Alleviating Control Valve Erosion Critical for Uptime
Process steam leakage can affect power plant uptime.
#maintenance-repair #components
Ongoing process steam leakage in power plant control valves due to erosion from wet steam should be addressed to maximize uptime.
Facilities operators need to ensure continued, uninterrupted performance, and prevent the impact of inefficient processes and unplanned downtime. Power plants with inadequate drain set ups, incorrect bypass operation, improper valve calibration or inadequate pre-warming processes continue to be impacted by wet steam erosion, hampering productivity.
Specifically, these issues can lead to erosion of trim components on steam valves used in critical service applications caused by flashing condensate, otherwise known as wet steam. This potentially chronic problem must be addressed if facilities are to remain efficient and cost-effective at a time when process costs are rising.
“Steam valve passing – or leakage – remains a common concern in power and processing plants that can lead to a whole host of issues, including downstream temperature rises, unplanned downtime, cracking pipes, and water hammer,” explains Mike Semens-Flanagan, global engineering director at IMI Critical Engineering. “The erosion of the valve plug and seat sealing surfaces are key reasons behind this, and must be addressed if the sector is to maximize performance at a time of great strain.
“While the common approach to mitigating trim damage involves the frequent repair and replacement of affected parts, the loss of energy and increased OpEx costs caused by this unplanned downtime is unacceptable in the current economic environment. Yet with major remedial steps such as adding drains to existing pipework, often ruled out due to costs and logistics concerns, an innovative approach is required to alleviate this pressing concern.”
One such way to minimize wet steam erosion is to ensure that any condensate has minimal contact with sealing surfaces. IMI Critical Engineering has developed EroSolve Wet Steam, which upgrades the valve’s plug, stem assembly, cage and seat ring. The solution has specially engineered sealing surfaces that optimize droplet impingement angles to reduce their impact. Its use of special, erosion-resistant, hard-facing materials also enhances trim life in a solution that can be easily implemented in any make of control valves.
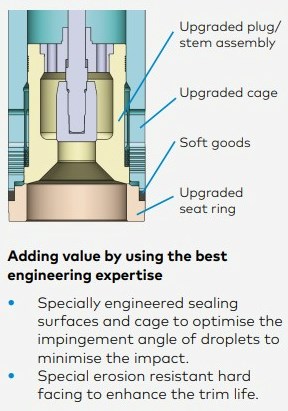
“Most traditional solutions to the problems posed by wet steam do not provide any added long-lasted benefits,” said Semens-Flanagan. “Alongside this, the complexity of fully replacing a valve within power plants can make solving the problem more expensive that the hardware itself, and this is obviously unacceptable. If the valves are welded inline there may also be substantial additional costs incurred through engineering, scheduling, cutting and re-welding valves, and post-weld inspection, creating further complexity. However, replacing the trim can help delay degradation and extend the lifetime of valves operating in conditions where erosive wet steam is common.”
The EroSolve upgrade can be carried out without changing the body, bonnet or actuator, where any downtime for repairs can carry a large cost burden. For more information on EroSolve Wet Steam, click here.
RELATED CONTENT
-
Dealing with Sand Erosion in Control and Choke Valves
Sand erosion in control and choke valves is a significant consideration offshore.
-
Proper Care of Knife Gate and Slurry Valves
How to resolve—and avoid—field failures of knife gate and slurry valves
-
The Diverse Role Valves Play in the Chemical Industry
The chemical industry is extremely diverse with more than 60,000 known products. Like all process industries, the chemical industry needs valves designed for safe, efficient and reliable process operation.