Are Bypasses Needed With Today’s Waterworks Gate Valves? New Information Says They’re Not
Gate valves are the most common valve used in the water utility industry.
#water-wastewater #gate-globe-check
Gate valves are the most common valve used in the water utility industry. As with many utility-type valves developed in the 1800s, the gate valve continues to employ many of its original features. The Industrial Revolution helped solidify the iron-bodied and bronze-mounted (IBBM) gate valve as a workhorse for controlling flow in the modern-day utility system. An important part of the larger diameter valve offerings included the use of gear actuators and integral bypasses. Gear actuation was necessary for the reduction of input torque to operate these valves. Similarly, various bypass appurtenances were necessary for the equalization of pressure differentials across the valve. Over time these metal-seated valves would give way to a much simpler design, called the resilient wedge gate valve (RWGV), which eliminated many of the operational hurdles caused by the different pressures.
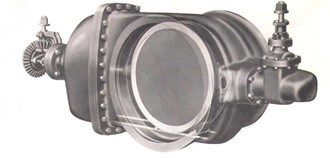
Figure 1. Iron-bodied and bronze-mounted (IBBM) gate valve with integral bypass. All photos courtesy of: AMERICAN Flow Control
Although the use of gear actuators in larger valves are beneficial, resilient wedge gate valves, introduced domestically more than 40 years ago, inherently require a much lower operating torque. For this reason, the operational need for the use of bypasses has long been questioned. In fact, today, most municipalities consider the bypass to be an added component to the system that must be maintained and accounted for, and the engineering community rarely requires bypasses. This position is based on logic and inherent field experience, but until recently, there was no empirical data to support the position that bypasses, for the routine operation of resilient wedge gate valves, are not needed.
BYPASSES DO NOT TYPICALLY LOWER THE OPERATING TORQUE OF RESILIENT WEDGE GATE VALVES
To determine the effects bypasses might have on large diameter resilient-seated gate valve operation, AMERICAN Flow Control conducted a series of operational tests on an AFC Series 2500 30-inch resilient wedge gate valve, equipped with a 2-inch bypass assembly, as shown in Figure 2. The initial flow rate in the pipe was recorded at 5,800 GPM. For this test, the 30-inch gate valve was cycled from a full-open position to a fully closed position under initial 80 psig line pressure. Operational torques were recorded six times through an automated cycle tester. Three of the recordings were collected with the bypass closed, and three recordings with the bypass open. To ensure accuracy, the valve automated cycle tester was mounted directly to the valve, eliminating the need for a manual gear actuator. The results of the tests are presented in Figure 3.
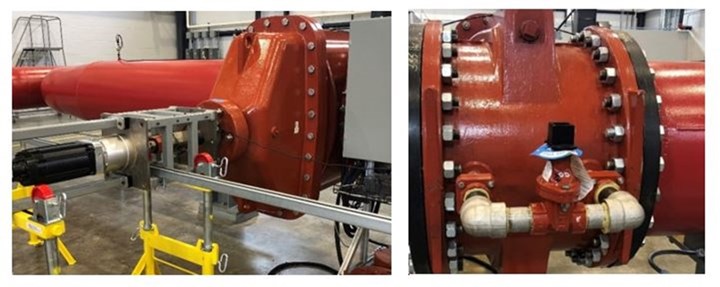
Figure 2. Operational torque testing setup for bypasses.
In all accounts, maximum torque values were recorded within two to three turns while opening the valve from being fully closed. As detailed, the maximum torque values were the same, regardless of the use of the 2-inch bypass. The remaining torque values leveled off at a significantly lower value for the remainder of the valve operation cycle. The initial torque values reflect the initial cracking torque of the valve. This increase in torque is necessary to overcome the compression seal that exists between the rubber encapsulated wedge and the valve body. In summary, the difference in the average maximum torque between open and closed bypass tests differed by only 2 ft-lbs, or about 1% of the 660 ± ft-lbs of torque required to operate the non-geared valve. This information validates the long-held assumption that bypasses are not required, but more importantly, it also validates the reason they are rarely used in practice.
OTHER CONSIDERATIONS
Although reduction in operating torque has long been the primary reason for using bypasses, in rare cases a bypass is used by system operators to fill new lines, or recently evacuated lines, downstream from the mainline valve. This practice was primarily used with metal-seated valves, which were prone to seat damage when the gate was left in a near-closed position for long periods of time. In that situation, damage could occur to the soft, unforgiving copper alloy seats because of high fluid velocity and the potential of trapping debris. This damage is characterized as wire drawing, which is an erosion or scoring of the seat. Although the throttling of a gate valve has never been recommended, the occasional use of partially opened resilient wedge gate valves, with full rubber encapsulation, has become an accepted operational field practice. System-type bypasses incorporated into the pipe network and independent of the valve are considered the best design practice.
Figure 3. Empirical test data demonstrating the lack of need for bypasses on a resilient wedge gate valve.
In cases where bypasses are used, some might assume larger bypass sizes can help prevent damage to the valve because a smaller bypass valve will have higher fluid velocities. This is incorrect. Innate to their design, RWGVs have functionally negligible resistance coefficients. Because of this, basic precepts of fluid mechanics state the velocity in the bypass will remain relatively constant, while the flow rate changes with the cross-section of the bypass. The results can be demonstrated by using modeling software, such as shown in Figure 4. In this illustration, a graphical comparison is made showing the functional difference between a 2-inch and 4-inch bypass with color representing velocity. Note bypass fluid velocities are the same.
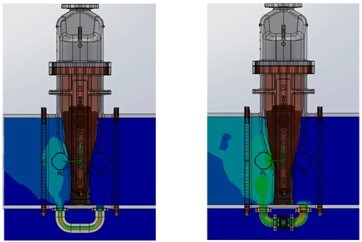
Figure 4. Comparison of bypass velocities as illustrated by flow simulation software.
SUMMARY
As creatures of habit, we must be reminded we shouldn’t do something just because it’s what we have always done. Design improvements and material changes have exponentially improved the gate valves used in today’s utility system over gate valves used more than 40 years ago. Today’s valves are more simplistic in design and efficient in their operation, making bypasses a convention of the past. Utilities still using bypasses simply because they always have, should reconsider.
ABOUT THE AUTHORS
Derek B. Scott is marketing and technical manager for AMERICAN Flow Control. He holds a Bachelor of Science in Mechanical Engineering and has nearly 40 years of experience in the water and wastewater industries. Scott joined AMERICAN in 1988 and is currently responsible for the division’s technical and marketing functions. He has published several articles and represents the company on several standards committees, including AWWA, MSS, ASCE and NSF. He also has served on numerous stakeholder and advisory boards. He currently serves as chair of the ANSI/AWWA C515 Committee on Reduced-Wall, Resilient-Seated Gate Valves for Water Supply Service.
John R. Helf, PE is product engineer for AMERICAN Flow Control. He holds a Bachelor of Science in Mechanical Engineering from Mississippi State University and is a licensed Professional Engineer in the State of Alabama. Prior to working with AMERICAN Flow Control, Helf was project manager for AMERICAN SpiralWeld Pipe, a leading producer of large diameter municipal water and wastewater transmission piping. He is actively involved in AWWA and MSS standards committees.
RELATED CONTENT
-
Which Gate Valve is Best for Today's Waterworks Systems?
A historical perspective may provide the answer.
-
Testing of Hydrogen Valves
Valves are used to control all types of fluids, and while some are easy to manage, others can be a challenge. At the top of the challenging list sits hydrogen, the smallest, lightest molecule known to man.
-
New Requirements for Actuator Sizing
After decades of confusion, the American Water Works Association has created new standards for actuator sizing that clear up some of the confusion and also provide guidance on where safety factors need to be applied.