Water Hammer's Impact on Valve Operation and Piping System Design
The risks of water hammer to fluid systems can be catastrophic.
#pressure-relief
It's a well-known fact that most liquids are inherently non-compressible, signifying that no matter how much pressure is exerted on them, their volume remains unaltered. This characteristic proves invaluable in power transmission systems like hydraulic pistons. However, it can also pose a risk of catastrophic accidents in piping systems. This article addresses such a potential risk, that of water hammer.
Water hammer, a phenomenon rooted in this non-compressibility principle, occurs when a volume of fluid traveling through a pipe suddenly has its direction altered. Because this fluid carries inertia due to its mass, it abruptly halts the momentum, resulting in a rapid surge in pressure. Due to the non-elastic nature of the fluid, this excess energy cannot dissipate or be absorbed, leading to the creation of a pressure wave that travels through the pipe until it finds a way to dissipate the energy. This pressure spike is directly proportional to the volume, much like what would transpire if an unyielding object collided with a wall at high speed. For instance, a 50-kilometer-long pipe with a nominal diameter of 24 inches, filled with water, possesses an approximate mass of 16,000 tons. Any disruption to this mass's momentum demands a significant amount of energy. Consequently, in large pipes, this phenomenon can result in catastrophic damage, ranging from vibrations and noise to complete pipe collapse.
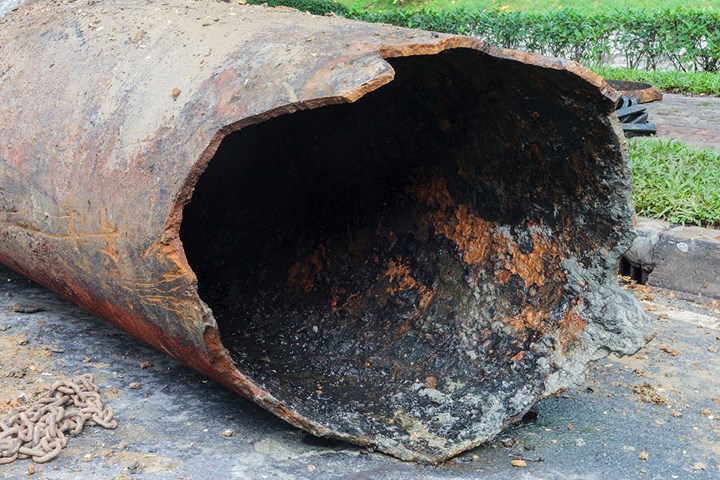
A 700 mm cast iron water pipe that burst as a result of water hammer.
Photo Credit: Cowan Dynamics
Various methods exist to prevent or mitigate water hammer, all hinging on the idea of averting abrupt changes in fluid movement or safely dissipating the wave's energy without harming the system. Valves play a pivotal role in this phenomenon, as they are engineered to alter fluid direction. Ensuring the proper operation of valves within the system is fundamental to designing an effective piping system.
So, how can valves be operated to reduce or prevent water hammer?
One effective approach involves prolonging the time during which changes in fluid movement occur. In pipes, often achieved by extending the valve's closing time, allowing for energy dissipation due to pressure loss. As a valve closes, its flow capacity decreases, which is determined by the relationship between the pressure differential across the valve and the flow rate passing through it. The higher the percentage of closure, the lower the capacity and the higher the differential pressure for a given flow rate. The pressure spike generated by closing a valve correlates with the time it takes to close it. An instantaneous valve closure yields the maximum pressure spike. While it may seem that closing the valve extremely slowly could entirely eliminate water hammer, this isn't a practical solution in all cases or for certain applications.
In many isolation or shut-off valve applications, it's essential for the valve to operate as swiftly as possible, particularly when dealing with emergency shut-off valves. This is necessary not only to promptly halt the flow, but also because on/off valves should not remain partially open for extended periods, as this could lead to damage to the closing membrane, seats, and other components due to erosion. This challenge can be addressed by implementing a dual or variable-speed system to operate the valve. Such a system enables the operator to close the valve, say, 80% of the way at high speed and then gradually reduce it in the remaining 20% to maximize energy dissipation in the shortest time. This approach also significantly reduces the valve's flow capacity in a short duration, allowing for efficient flow blockage while accounting for the necessary pressure loss to mitigate or prevent water hammer.
The actuator's operational controls manage this system, relying on valve position feedback and an energy supply system. For simple hydraulic actuator systems or those utilizing non-compressive fluids, synchronization of target position setpoints is typically achieved using limit switches or position transducers. Once the valve reaches the desired position, the system reduces the flow rate to slow down the actuator's stroke time. Similar operational configurations can also be designed for pneumatic systems or those using compressive fluids. Calculations for the time required to alter the pipeline fluid are determined through a transit analysis of the piping system.
Another common technique for mitigating the potentially damaging effects of water hammer centers around the deliberate reduction of the velocity at which fluid travels within the pipeline. This velocity, in turn, is linked to the pipe's nominal diameter. The crux of the matter lies in understanding this relationship: as the diameter of the pipe increases, it inherently provides a more expansive cross-sectional area through which the fluid can flow. Consequently, to maintain a consistent flow rate, the fluid has to move at a lower velocity within the larger-diameter pipe. Conversely, when a smaller-diameter pipe is used, the fluid must surge through it at a higher velocity to maintain the same volumetric flow rate. The more swiftly the fluid is moving, the greater its kinetic energy, and thus, the more pronounced the pressure surge resulting from abrupt changes.
Considering this, the selection of pipe diameter emerges as a pivotal design consideration. While it might be tempting to opt for smaller pipes that meet the bare minimum flow velocity requirements on paper, this approach often leads to elevated flow velocities in practice. These elevated velocities, in turn, escalate the vulnerability to water hammer during valve operations or other flow disruptions.
Consequently, a prudent and proactive strategy involves choosing pipes with larger diameters than the bare minimum specified by flow calculations. By opting for larger pipes, the flow velocity is naturally attenuated for the same flow rate. This reduction in velocity acts as a buffer, facilitating more gradual adjustments in flow and pressure. This, in turn, reduces the likelihood of pressure spikes and their associated potential for inflicting harm on the system.
In summary, the proper design of pipeline valve actuation systems is essential to prevent or mitigate the effects of water hammer in piping systems. Valves, designed to alter flow direction, impact the momentum of the fluid within the pipe. Depending on the application, valves may need to effect these changes quickly, but rapid changes can lead to increased pressure peaks and pressure waves. Introducing a variable-speed system for valve operation, coupled with meticulous fluid transit analysis and consideration of future flow increments when determining the size of piping systems, can provide a viable solution to the issues posed by water hammer in the operation of pipeline valves.
Maria Aguirre is a professional mechanical engineer with a master’s degree in mechanical engineering and a master’s degree in environmental engineering, and she is a certified professional mechanical engineer. She is the director of business and product development for Cowan Dynamics and is a Valve Magazine editorial advisory board member.
RELATED CONTENT
-
Direct-Sealing Diaphragm Valves Offer Novel Approach
As modern industries such as hydrogen electrolysis and biotech make dramatic technical advances, engineers and researchers must sometimes turn to nontraditional process control systems.
-
Introduction to Pressure Relief Devices - Part 1
When the pressure inside equipment such as boilers or pressure vessels increases beyond a specified value, the excess pressure may result in a catastrophic failure.
-
Best Practices in Pressure-Relief Valve Maintenance and Repair
In their presentation at the Valve Repair Council Repair Meeting & Exhibition, Nov. 1 and 2, 2012, in Houston, Bob Donalson and Kevin Simmons of Pentair Valves & Controls shared valuable information about maintenance and repair programs for pressure-relief valves.