Pneumatics is one technology where the demand for and innovation of wireless tools is growing. The latest wireless pneumatic devices remotely connect operators to pneumatic components such as valves—and often use phones, tablets and laptops to do it. Their new capabilities and direct, wireless access provide end-users with valuable benefits that can reduce downtime while improving convenience and efficiency.
IMPROVE EQUIPMENT EFFECTIVENESS
Pneumatics is one of the most widely used and effective technologies in today’s automation systems. Pneumatic systems are ideal because they are proven to provide long operational life, as well as a low-cost and effective way to add various motion to equipment. As technology suppliers add intelligence to these widely used devices, OEMs and manufacturers have opportunities to build more sophisticated, smarter automation systems.
As sensing technology has advanced, it is now easier to monitor pneumatic actuators and valves and get actionable data without being cost-prohibitive. Pneumatics now ties in with the overall automation system to provide comprehensive, actionable performance data that can improve overall equipment effectiveness (OEE).
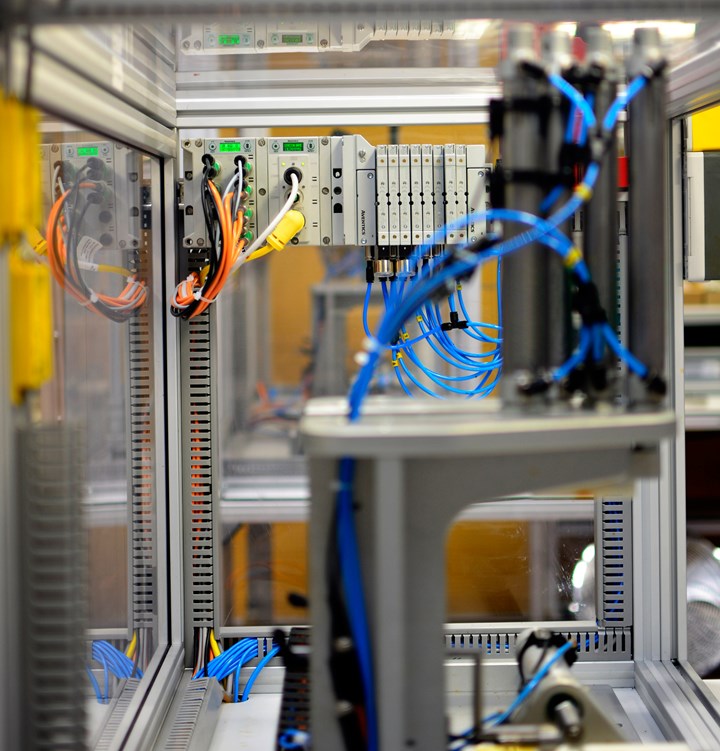
Pneumatic valve technology plays a critical role in today’s high-speed automation machines and platforms. New wireless technology is now being introduced to enable easy valve system commissioning and configuration, as well as real-time access to pneumatic component diagnostics.
Reliable wireless communication interfaces now network large installations of widely distributed sensors, freeing facilities from the time and costs required to physically connect devices and freeing personnel from the need to physically check assets that could be out of easy reach.
These smart pneumatic technologies deliver actionable data, in real time, that machine operators and plant engineers use in two critical ways: to immediately respond to problems and issues with pneumatic components and to correct them before they cause significant problems or lead to significant downtime for automation systems.
Robust, high-performance pneumatic systems with real-time sensor data also provide the basis for data-driven, preventative maintenance programs. Data on valve performance, and whether pneumatic function is falling outside of established thresholds, now provides the basis for more predictive maintenance programs, helping to prevent unscheduled downtime by planning for component servicing and replacement in the most efficient manner possible.
SIMPLIFY VALVE COMMISSIONING AND CONFIGURATION
Even if it’s planned, any downtime on the plant floor is money lost. This includes installation time. Easy commissioning and configuration get valve systems in service—and machines running—more quickly.
An advanced, modular fieldbus valve system interface helps simplify commissioning, installation and integration of pneumatic valves into the overall automation system. Such fieldbus valve systems enable faster start-ups and enhanced diagnostics that help identify problems earlier and faster, contributing to increased equipment uptime and greater productivity.
A pneumatic fieldbus valve system connects to sensors incorporated with an automation system’s pneumatic components. The system then captures and manages the data that sensors collect to provide operators access to valve status and diagnostics through a web browser dashboard. These fieldbus valve systems replace conventional hardwired solutions and integrate communication interfaces and input/output (I/O) capabilities to pneumatic valve manifolds.
When choosing a fieldbus system, it’s important to select one with a full range of automation communications protocols, including EtherCAT, EtherNet/IP and ProfiNet. This enables PLCs to turn valves on and off more efficiently and to channel I/O data from sensors, lights, relays, individual valves or other I/O devices via various industrial networks.
The modularity of fieldbus valve systems often invite innovation that can amplify their capabilities. For example, there’s now a wireless automatic recovery module that can easily be added as a “clip” into compatible, existing fieldbus platforms. The module provides real-time, wireless access to pneumatic component diagnostics, as well as supports easy valve system commissioning and configuration.
Sensor data from pneumatic devices networked through the fieldbus platform are sent via secured Wi-Fi connection to a web-based dashboard that can be accessed by any smartphone, tablet or laptop. Using the wireless automatic recovery module allows the valve manifolds to be fully commissioned and monitored prior to machine start-up; this includes setting operational thresholds and alarm settings.
It’s an example of how wireless interfaces can more easily support a fieldbus platform’s diagnostic and commissioning capabilities via an internal Wi-Fi access point. This wireless access can improve operational convenience and efficiency, especially in machine settings where the valve system is located inside the machine or on the ceiling.
This web interface can also be used to commission all the features of the fieldbus module when it is first integrated into the overall automated production system. Operators using a wireless laptop or tablet can commission networking features such as IP address, subnet mask and gateway addresses for the fieldbus module, as well as valve manifold settings such as baud rates.
EFFICIENTLY DIAGNOSE COMPONENT ISSUES
Like drawn-out commissioning and configuration, endless troubleshooting can also eat away at productivity. A wireless automated recovery module clipped into a fieldbus platform can provide operators with convenient, wireless access to diagnostics that help identify potential issues quickly and efficiently.
Devices ranging from pneumatic cylinders and valve manifolds to pressure sensors and air preparation units are constantly generating performance data. This is essential information that operators need so they understand how all the pneumatic devices connected through the fieldbus communication interface are performing and can be diagnosed when problems occur during production.
Once an automated system has been commissioned, configured and is up and running, the fieldbus valve system can send error notifications for alarms, voltage levels, short circuits, module errors, open load errors and distribution errors to the web-based dashboard. To address issues in near-real time, operators can configure the system to send alert notifications to appropriate laptops or smartphones if critical thresholds threaten to be exceeded.
Machine operators can use these alarms for detailed guidance about precisely which device or valve component may be approaching failure thresholds, providing the kind of actionable data needed to support the servicing of a device during the next scheduled downtime for machine maintenance.
Performance and diagnostic data that is aggregated to the website dashboard is, obviously, pneumatic-specific. However, the end user can combine that data with other data from the machine’s PLC and other sensors to conduct more sophisticated analytics about overall automation performance. Using this real-time data develops deeper insights into machine productivity and energy efficiency.
One example of an application that benefits from such prolific and detailed real-time performance and diagnostic data is the engine test stand. Engine test stands are just what they sound like. They’re used to run vehicle engines, often to their limits, to monitor the engine’s overall performance. Pressure sensors are key measurement components found throughout these testing systems. By integrating a fieldbus valve system interface and wireless automatic recovery module, manufacturers can add a user-friendly way to capture and manage sensor data and access real-time pneumatic component diagnostics. The solution also integrates communication interfaces and I/O capabilities to the test stand’s pneumatic valve manifolds.
QUICKLY RESTORE FUNCTIONALITY AFTER FAILURES
Power spikes and other critical events can damage the modules of a fieldbus system. If they are not backed up in any way, a controls engineer must recover and reprogram valve system functionality through a PLC or laptop. This incurs downtime and pulls experts away from other important work.
As its name suggests, the wireless automatic recovery module provides an automated recovery capability in addition to wireless access to commissioning and diagnostics. Each time the fieldbus manifold is powered up, its configuration and parameter settings are saved into the wireless automatic recovery module’s nonvolatile memory.
If a critical event damages any of the modules of the fieldbus system, the wireless automatic recovery module will automatically reconfigure any replacement modules without the need for a laptop or user commissioning. The module automatically saves all the configuration data, avoiding valuable time loss and allowing the valve manifold to quickly get back into service.
This kind of backup intelligence, based on the use of smart digital technology, is a key requirement for many automation end users: Instead of requiring a controls engineer for system recovery and reprogramming, a service technician or machine operator can easily perform the replacement to restore the valve function with minimal effort and without using any special tools or software.
STREAMLINE DIGITAL TRANSFORMATION
The latest wireless pneumatic devices demonstrate a key IoT principle: using advanced digital technology to maximize the uptime and productivity of complex automation systems. Wireless interfaces can simplify and streamline how plant floor personnel or maintenance technicians access diagnostics from pneumatic valve systems. There’s no need to gain access to the machine’s network or download a special app—the real-time, actionable data is safely available via a standard web browser.
The wireless automatic recovery module is not meant to replace high-speed, wired automation networks like EtherNet/IP or ProfiNet for valve control. Rather, it provides a simple wireless diagnostic interface into smart pneumatic valve systems platforms and represents a key addition to the expanding range of smart digital technologies being integrated into today’s pneumatics.
It is also an example of how pneumatics technology providers continue to invest in innovation and advanced thinking about ways to leverage proven technologies like wireless connectivity. As a result, manufacturers can reduce production downtime and simplify valve system commissioning. In addition, these developments are designed to create a path for using diagnostics and pneumatic device performance data for analytics and further expanding IIoT functionality.
About the Author
Adam Gibson, application engineering manager, is responsible for managing advanced customer support of all fluid power components and systems at Emerson. Gibson has over 25 years of experience in the pneumatics industry. He provides expert guidance and input into the development of new components and systems, with emphasis on industrial communication and related technologies.
RELATED CONTENT
-
Electric Actuators in the Oil and Gas Industry
Actuators in the oil and gas industry operate many types of valves, and they must do so with great precision and accuracy.
-
The Next Step in Functional Safety
The primary goal of functional safety is to prevent accidents.
-
HVOF Coatings for Severe Service Valves
Chrome carbide is one coating that can be done during manufacturing or repairs that extends service life of valves and other flow control components.