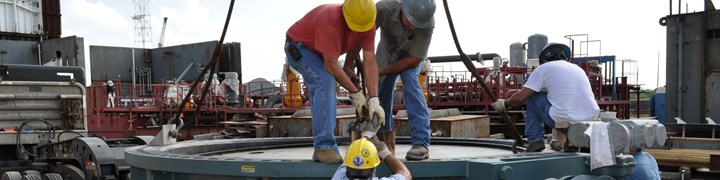
In a time of ever-increasing demand for industrial growth and end products, sectors such as refining, water and wastewater, hydropower, chemical and mining are seeing a move toward bigger valves. But with greater size, many factors and design considerations come into play, as it’s not a simple proposition of enlarging the valve components. Very few companies in the world are capable of manufacturing such large valves. Below are three VMA member companies — DeZURIK, ITT Engineered Valves and Mueller Water Products — that fielded questions about this change and the complex engineering, unique challenges and great lengths to which they’ve gone to meet design, manufacturing and logistical needs all along the way. Also included are the three manufacturers’ case studies citing specifics of their work.
DEZURIK
by Don Bartell and George Stevenson
DeZURIK has a long history of manufacturing large valves. For DeZURIK, a large valve is considered 42 inches and greater. The company manufactures cast eccentric plug valves to 72 inches, resilient seated butterfly valves to 168 inches and knife gate valves to 48 inches. At the manufacturing plant in Redmond, WA, DeZURIK specializes in engineering and fabricating large diameter and custom valves up to 144 inches. Fabricated construction allows the use of high alloys for wetted parts and less costly materials for exterior construction. For the hydro market, DeZURIK has supplied custom fabricated fixed cone and jet flow gate valves in sizes up to 78 inches and throttling knife gate valves up to 96 inches for releasing water from the low-level outlets of reservoirs.
Why is there a trend toward producing bigger valves?
- Population shifts to more arid climates require water to be transported from the source through larger and longer pipelines than ever before.
- Limitations on groundwater pumping enacted to maintain healthy aquifers and prevent seawater encroachment necessitates transporting water from surface water sources through large pipelines over long distances.
- Aging infrastructure and increasing urbanization where larger water treatment and wastewater/sewage treatment facilities are being specified, which requires larger valves.
- Climate change and increased extreme weather events, such as hurricanes, flooding and levee breaches that require larger storm water-handling valves. The hydro sector, for example, is impacted by climate change and more frequent large rainfall events. Dam owners are under pressure by regulators to increase the ability to release water faster to avoid flooding or overtopping, which often translates to a need for larger valves. A lesser factor is the regulatory requirement to release more flow from low-level outlets to improve downstream conditions for fish and recreation. Many existing low-level outlet valves are incapable of releasing greater mandated flows. Also, drought conditions are increasing the need for longer pipelines and more storage.
- Accessibility is a growing challenge. On one of our projects, the tortuous route for the pipeline was determined by the public not wanting a pipeline under its homes, so it was run under roadways instead. A bigger pipeline under the roadway of this heavily populated area was more acceptable to the public.
- Increases in power consumption require valves for hydropower facilities and oil and natural gas pipelines.
What are the most significant challenges in dealing with exceptionally large valves?
There are simply fewer companies that have the design expertise and manufacturing capability available to handle big valves. There are also fewer foundries that can pour the large castings. Engineering capability and complex tooling may need to be created. Valve manufacturers that have the expertise, equipment and facilities to produce large valves are rare. The manufacturing process may be less vertically integrated — handling, testing and transporting larger valves is more challenging.
Other noteworthy large-valve challenges include:
- Material handling for fabrication and testing (factory crane capacity and lift height limitations) is a challenge. Another issue is machine tool limitations (the mill and lathe size required).
- Compliance with industry standards that apply to smaller valves can often be cost-prohibitive to meet on a larger valve.
- Stroke speed (speed that the gate or flow element moves) for large electrically actuated valves may need to be faster than that for a smaller valve so as not to exceed standard 15- or 30-minute electric actuator motor run times.
- Standard semi-trailer over-road maximum capacity is 80,000 pounds. At the site, the contractor may also have handling limitations or the access to the installed location may be restricted, requiring the valve be shipped in pieces and assembled onsite.
Are your largest valves all “one off” or custom-made?
The first time a large valve is built, it is a custom build, but as requirements for larger valves increase, so does the likelihood that the valve build will be repeated until it is no longer a special. All large Hilton valves are custom fabricated or “one off.” The advantage of this is that the valve can be designed to meet specific pressure regimes. Most cast valves have a minimum pressure rating of 150 psi; if only 50 psi is required, a 50 psi fabricated valve can be supplied. This greatly reduces the weight and cost of the valve.
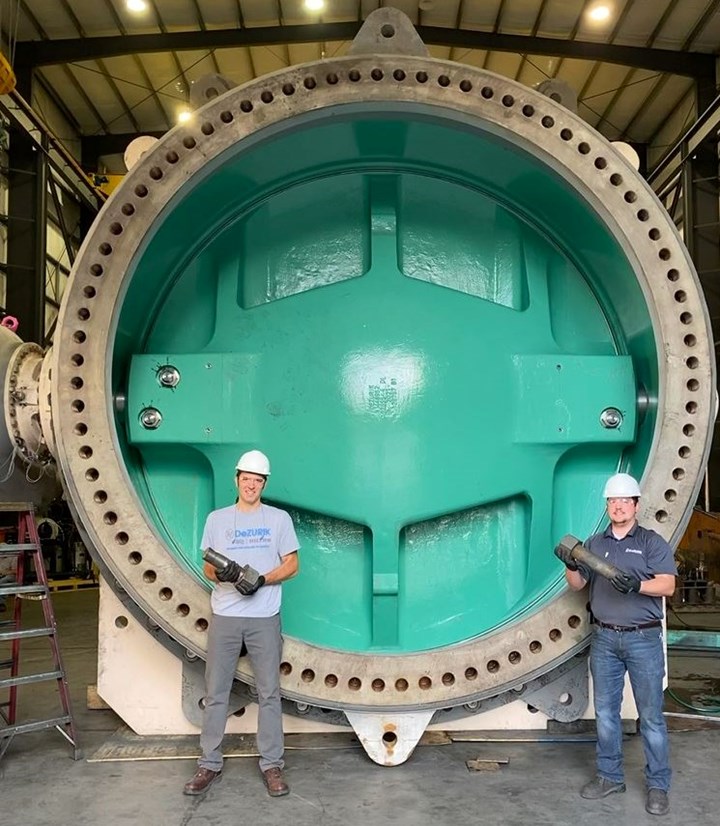
Figure 1. 168-inch AWWA butterfly valve. Photo credit: DeZURIK
DEZURIK CASE STUDY: A BUTTERFLY VALVE FOR WASTEWATER TREATMENT
This 168-inch (14-foot internal diameter) AWWA butterfly valve (Figures 1, 2), manufactured by DeZURIK in 2021, will be installed as part of a wastewater treatment plant in one of the Los Angeles County Sanitation Districts. The valve will control the flow of treated water from the plant through a seven-mile-long, 18-foot-diameter tunnel to the outfall. This project, approved in 2012 after a multiple-year evaluation, is a preemptive solution to an aging sewer infrastructure and a growing population. The existing two tunnels were built in 1937 and 1958 and a failure in either tunnel or overflow conditions would require drastic measures to ensure continued water treatment service and prevent flooding to the area. The most concerning was the possibility of accidentally dumping untreated sewage and contaminating local waterways that lead to the harbor and surrounding beaches.
This 168-inch outfall valve is the largest ever built in the United States. It weighs about 70 tons and is roughly 21 feet wide (including the actuator) and 17 feet tall. The body is 43 inches from flange to flange and has integrally cast lifting lugs and support bases. Engineers also designed a new flange bolt pattern since there is no AWWA specification for valves this size. Extensive valve testing and validation were requirements for this project. Pressure rating and testing is 50 psi. The valve is tested to meet requirements of the AWWA 516-21 standard. Stress calculations were performed on all torque-bearing components validating design prior to building. A requirement for ultrasonic testing of castings was also completed.
DEZURIK CASE STUDY: A KNIFE GATE VALVE FOR NASA
Figure 3. Sketch of the 66-inch Hilton bonneted knife gate valve at the NASA John C. Stennis Space Center rocket test facility.
Photo credit: DeZURIK
A 66-inch Hilton bonneted knife gate valve (Figures 3, 4) is installed at the John C. Stennis Space Center NASA rocket test facility in Mississippi that oversees the safe operation of rocket engine propulsion test programs. During testing of rocket engines, temperatures on the test stand are high enough to melt the steel and destroy the concrete structure of the stand. Therefore, during testing, the test stand is flooded with water to lower the temperature on the stand. A 66-inch pipeline feeds water to the A-1 test stand that is capable of static firing a test article up to 33 feet in diameter. The A-1 test stand was used most recently to test the Space Launch System RS-25 rocket engine.
Figure 4. Hilton bonneted 66-inch knife gate valve at the NASA John C. Stennis Space Center rocket test facility.
Photo credit: DeZURIK
The cooling water isolation valve is only required to open at 25 psi maximum pressure differential and there is normally no pressure for the valve to open or close against. The pipeline is designed to handle a pressure of 275 psi, therefore the valve body is designed for the full pressure rating of 275 psi with a test pressure of 413 psi.
DEZURIK CASE STUDY: HILTON JET FLOW GATE VALVES IN TAIWAN
Figure 5. Hilton Jet Flow gate valve in Taiwan. Photo credit: DeZURIK
DeZURIK manufactured two 78-inch orifice diameter Hilton Jet Flow gate valves (Figures 5, 6) that were installed at the Tseng Wen Reservoir on Southern Taiwan’s Zengwun River. This dam is part of Taiwan’s largest reservoir by volume (approx. 480,000 acre-feet) and supports the local irrigation and flood control, in addition to a 50MW hydroelectric power station. The Jet Flow gates are installed below the 420-foot dam, which is the third-tallest in Taiwan. The reservoir is located in a remote area in South-Central Taiwan and the valve chamber is inside a mountain, with a long tunnel as the only access. The valves are used for throttling service and are submerged in water and encased in concrete.
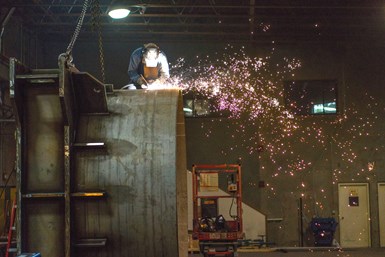
Figure 6. Welding the jet flow gate valve. Photo credit: DeZURIK
These gate valves measure 31 feet tall and 10 feet wide and weigh 75,000 pounds. The only way to transport the valves to the installation site was to ship them disassembled. After final testing in DeZURIK’s Redmond, WA factory in September 2013 (witnessed by representatives from the Taiwan government and the contractor) the valves were disassembled and loaded on flat racks for ocean shipping. The DeZURIK engineering team flew to Taiwan job site in 2014 to observe and advise on the off-loading, transport, installation and preliminary testing of the valves.
DEZURIK CASE STUDY: AWWA POST-KATRINA BUTTERFLY VALVES
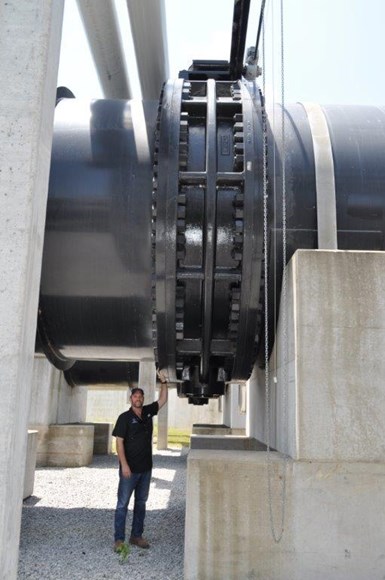
Figure 7. DeZURIK 144-inch AWWA butterfly valve in Belle Chasse, LA. Photo credit: DeZURIK
DeZURIK 144-inch AWWA butterfly valves (Figure 7) were installed in 2010 as part of the New Orleans post-Katrina hurricane risk-reduction program at the levee in Belle Chasse, LA. These valves are one important component of the levees that held up during hurricane Ida in fall 2021.
DEZURIK CASE STUDY: APCO SWING CHECK VALVES
Sixty-inch APCO brand CVS-6000 swing check valves (Figure 8) and ASV air vacuum valves are installed at the Louis Armstrong New Orleans Airport Pump Station. The pump station was part of a project to $1.029 billion project to construct a new terminal to replace the original and
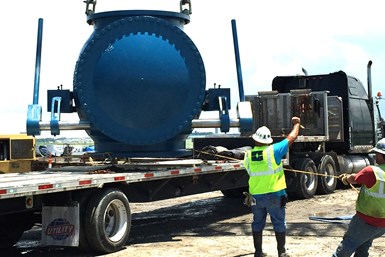
Figure 8. DeZURIK 60-inch APCO check valve for the New Orleans airport. Photo credit: DeZURIK
outdated 60-year old terminal. The project began in 2013 and opened in 2019. This pump station directs stormwater away from the airport to protect against flooding damage during tropical storms. The valves are part of the extensive post-Katrina infrastructure modifications that are critical to the protection of the City of New Orleans and its transportation system.
ITT ENGINEERED VALVES
by Jeremy Carroll
ITT Engineered Valves has 70 years of experience creating large custom valves for a variety of applications to ensure all of these considerations are made prior to manufacturing.
Why is there a trend toward producing bigger valves?
ITT has certainly seen an increase in both the creation of, and demand for, larger diameter valves. This trend is driven in large part by three unique factors.
First, the capabilities of ITT’s customers are growing, especially regarding their pumping operations. As pumps grow, they’re able to push much more material through a valve, requiring a larger diameter. For example, while two 30-inch valves seem to equal the same capacity as one 60-inch valve, a larger diameter valve can fit much more material. It would likely take two 48-inch valves to equal the same capacity as one 60-inch valve, which is a much more efficient way to work.
Second, many municipalities are investing in large valves for processing water/wastewater to keep up with growing populations. For instance, while the population of a city like Boston continues to grow, the actual physical size of the city stays the same. Instead of growing horizontally, municipalities are investing in equipment that can process sewage much faster to keep up with demand.
Finally, events like the recent flood in Houston have forced many municipalities to rethink their maximum capacity. Water/wastewater systems must be designed to handle maximum capacity, which is often in the early evening when commuters arrive home from work. Some municipalities are beginning to dig deep tunnels to act as reservoirs for wastewater — during peak time, water is diverted to that tunnel through large-diameter valves and is later returned back to the processing plant during the middle of the night.
What are the most significant challenges in dealing with exceptionally large valves?
As the size of the valve increases, handling the valve becomes more difficult. This includes longer testing times, ability to maneuver and the cost of shipping. For the customer, installation becomes more difficult as the valve becomes harder to move and rigging must be more precise.
A major consideration for large valve manufacturers is the maximum psi the valve can handle. For example, users of 2- to 24-inch sizes often send roughly 60-90 psi through their valves, which are usually designed to handle up to 150 psi. No problem there. But when looking at a 72-inch valve, which is designed to handle around 25 psi, it’s much easier for the actual psi to rise above that threshold. When psi rises above the amount a valve has been designed to handle, a series of issues can occur, including the inability to open and close the valve, damage to internal components and more.
Are your largest valves all “one off” or custom-made?
In ITT’s experience, roughly 90% of all large valves — which are defined as anything over 42 inches — are custom-made. When designing something so large, each attribute of the valve costs more and every application requires unique characteristics. For these reasons, designing large valves to sit in inventory would be impractical.
ITT CASE STUDY: FISH DIVERSION VALVE FOR HYDRO-ELECTRIC DAM
F134, 132 inches, 50 psi, 104,825 pounds, 42 feet tall (including actuator) 16 feet wide and 6 feet deep, installed in 2016 — this fish diversion valve is for a hydro-electric dam in Asia (Figures 9, 10). The local population’s primary industry was fish, and the dam created concerns related to the welfare of the fish midway through the project. ITT had to work quickly with the engineering firm to develop a fish bypass around the dam turbines, which decreased damage to the river’s fish population, allowing the project to move forward without further delay.
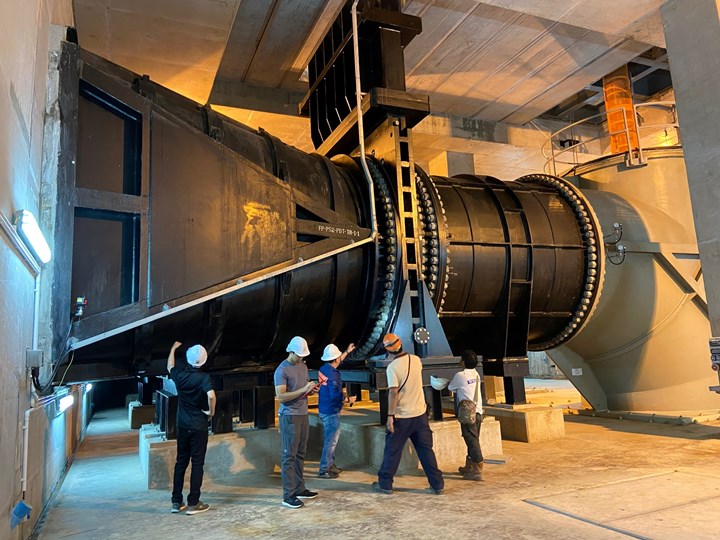
Figure 9. 132-inch fish diversion valve. Photo credit: ITT Engineered Valves
Unlike other valve designs, the knife gate design allowed for unrestricted flow through the bypass system. However, with no standards for knife gate valves of this size and with high-pressure requirements, ITT engineers had to rely on years of experience and finite element analysis to create a product that would not affect the safety and livelihood of the surrounding communities.

Figure 10. A different view of the 132-inch ITT knife gate valve. Photo credit: ITT Engineered Valves
One interesting challenge in this project is that the 132-inch valve was too large to ship as a unit, so it had to be designed as an erector set and shipped in pieces to be assembled in the field (with limited valve knowledge onsite). To overcome this challenge, ITT designed the product so it would assemble and seal in the field without the need for extensive know-how.
ITT CASE STUDY: KNIFE GATE VALVE FOR VICTAULIC COUPLINGS
F134, 84 inches, 50 psi, 24,000 pounds, 26 feet tall (including actuator) 8.5 feet wide and 5 feet from flange to flange, installed the first in 2004 and another in 2020 — this large knife gate valve is in Michigan where the customer needed a Victaulic pipe connection (Figure 11). Victaulic couplings are typically reserved for small-diameter valves and are not very common with knife gate valves, especially in this diameter. ITT was able to accommodate the customer’s needs, meeting the required face-to-face dimensions and reducing the amount of time needed to tighten the flange bolts.

Figure 11. 84-inch knife gate valve. Photo credit: ITT Engineered Valves
In addition to the odd connecting flanges, the valves needed to fit into an existing vault with height restrictions. To do so, ITT partnered with a hydraulic operator company to supply a self-contained hydraulic power unit that could be integrated into the hydraulic cylinder. The operator-to-valve connection featured a close coupled design that eliminated the need for a yoke, allowing for a height reduction of over six feet. This design required precision machining of the valve bonnet in order to guarantee smooth assembly and actuation. In addition to the two installed Victaulic valves, three additional valves are planned for the future.
MUELLER WATER PRODUCTS
by Timothy Fallon and Julian Ramirez
Mueller Water Products is a manufacturer and marketer of products and services used in the transmission, distribution and measurement of water. For more than 160 years, Mueller has manufactured a variety of valves, including large custom-engineered valves. The company’s broad product and service portfolio also includes fire hydrants, pipe connection and repair products, metering products, leak detection, pipe condition assessment and pressure management products.
Why is there a trend toward producing bigger valves?
The frequency and severity of drought in the West and severe weather events, like slow-moving hurricanes in the gulf and on the East Coast, have motivated municipalities to creatively figure out how to collect, protect and conserve available raw and semi-finished freshwater resources. The large population migration to non-drought areas and the numerous water conservation projects in drought-ridden regions are fueling some very large projects, such as protectively “banking” water that has already been treated in new facilities. There are also big projects underway to prevent raw water reservoirs from overflowing to the south. To do this, new or larger pumping stations are being built to pump (transfer) water over to neighboring northern reservoirs to minimize losing what has already been naturally collected. Moving larger amounts of water requires bigger valves.
What are the most significant challenges in dealing with exceptionally large valves?
One of the biggest challenges is costing and pricing. Due to the seldom-sourced large-diameter product, the ability to accurately estimate the cost to produce these sizes is a big risk for manufacturers — the work is often too large to machine in-house, so the outsourced production becomes an unknown cost variable, which is a gray area in getting a fixed or capped cost. The same goes for the raw materials. These projects are sometimes years out, so the cost per pound of carbon steel and stainless alloys can swing in the wrong direction over the course of the project. Also, any ancillary (one-time) equipment costs need to be taken into consideration, such as testing equipment (test heads with bolts and nuts). The costs are high and the lead time alone to obtain a pair of large-diameter test heads can be up to 18 months. Another challenge is that when you are dealing with large castings you have more room for casting issues, like porosity. Also handling and testing becomes more complicated as valves get larger.
Are your largest valves all “one off” or custom-made?
Yes. Anything that is not covered by a nationally recognized standard (or designed to the intent of a standard) is considered a custom product. For both butterfly and plug valves, we have large standard castings, but we have also fabricated large butterfly valves.
MUELLER CASE STUDY: VALVE AND ACTUATOR UPDATES FOR AGING RECLAMATION PLANT
The Hyperion Water Reclamation Plant is the largest sewage treatment facility in the Los Angeles metropolitan area, treating 450 million gallons per day. During a comprehensive inspection, Hyperion officials discovered deterioration of its primary outfall pipeline, which wasn’t unusual given that the pipeline and pump header were over 60 years old. The inspection also revealed that 10 old isolation butterfly valves on the suction and discharge sides of the vertical turbine effluent pumps needed to be refurbished or replaced due to corrosion of the valve body and disc. When tide and plant hydraulic conditions allow, plant effluent flows with the help of gravity through a 120-inch diameter butterfly valve (Figure 12) to the plant’s five-mile outfall pipeline without the use of pumps. Failure of any of these valves could create a backflow event, which would flood the plant.
Figure 12. R. Scott Scheffler of MOOG-Flo-Tork with new 120-inch butterfly valve.
Photo credit: Mueller Water Products
To repair the pipeline, maintenance and construction crews needed to divert the treated wastewater to an emergency one-mile outfall pipeline. The city’s environmental engineering division determined that Hyperion crews and suppliers would need to work around the clock for six weeks to minimize impact on plant operations and the environment.
While refurbishing valves can save money, it can often take longer than installing new products. Existing valves must be inspected to determine if refurbishment is a viable option, and given the location, these valves could not be extracted until the project had begun. This would delay the project’s timeline, as parts would need to be located and ordered when work should already be underway. The Los Angeles Department of Public Works had documented that the five existing 60-inch butterfly valves and the five 78-inch valves were Pratt valves installed in the early 1970s. Knowing this information meant original project files, parts and replacement valves could be on hand before starting the work.
However, there was one exception: the 120-inch gravity-fed butterfly valve was critical to public safety and plant operations. If this valve were to fail in the open position at high tide, ocean water from the bay and effluent would back up the pipe and potentially flood the facility. There was no secondary valve, but rather a redundant cylinder for closing and opening the valve. This butterfly valve was custom-made with no original manufacturer marking to be found. Given the time constraints, replacing it with a new butterfly valve was the only viable option. This also meant that a new actuation system would be required.
Moog Flo-Tork designed an actuator that required 3,200 cubic inches (13.9 gallons) of hydraulic oil per stroke with a rated working oil pressure of 3,000 psi. This system would produce up to three million inch pounds of torque from either one of the two rack-and-pinion actuators, which accommodated the need for redundancy. Even though the two actuators are mechanically sandwiched together, they act as independent primary and emergency backup actuation systems.
ABOUT THE AUTHORS
Don Bartell is currently vice president of Municipal Sales for DeZURIK. Don has over 30 years of experience in municipal valve applications and sales management. He received a bachelor of science degree in Engineering from Penn State in State College, PA.
George Stevenson officially retired from his position as chief engineer for DeZURIK’s Hilton Valve product line in 2019 after 44 years of service but is still involved in a few special projects. George graduated with a bachelor of science in Mechanical Engineering from California State Polytechnic University in Pomona, CA.
Jeremy Carroll has worked in the material and fluid handling industry for more than 15 years. He has had roles in engineering design, applications engineering, production management and new product development. Jeremy’s current role of knife gate valve product manager for ITT Engineered Valves has a wide-ranging scope and often leads to front line involvement in industries including water/wastewater, pulp and paper, power, mining and petrochemicals.
Timothy Fallon is senior product manager at Mueller Water Products. He has been in the valve industry for more than 20 years and has a strong technical understanding of valve engineering to ensure customers have the optimal flow control solution. Email him at tfallon@muellerwp.com.
Julian Ramirez is product manager at Mueller Water Products, overseeing the development of air valves, industrial butterfly valves and knife gate products. Email him at jramirez@muellerwp.com.
RELATED CONTENT
-
America Moves Toward a Stronger Infrastructure
Here’s what you need to now about the multi-billion-dollar funding designated for the water and wastewater markets as part of the American Jobs Plan.
-
Are Bypasses Needed With Today’s Waterworks Gate Valves? New Information Says They’re Not
Gate valves are the most common valve used in the water utility industry.
-
Automating Old Sluice Gates with Electric Actuators
Since the early days of water and wastewater treatment plants in the U.S., municipalities and industries have continued to expand and upgrade existing plants and distribution infrastructure as well as build new facilities.