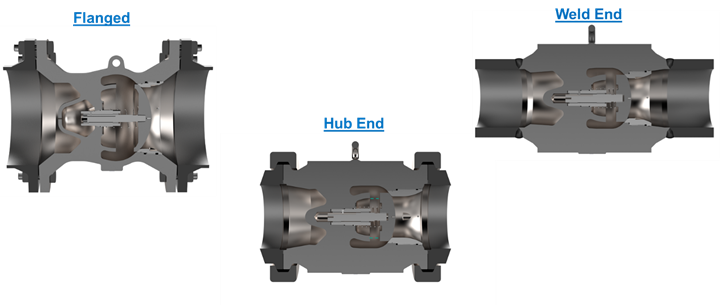
STANDARDS
The list below summarizes the most important standards for axial flow check valves:
STANDARD |
DESCRIPTION |
PUBLISHERSUPPLIER OF CERTIFICATE |
|
ASME B16.34 | Applies to new construction and covers pressure — temperature ratings, dimensions, tolerances, materials, nondestructive examination requirements, testing and marking for cast, forged and fabricated flanged, threaded and welding end and wafer or flangeless valves of steel, nickel-base alloys and other alloys.
|
American Society of Mechanical Engineers (ASME) | |
ASME B16.10 | Covers face-to-face and end-to-end dimensions of straightway valves and center-to-face and center-to-end dimensions of angle valves. | ASME | |
API 598 EN 12266-1, 2 |
Defines inspection, examination, supplementary examinations, and pressure test requirements for resilient-seated, nonmetallic-seated (e.g., ceramic), and metal-to-metal-seated valves of the gate, globe, plug, ball, check and butterfly types. | American Petroleum Institute (API) | |
ISO 5208 | Defines examinations and tests that a valve manufacturer needs to act upon in order to establish the integrity of the pressure boundary of an industrial metallic valve and to verify the degree of valve closure tightness and the structural adequacy of its closure mechanism. | International Organization for Standardization | |
API 6D | API Specification 6D is an adoption of ISO 14313: 1999, Petroleum and Natural Gas Industries-Pipeline Transportation Systems-Pipeline Valves. This international standard specifies requirements and gives recommendations for the design, manufacturing, testing and documentation of ball, check, gate and plug valves for application in pipeline systems. | API |
TYPICAL APPLICATIONS
Although axial flow check valves can be utilized in a multitude of applications, a growing number of niche sectors the valves have primarily been utilized in the following:
Oil and gas production, including midstream:
- Regasification
- Liquefaction
- Centrifugal compressor discharge
- Fire water lines
- Oil/steam separation
- Steam and CO₂ injection
- Oil and gas gathering systems
Chemical and pharma:
- Chlorine
- Phosgene
- Aromatics
- Polymers
- Acids
- Air separation
- Caustics
Petroleum refining and petrochemicals:
- Hydrogen
- Cracking
- Steam
- Crude oil
- Ethylene
- Propylene
- Steam
Power:
- Steam
- Condensate
- Boiler feed pumps
- Cooling towers
- Service water recirculators
- River water intake
- Renewables
The most important thing to remember is that axial flow check valves are specifically designed for fast-reversing systems where backflow is a constant concern.
ABOUT THE AUTHORS
Ian Noble is the Global Business Line manager for the Crane range of Engineered Check valves, working within the Crane Process Flow Technologies (CPFT) business segment. Crane Process Flow Technologies segment is a global provider of highly engineered products and systems, serving chemical, petrochemical, pharmaceutical, water and wastewater and general industrial market among others.
John McIlroy has worked in manufacturing for more than 30 years, including 15 in the valve industry. He has had roles in check valve technical sales, applications engineering and manufacturing. McIlroy’s current role of application specialist for Crane Engineered Check Valves has a wide scope from direct customer support, resolving immediate system issues where the correct check valve can be a solution, to technical presentations around the application of check valves within industries like oil and gas, petrochemical, hydrogen production, LNG and renewable energy.
RELATED CONTENT
-
Fundamental Operation of Pilot-Operated Safety Relief Valves
In this second of a series, we explore another type of pressure relief valves used in common applications.
-
Pinch Valves: An Uncomplicated Valve With an Important Purpose
Used in on/off or throttling applications, choosing the right style pinch valve depends on the application.
-
Auxiliary Connections: Why We Have Them
Valves are a vital part of the piping systems that run like arteries and veins throughout industrial plants.