Weight-loaded, Low-pressure Protection Devices 101
In the world of low-pressure and low-vacuum relief valves—defined for this article as valves with settings less than 15 psig—there are several different common valve configurations.
#basics #knowyourvalves
In the world of low-pressure and low-vacuum relief valves—defined for this article as valves with settings less than 15 psig—there are several different common valve configurations. These configurations include spring-loaded valves, pilot-operated valves and weight-loaded valves. These valves can be set up in a variety of configurations with all sorts of different bells and whistles based on customer preference and tank-specific needs. In this article, however, we are going to focus on the most basic: the weight-loaded relief valve.
HOW WEIGHT-LOADED VALVES WORK
The weight-loaded valve is king in low pressure applications due to its simplicity. There is very little to go wrong with a weight-loaded valve because the technology is based upon the ever-constant force of gravity. If installed correctly and properly maintained, it will work every time. The biggest drawback with the weight-loaded valve is the weight itself. A large valve can get very heavy very fast as the valve set pressure is increased. For this reason, most weight-loaded valves have set pressures less than one psig. The science behind weight-loaded valves should sound familiar, you were likely first introduced to the concept of pressure in junior high. To calculate how much weight is required to reach your desired valve set pressure, use the following formula:
P x A = F, where desired set Pressure multiplied by the effective Area of the pallet/disc (the area that the pressure acts upon while the pallet is closed) equals the amount of Force (weight) required to hold the pallet closed (until reaching the set pressure).
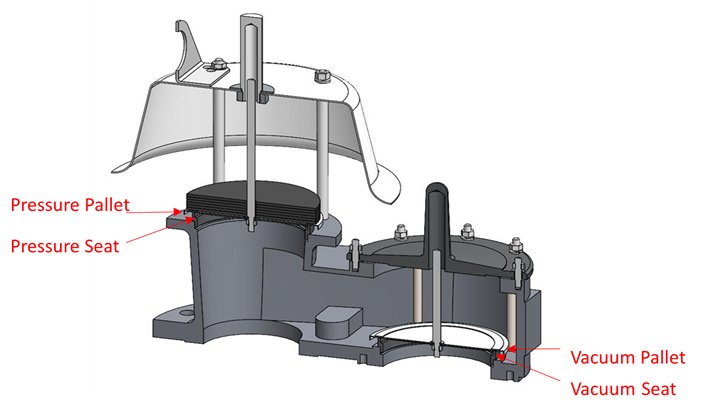
Figure 1. Pressure and vacuum relief valve.
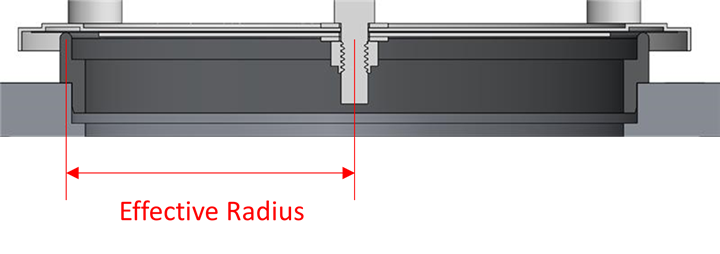
Figure 2. Effective area.
DEFINITIONS:
Set pressure: The pressure at which a valve is calibrated to crack open
Effective area: πr2 (in this case r is the effective radius shown in Figure 2)
Force: Total dead weight of the pallet assembly
One of the keys to success with a weight-loaded valve is the tank nozzle is level prior to mounting the valve. If the tank nozzle is not level, the normal forces (gravity) of the weight can cause the valve pallet to interact with the valve seat in an uneven fashion. This typically manifests itself in lower than calculated set pressures and/or inconsistent set pressures. Valve leak rates will also be negatively impacted which results in an increase of fugitive emissions being released.
Valve soft goods maintenance is also a key contributor to a weight-loaded valve’s performance. Soft goods wear out over the course of time during normal operation. Therefore, it is important to follow the manufacturer’s maintenance recommendations to ensure the best performance from your weight-loaded valve.
WHY WEIGHT-LOADED VALVES ARE NECESSARY
Weight-loaded relief valves are available in pressure only, vacuum only or with both pressure and vacuum relief capabilities. These devices are typically used to vent storage tanks to protect against overpressure and/or excessive vacuum conditions during normal operations. Storage tanks need to be able to breathe to stay within a tank’s maximum allowable working pressure (MAWP) and maximum allowable working vacuum (MAWV). Pressure or vacuum conditions outside of the MAWP and MAWV limits can result in structural failure of the storage tank, and possibly much worse depending on what media is stored inside the tank. The most common reasons a tank may need to breathe under normal operation include the following:
- Moving media into or out of a storage tank
- Weather changes (temperature change or atmospheric pressure change)
Weight-loaded relief valves also provide venting capacity during emergency events but should be used in addition to emergency relief valves. They are typically not designed or sized to be the only emergency relief for a tank.
WHERE WEIGHT-LOADED VALVES ARE USED
Weight-loaded relief valves are most commonly used on thin-walled storage tanks with relatively low MAWP and MAWV ranges. These types of tanks are common in the upstream oil production industry, the downstream petrochemical industry and other industrial liquid storage applications.
CODES AND STANDARDS
API 2000: Venting of Atmospheric and Low-Pressure Storage Tanks, 7th Edition and ISO 28300: Petroleum, Petrochemical and Natural Gas Industries — Venting of Atmospheric and Low Pressure Storage Tanks, are the current design standards that govern the design of venting devices for low-pressure tanks such as weight-loaded relief valves (as well as the other types of emergency and relief valves). These standards are intended for tanks containing petroleum and petroleum products but are also commonly applied on tanks containing other liquids.
About the Author
With 31 years in the industrial sector, Stuart Prestridge has worked primarily in oil and gas/petroleum refining. Twenty years was spent in industrial construction management, specializing in process instrumentation and controls. He has worked the past 11 years for Setpoint Integrated Solutions Inc., serving in several leadership roles across the organization. Prestridge’s role as corporate director of sales focuses his time and energy on building out OEM partner relationships, evaluating potential additions to product offerings, as well as the identification and evaluation of M&A targets for expansion and growth.
RELATED CONTENT
-
Air Valves in Piping Systems
Liquid piping systems are prone to collecting air from incoming fluids, pumps and connections.
-
The Future of Valve Manufacturing is Already Here
Companies in the valve and control products industry are responding to a confluence of forces that are changing the landscape of manufacturing — automation, agility and digitalization to name a few.
-
Selecting Non-metal Materials for Valve Components and Coatings
Non-metallic materials are commonly used for valve components, and the selection of non-metallic materials for valve design and for application-specific conditions is critical to ensuring product reliability.