Five Reasons Why the Right Strategy Leads to the Success of Digital Transformation Implementation
The past few years have proven that digital transformation (DT) is more than just a trend. It is becoming one of the frontrunners for ensuring business continuity through modernizing times. However, despite being an essential component for adaptability in a competitive industry, not all companies would consider their DT implementation a success.
#iiot #automation #basics
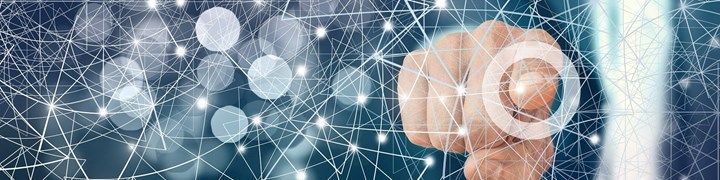
Most companies expect the benefits of digital transformation in manufacturing include reduced costs, data visibility and improved reliability, among other things. In other words, success means positive returns, higher efficiencies and increased throughput. Because DT usually relies on incremental changes, the overall success of implementation relies on staying true to a sound strategy.
BUSINESS TRANSFORMATION
Before diving into the details of digitalization, it helps to take a few steps back and understand why it is essential in the first place. Ultimately, DT is a business decision that needs to align with the company’s overall objectives. It is easy to get lost in the world of digitalization, high-tech tools and automated processes, only to end up with a poor bottom line.

The statistics shown here and in the following graphic are from L2L’s Digital Transformation Survey, conducted in January 2022. Respondents included 125 manufacturing leaders with mid to C-level titles across Production, Operations, Engineering, IT and Management. Photo credit: courtesy of L2L
For instance, a game-changing type of technology in the arsenal of digital tools is artificial intelligence (AI). A machine that can learn on its own, using massive amounts of data, can grab the attention of any manufacturer. But what does that kind of power really mean for a business?
For starters, wielding such technology can streamline the whole supply chain. Anticipating customer demand no longer relies solely on extrapolated historical information. Instead, a more thoughtful process can utilize algorithms to offer a more predictive outlook to forecast requirements. A valve manufacturer, for example, can link their inventory systems with their customers in the industry. With both sides having visibility on supply and potential constraints, modern systems can precisely identify when to order a new part.
The supply chain is only one of many practical applications of going digital, and there continues to be an abundance of emerging technologies. The challenge for companies is to discern which prospects make the most sense for their business and which ones align with their objectives.
DIGITAL JOURNEY
While some DT initiatives can realize value quickly, remember that an entire transformation is a continuous process. It is beneficial to think of DT as a journey that keeps on building upon a series of steps. Therefore, any progress towards digitalization needs to align with a clear vision and a well-founded strategy.
Going through DT is a balancing act of taking significant but practical actions. Taking on things all at once will set teams up for failure, while taking too much time runs the risk of being outpaced by competitors. Putting focus on particular projects over others should be guided by the current capacity of a company. Teams should also have the ability to adapt whenever results are no longer aligning with the overall objective.
The foundations of a strategy involve three key components: products, infrastructure and people. The constant flow of quality products is arguably the most significant — yet practical — challenge to displaying success. A digital transformation strategy needs to consider the continuity of operations and, consequently, the flow of products. Infrastructure refers to the resources a company needs to get to its goal. Preparing for any compatibility issues between transitioning technologies ensures minimal disruptions. Lastly, the people within the organization are the driving force behind the execution throughout the entire journey.
Remember that the actual state of implementation does not always follow a clear and exact path. Instead, you can expect an iteration of the different possible outcomes concerning transformation. A comprehensive strategy allows teams to stay true to the course regardless of the twists and turns along the way.
PROMOTING A DATA-DRIVEN CULTURE
Acknowledging the evolutionary nature of a DT journey highlights the importance of relying on objective decisions. Expanding on that same analogy, think of data as your compass while navigating through varying terrain. Of course, it is not enough to merely collect and gather data. Equally important is the way teams regard the information and utilize the knowledge.
There are several ways that a data-driven approach can manifest throughout DT. Prioritization of initiatives, for instance, needs to be based on reliable information. Any project that requires new tools and additional resources will incur costs. Companies need to ensure the advantages of taking on a project outweigh the costs within an acceptable timeframe to realize value. Modern systems such as Enterprise Asset Management software or Enterprise Resource Planning programs can tremendously lessen the effort in gathering such data. By having a sense of the current allocation of resources going into existing processes, any improvements can be more readily determined and quantified.
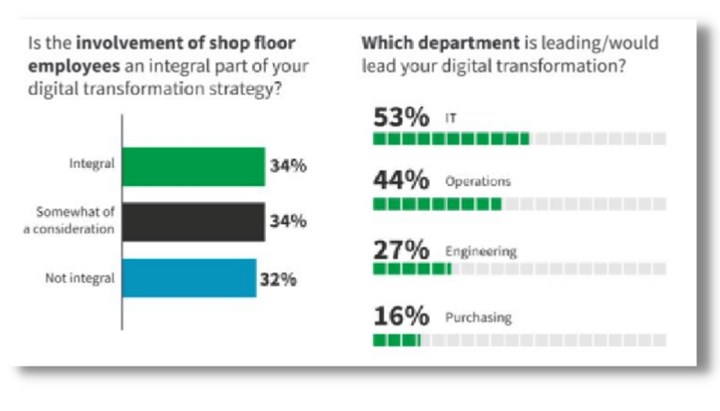
Regardless of how the data lends itself to various aspects of the transformation, companies should recognize the importance of building a data-informed culture. Involving workers from different levels of the organization promotes an environment of awareness about the possibilities and boundaries of data.
MAXIMIZING ASSETS
While the measure of success can vary for each company, we can all agree that there is significant value in maximizing the potential of current and future assets.
For equipment used in manufacturing, maximizing assets may relate to maintenance and operations to increase reliability and throughput. A traditional approach might employ a preventive maintenance strategy that schedules servicing tasks, preempting breakdowns. A modern approach to the same problem can more precisely identify maintenance needs using software that leverages big data.
Advanced maintenance methods may call for specialized tools and processes. For example, an industrial valve will require several additional sensors, measuring devices and transmitters to gather and collect sufficient information. Additionally, a computing system will need to consolidate the data and perform analysis using a comprehensive algorithm. All these components play a role in the DT journey as the digital maturity of a facility will prescribe the viability of more advanced maintenance strategies.
Infrastructure spending to prepare manufacturing systems for advanced options can comprise a sizable portion of the budget. Decisions about the resources to put into projects come back to comparing investments with the perceived benefits. A practical approach for companies is to identify the critical materials that will realize returns on manufacturing process improvements and specialized maintenance strategies.
PEOPLE MANAGEMENT
As with any business transformation, DT does not just impact physical and virtual tools — but also the users themselves. Planning for the various skill levels throughout the phases of a DT journey requires a dynamic approach to people management. Examples of questions to think about include what support the company needs, what opportunities are there to upskill employees, and what feedback the workers have with any project development.
A common concern for employees is that highly technological tools are often an entirely different scope of work from their usual expertise. A good strategy will be to narrow the gap between the technical requirements of digitalization and the skills of the intended users. Opportunities for training and upskilling will be beneficial to increasing the number of resources that can add value to the transformation. In parallel, management teams should consider selecting user-friendly software alternatives whenever possible.
Preparing for a diverse group of users ensures that the leap to digitalization need not be a shocking event. Instead, it becomes a learning experience that builds on collective knowledge and shared experience.
CONCLUSION
Transitioning to a more digital world is an inevitable feat in establishing an agile and competitive manufacturing practice. Once a company embarks on its digital journey, the process becomes a continual effort to innovate and improve. Throughout the transformation, a long-term strategy needs to be in place to guide actions toward success.
ABOUT THE AUTHOR
For more than 30 years, Eric Whitley has been a noteworthy leader in the manufacturing space. In addition to the many publications and articles he has written on various manufacturing topics, he led the Total Productive Maintenance effort at Autoliv ASP and has been involved in the Management Certification programs at The Ohio State University, where he served as an adjunct faculty member. After an extensive career as a reliability and business improvement consultant, Whitley joined L2L, where he currently serves as the director of Smart Manufacturing. His role in this position is to help clients learn and implement L2L’s pragmatic and simple approach to corporate digital transformation. Eric’s email: editor@leading2lean.com
RELATED CONTENT
-
Grappling with the World's Complex Energy Transition Through an ESG Lens
With a long list of contributing factors, the world is barreling headlong into an energy transition that’s full of challenges, opportunities and lofty net-zero goals.
-
Intermediate Class Valves, the Forgotten Classification
These days, piping designers use automated systems that default to standard classifications such as pressure classes of 150 to 2500 for valves and associated equipment.
-
Creating a Standard for Severe Service Valves
Severe service valves are offered in several standard designs, including non-return, isolation and control types.