Erosive Pulp & Paper Systems Require Proper Valve Selection
As new recycled paper plants are being built for the first time in decades, not only do paper companies have opportunities to grow revenue but so do service suppliers such as valve companies.
#maintenance-repair #actuators #ball-butterfly-plug
As a member of the valve industry, you likely recognize the number of valves we encounter in our everyday lives. They are prolific, in everything from our water taps to helping power our homes in energy applications. But have you ever stopped to think about how much paper you consume? This includes so many things we interact with and use every single day -- office printing paper, toilet paper, labels, product packaging and shipping boxes, just to name a few.
During the height of the pandemic when many people were ordering items to be delivered to their homes, the pulp and paper industry shifted much of its production to paperboard and corrugated papers used to make packaging for consumer goods and final boxes to ship them. There was less demand for writing and printing paper as people worked from home, so paper companies used their inventory to meet the lower demands. Today, three years later, there are ongoing shortages affecting all markets that use paper, including the printing industry which produces this magazine. This has led to several new paper plants coming online, and the retrofitting of existing plants to manufacture recycled paper to meet the market needs.
In mid-2021 Green Bay Packaging inaugurated a new plant in Wisconsin – the first new paper mill in the U.S. in 30 years. Graphic Packaging in Waco, Texas, is currently converting a recycled corrugated plant to a paperboard plant at an expected cost of $1 billion USD. And Pratt Paper is opening new recycled paper mills in Ohio and Kentucky, and a co-located corrugated box factory at the same site in Kentucky to manufacture market-ready corrugated products from the mill’s output. There is a lot of investment going into mills across the U.S. and around the world, and myriad opportunities for valve manufacturers to sell to and service valves in this industry.
Another reason why more recycled paper plants are coming online is consumer demand for recycled materials, with paper being high on the list. The pulp and paper industry contributes not only to municipal waste but has an environmental impact. Many paper companies are now reforesting thousands of acres of land to replace the trees removed in the past, and they have shifted to using specific wood that is easily regrown and processed. Pulp and paper processing also uses an extraordinary amount of water. The United Nations estimates that 12% of water withdrawals globally are for pulp and paper plants. With droughts globally and climate change at the forefront of many, recycling paper just makes sense.
Much of our trash stream is also paper and other products that could be recycled. Consumers are getting more conscientious about recycling their paper, more than other products, according to recent statistics. The EPA estimated in the U.S. in 2018 that 23.1% of municipal solid waste (MSW) was paper products that could have been recycled. However, they also estimate that approximately 46 million tons of paper and paperboard were recycled in 2018 for a recycling rate of 68.2%, higher than all other materials in MSW. Many U.S. municipalities are making recycling a compulsory part of their waste collection, which should only help these numbers continue to improve.
But recycled paper plants consist of systems that see extraordinary amounts of erosive and abrasive materials processed every day. Proper valve selection is critical to ensuring the plant can run as efficiently as possible and avoid unnecessary stoppages due to equipment failure. Unlike large processing plants such as power or chemical which have scheduled maintenance shutdowns that may last for weeks and are planned for many months or years in advance, paper plants are much smaller operations and work on much shorter timelines in duration and frequency, with maintenance shutdowns happening as often as every eight to ten weeks, or sometimes a few months, depending on volume.
We spoke with Shahrum Iqbal, vice president of control valves and automation at Bray International Inc., to learn more about the process of making recycled paper, the valves involved, and the necessity to use valves made of the right materials and at the right size to withstand the harsh environment of a paper mill.
Process of Recycled Papermaking
For this article, we are only going to focus on the first phases of recycling paper into pulp. There are several downstream processes that occur which we won’t cover in this article but will look to explore in future content.
To make recycled paper, the feedstock or starting paper needs to be broken down back to a fiber state. This process shortens and weakens the fiber each time it is recycled, which is possible an average of 5-7 times before it becomes unusable.
The paper manufacturing process is very challenging as the pulp is very viscous, and a variety of abrasive materials are filtered out through the manufacturing process that is very damaging to fluid systems, particularly in recycled paper as it contains what the industry calls “rejects,” or foreign objects that make their way into the processing.
Manufacturing recycled paper starts when consumers put waste paper and other recyclable items into their recycling bins. From here, the materials are sent to re-sorting facilities which remove non-recyclable materials and sort what’s left into the appropriate stream. Paper bales are created, often sorted by type of paper such as brown and corrugated, white writing paper, etc., and delivered to recycled paper plants.
Once the bales arrive, they are broken up and placed into a large vessel called a pulper that contains water, and in some cases chemicals, to break the materials down to the fiber level turning it into a paste-like consistency. From the pulper, the slurry goes into a cyclone. A spinning blade mechanically assists the chemicals and water to help form the cyclonic action. Within this vessel there are often residual metal staples, glass, sand and other abrasive contaminants, called rejects, are being agitated and sorted from the fibers. It’s also heated to burn off lingering contaminants and grease, particularly from food packaging. The output is called brown stock or paper pulp, which then is expelled from the vessel through large control valves, 10- to 16-inch valves.
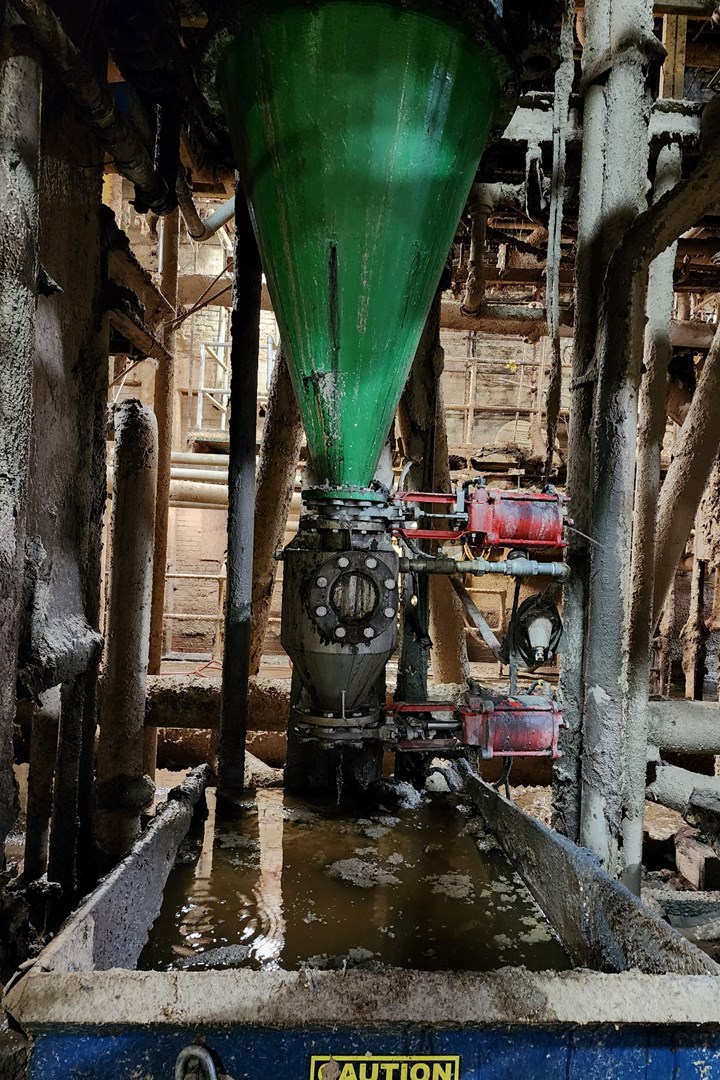
Each cyclone in the recycled pulping process expels rejects through a gate or knife valve that experience high erosion.
Next are multiple steps of cleaning and filtration. The steps consecutively remove finer and finer particles. The pulp stock enters a series of cleaners and cyclonic machines that spin the stock to remove rejects that fall to the bottom into a screen. At the bottom of the cyclone is often a butterfly valve or gate valve, but because of the harsh environment, it may only last a few weeks. This is why it is critical for users to order valves with the right packing and materials to extend the life of the valve. Typically, the valve packing would be made of PTFE or graphite, which would have significant shortcomings in this application. Valve manufacturers offer solutions specific to this application, including one from Bray that has a copper scraper with high-performance packing made from Kevlar, a material that is more durable and resistant to erosion. This specific valve also has purge ports on the valve body to make it possible for operators to use high-pressure water to clean the valve and further extend its life. The stock is further cleaned with a series of cleaners to remove the finer rejects. Control valves in these applications see high wear and tear from the abrasive media. These valves are typically designed knife gate or segmented control valves with abrasion-resistant coatings and extremely hard material of construction to withstand the sand, glass, staples, and other metal fragments often flowing in the media.
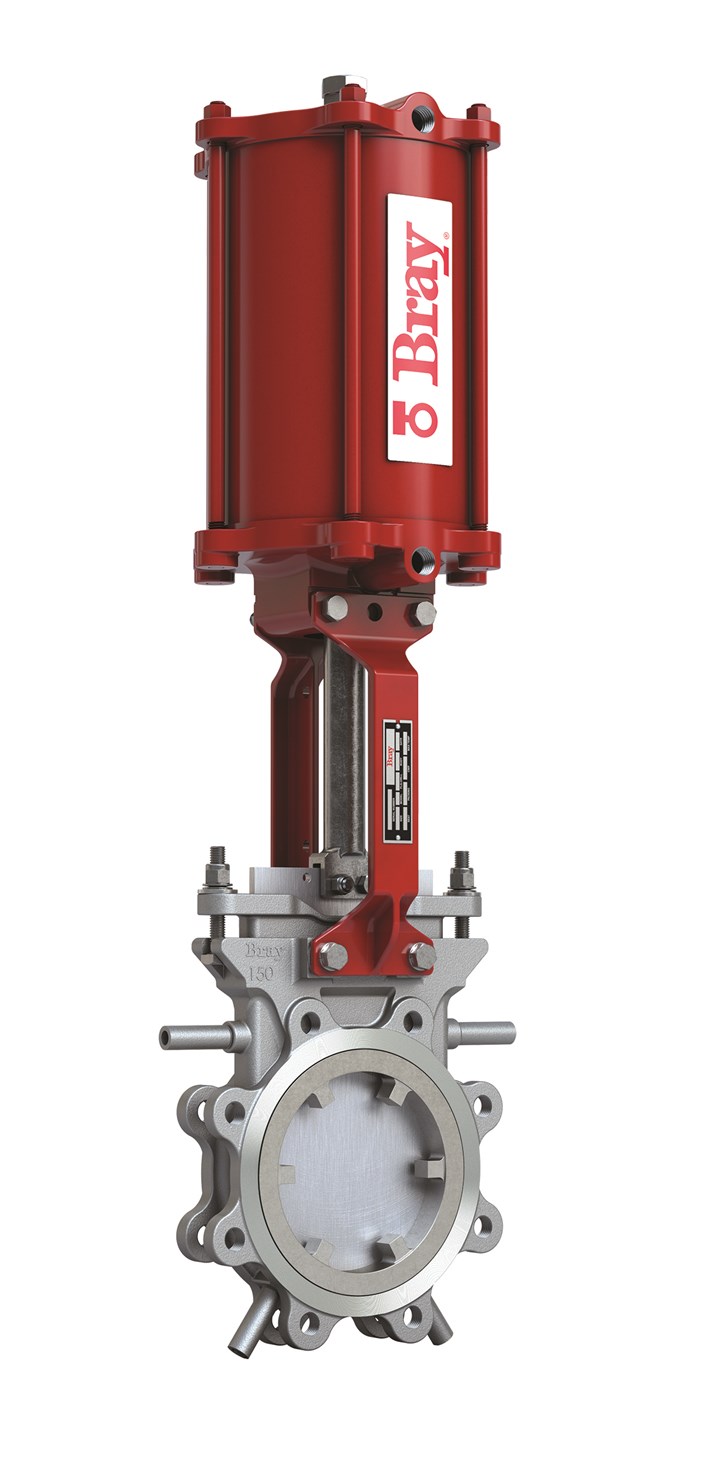
Bray knife gate valve Series 942 featuring replaceable vortex breaker with A36 steel and tungsten carbide overlay for extended duty.
Next, once the pulp is made, it is run through a series of machines to dry it to convert it to sheets of material that can be sent to paper mills and converted into various types of paper products – from corrugated cardboard to paperboard used in consumer goods packaging. But throughout this system the pulp material runs through a series of pipes, tubing, valves and other process control systems, putting a great strain on these components because of the solids that abrade and degrade the controls. Iqbal said this is where the material selection becomes critical.
“It’s not just the packing material of the valve, or the trim materials that see the main flow through them, but also the area around the stem that you have to consider,” Iqbal shared. “The design of the valves is also critically important because some valves have more cavities than others and the more cavities they contain the higher the risk of breakdown or failure. As the rejects or solids flow through the system, they have a chance to build up on the internals of the valve and the valve drive train, jamming them and preventing them from operating properly or at all.”
Paper manufacturing and recycling are completely reliant on fluid systems as each phase involves an addition or subtraction of liquid from the pulp. Iqbal says, depending on the size of the plant, the number of valves can number in the thousands, and these are just the process valves. If you work in one of these plants as a maintenance or reliability engineer, you already know this and spend your days very busy repairing and replacing components.
“For a 1500-ton-per-day plant, you’ve probably got about 2000 to 2300 valves, in a combination of manually operated, electrical, pneumatic, etc., and different types of valves. Critical valves are always going to be actuated and controlled with automation.”
Of these control valves, Iqbal said, large numbers of mills use a segmented ball valve that is optimized for this application. These valves were designed to reduce the impact of the abrasive environment in pulp and paper plants. The design offers a shearing action to cut through pulp fibers and precise controllability which is often required in this process. The other valves used in automated applications in pulp and paper plants are knife gate valves and ball valves.
Materials selection
Iqbal said: “I’ve been in several plants and seen the valve body blow out, and lots of other failures in various mechanisms including valve leaks, jamming and more. This creates a lot of maintenance headaches at these plants and stops processing altogether.” This can be due to several factors: the abrasive nature of the process, improper materials selection, improper valve selection and improper sizing are among the most common.
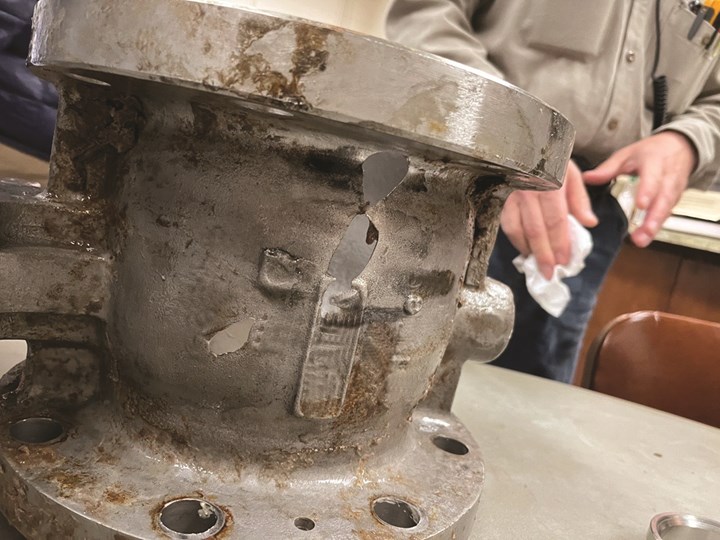
Large holes formed in the body of this valve after a few weeks.
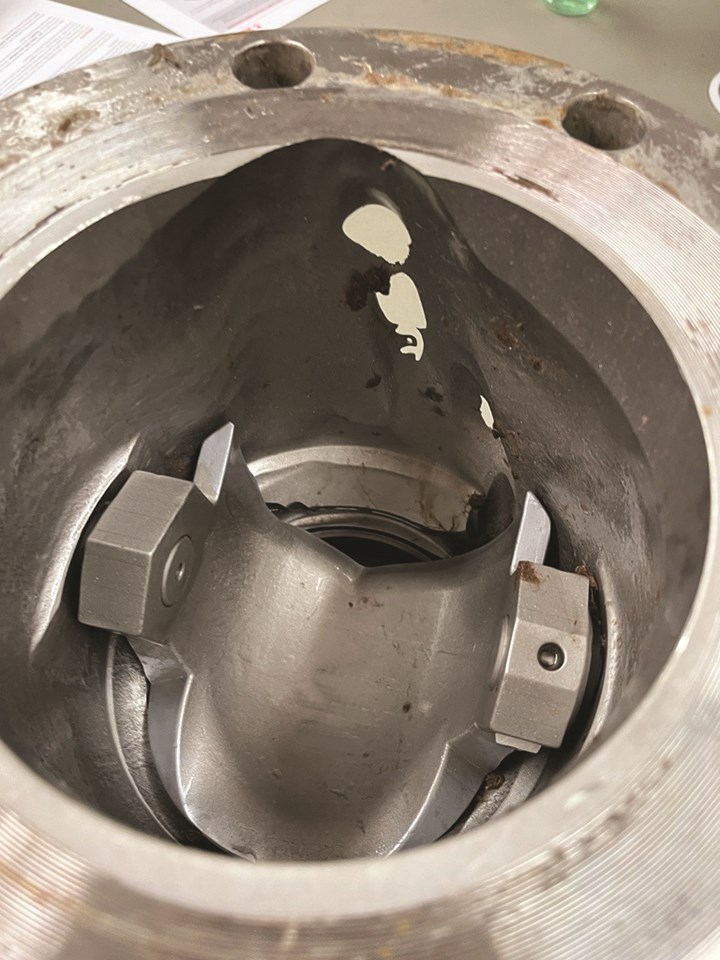
Internal photo of the same valve with holes highlighted, and erosion shown throughout on the ball of the valve.
There are solutions on the market that are more durable that may be used in some of these applications, including ceramic valves or chrome iron valves. It’s critical that the internals of the valve, including the entire fluid path and the ball or disk be made with these materials. These options are typically costly.
Ceramic valves can withstand a lot of abrasion but are more susceptible to cracking and failure from excess vibration, mechanical or hydraulic shock or pressure. They are better suited for processes where the fluids are highly abrasive, and slurries are thicker and heavier. They may be used in the harshest part of the stock preparation process but aren’t frequently used. Chrome iron internals are more durable than ceramic. In virgin paper manufacturing you are more likely to see these valves because of the caustic chemicals used in bleaching and processing the pulp. They may also use valves made of alloys or exotics such as Hastelloy, Titanium or Monel.
Iqbal said one successful deployment he’s seen for control valves on rejects in recycled paper plants is the use of standard stainless steel valve bodies with abrasion-resistant thermally coated internals and specialty alloy seats and downstream bore liners. For example, when using a ball valve, he recommends the entire bore of the valve be coated with the abrasion-resistant coating including the ball. This is also a more cost-effective solution for a market with very tight operating budgets.
The valves at the bottom of the cyclones are typically knife gate valves. He’s seen these fail very commonly. One reason can be that the cyclonic action can be enough to bore through the gate of the valve. He’s also seen many of these valves leak through the packing and the seats because of improper materials selection. Jamming is a common failure as the rejects/junk from the media builds up in the pockets leading to valves getting stuck. Bray offers a knife gate valve that has a proprietary coated vortex breaker in it to break the cyclonic effect to prevent the rejects from creating a drill-through problem. They also use harder materials for the gate to allow for more strength and abrasion resistance. In addition, the Bray valve has a copper scraper to prevent damage to the packing. The purge ports allow the customers to use high-pressure water and flush the rejects/junks from the valve preventing jamming.
Proper Sizing and Actuation
With these valves often cycling up to 1500 times a day, users need to consider not just the valve but the durability of the actuators. With dust and debris inherent to the atmosphere of a pulp and paper plant, seals can fail in fluid-powered actuators because they are made from soft materials and the actuators develop leaks, leading to pressure blowby. “As you’re trying to build up pressure in the actuator to move the valve, your seal integrity has been compromised due to foreign particles inside the actuator housing and the actuator is not able to move the valve,” said Iqbal. “One thing to keep in mind is the importance of the type of actuator seal selected. Most actuators have O-rings, but we use Quad rings as standard for better seal integrity and reliability.” Bray's standard design also has internal wipers for actuators that remove dust and debris that may have been ingested in the actuator assembly. Bray also offers a closed-loop pneumatic circuit that prevents ingesting outside dust and debris — enhancing the life of the actuator.
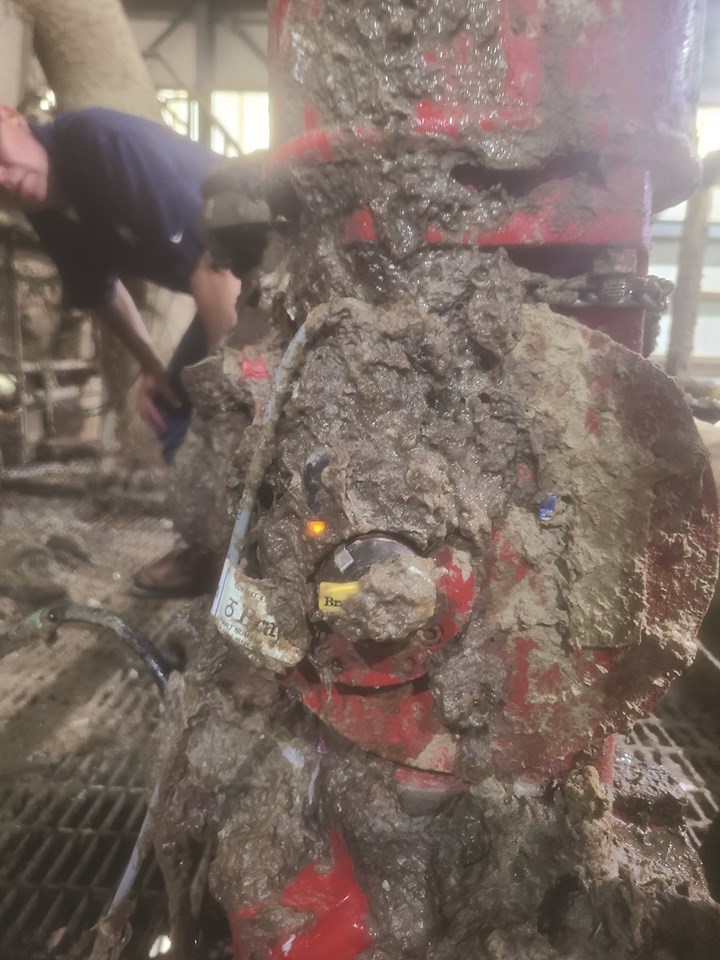
Actuator covered in pulp in application.
Iqbal also recommends the use chrome plating on the inside of the actuators. “Chrome plating allows multiple benefits. There is also a lot of moisture in the air and sometimes instrument air can have moisture as well at these plants, so having chrome-plated internals helps with corrosion resistance.
Utilizing appropriate safety factors for actuator sizing is critical as mentioned by Iqbal and his team so that the actuator has enough torque or thrust to account for the buildup of pulp, debris and scale from the media and the ability to handle the high cycles often found in paper plants.
Valve sizing is another area where users should work with their suppliers closely. When customers say they are having repeated failures, computational fluid dynamics (CFD) can be used to analyze the processes and make recommendations. Using process flow conditions, angles of opening and other relevant details, they can then recommend the best solutions.
“We use ISA control valve sizing standards with the CFD analysis and recommend sizing, sometimes upsizing, sometimes downsizing, to help them last longer. We see valves being undersized or oversized all the time, usually oversized, which leads to premature wear and failure,” he said. “Failures happen most where you have constrictions, such as valves or other components to restrict flow. Proper valve sizing helps reduce the constriction for flow upstream and downstream, eliminating high velocities and preventing premature failure.”
Another consideration is the ease of repairability and replacement for the maintenance teams. “All of these valves are eventually going to wear out – there’s no bulletproof solution,” Iqbal said. “So, giving customers a valve solution that is repairable and can be easily fixed versus replaced.”
Manufacturers have embraced videos to train their customers on how to repair and replace their own valves. They post them on YouTube or other easily accessible sites so that the maintenance team isn’t flipping through a 60-page manual but watching a short step-by-step repair video. “We need to make it easier for those in the field to understand what the problems are, diagnose and repair them. If you can do that in a five- or six-minute video, it’s a great solution,” Iqbal said.
Most suppliers also offer training to their customers. Bray offers different options for employees in different roles and can do the training at one of their facilities or on-site at the plant. Training includes valve sizing and selection geared toward plant engineers, as well as a focus for instrumentation and reliability techs and maintenance geared toward diagnosing and repairing issues as they occur. Reach out to your supplier directly for information on the training offered.
Final recommendations
At the end of the day, valve companies want to do all they can to help their customers control their total cost of ownership. If you work at a plant, involving your suppliers early and often can help your operations be more efficient and avoid unnecessary costs, wasted pulp due to leaking valves or unplanned shutdowns. Iqbal recommends engaging directly with valve companies that have the technical and application depth when possible to allow for a strong technical partnership between the teams resulting in maximized productivity and efficiency for the plants.
Heather Gaynor is the editor of VALVE Magazine.
SIDEBAR
RELATED CONTENT
-
New API Standard for Globe Valves
While the American Petroleum Institute (API) and other organizations published a variety of valve standards covering gate, ball, check, butterfly and plug valves for decades, the first for globe valves came out in 2013.
-
Ball Valve Repair 101
From time to time, we are re-posting well-received or particularly valuable articles that have previously run on VALVEMagazine.com so that those who might have missed them will be able to catch up on the best of the best.
-
The Biggest Valves: Sizes Growing in Step with Greater Demand
Valve manufacturers that have the expertise, skills, equipment and facilities to produce large valves are rare.