Do Current Headwinds Affect the Repair or Replace Decision for Valves?
Perspectives from a valve repair company and and OEM on what drives end users to make this determination.
#maintenance-repair #components
Repercussions from the manufacturing shutdowns and supply chain issues that arose from the 2020 pandemic have persisted. There was hope that once the COVID-19 virus vaccines were rolled out, and medical interventions were refined, that the world would return to “normal” — whatever that meant. But even three years later, many areas of the global economy still face problems with raw materials, staffing and delivery times that continue to create roadblocks for consumers and companies worldwide. The impact on the world of industrial valves is no exception.
One area where this could have a major impact is when it comes to valve repair or replacement. In the past, different organizations have rules of thumb they follow to determine this—sometimes based on predicted service life, cost, total downtime, etc. But in a world with a constrained labor force, long manufacturing and repair lead times and even shorter scheduled downtimes, has this changed?
VALVE Magazine spoke with a valve repair company and an OEM for their perspectives on today’s market. Michael Bailey, general manager of A.V.P. Valve in Lakeland, Fla., runs a valve sales and repair business. Karl Lanes is a senior director of global lifecycle services at Emerson, located in Marshalltown, Iowa
We started by asking Bailey and Lanes if there is a rule of thumb or cost target for when a valve should be repaired versus replaced, and the conversations evolved from there.
Bailey said: “Years ago we always looked at repair costs and tried to stay under 50% of the cost of a new valve. If we started to exceed that number, we’d recommend replacement. But when you do that you have to have a new valve to replace it with or the customer has to have one on order to get it in time. They also need time to cut it out, weld the new valve inline, etc. I have seen customers routinely pay 80-120% of the cost of a new valve just to recondition a $75,000 valve — $60,000 to repair the valve, and another $30,000 to cut it out of the piping system and reweld it into place. Because of that, we’re seeing more and more customers go to reconditioning.
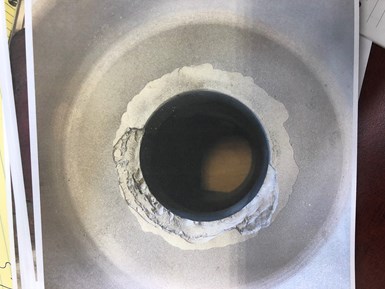
Cracked bonnet valve backseat before repairs were completed.
Photo Credit: A.V.P. Valve Inc.
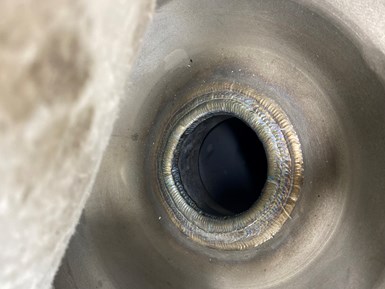
The same bonnet valve backseat post-repair.
Photo Credit: A.V.P. Valve Inc.
“Previously, we’d likely only have replaced 4- or 6-in. valves, and we’d recondition or rebuild the rest. But recently, a customer had us pull out a 20-in. valve and replace it. We also used to have more time. Most outages now seem to be 21-30 days, but in the 80s and 90s, they’d be 60 days. We’d have time to be on-site and do the work, because it wasn’t the breakneck pace it is now with some plants trying to accomplish this in just 10-12 days.”
Lanes said Emerson sees similar responses from their customers. “At Emerson, we’ve always used a cost factor of 60% of the cost of new or less and we’d recommend trying to repair or rebuild. But there are safety considerations we have to face. We don’t necessarily know what the valve’s internals are. Are they OEM parts? Are they replicated parts? We always advise using OEM parts from a safety and quality factor. Otherwise, we have to do parts analysis, materials analysis, etc., (when onsite to do rebuilds or reconditioning) and that adds time and cost.”
Supply chain challenges continue
Lanes said the number is just a guide. “The 60% cost factor has been highly fluid with today’s supply chain issues. We have not seen customers necessarily change their entire repair vs. replace strategy when it comes to supply chain issues. It has been on an asset level when making the decision to repair or replace. The maintenance manager within the plant in charge of valves will be the decision maker to decide to do a functional repair or to wait for the part or new valve to come in stock.”
He continued saying the company has been working diligently to address how COVID impacted the global supply chain, and its procurement teams have been working with suppliers to maximize availability of key components to avoid supply chain issues as best as possible.
Last year, Emerson introduced a trim cartridge repair solution for its Fisher easy-e globe valves. The cartridge is a factory-assembled repair cartridge that combines all the valve replacement parts and the bonnet and it can be dropped into existing valve bodies. This solution has helped customers by saving time previously spent to disassemble valves, identify, find and order replacement parts and then install them. Valves would also have to be removed from service in many cases causing even further downtime. By having all the components in one part number, customers and Emerson repair partners can have them in stock and ready to easily drop into place.
Supply chain issues are affecting A.V.P. and its customers, too. “We get valves in failure mode that should probably be replaced, but the new valve isn’t available, so they need to repair it (as a stopgap),” Bailey says. “Lead times used to be 12-16 weeks, and that seemed excessive, but now it can be 30- 50 weeks. It’s just crazy.”
A.V.P. has also increased its spare parts inventory. “It’s an investment but I know that at some point they’ll be sold,” he said. “I have two dedicated storage areas for our spare parts inventory for emergencies. You have to be prepared for anything with your customers. We have our core customer base in Florida that we’ve built such a strong relationship with, and we’ve gained a number of out-of-state customers that we don’t service for scheduled outages but they know we can supply them in case of emergency due to having this inventory —that’s the reputation we built.”
As an OEM, Emerson doesn’t face the same level of supply chain challenges that end users or even valve repair companies face, as they can better forecast based on their view of the entire supply chain of their products. When asked if their customers were stocking more spares, Lanes says: “You would think they would, but we have not seen the customers take on significantly increased stock levels in general themselves. This may be because the customers may not know what to inventory. Emerson offers recommended spare part lists for our customers to be able to know what parts to stock. Although, these are not too popular — likely because our customers prefer to collaborate with a service organization, such as one of our accredited service providers, who have been stocking additional replacement and repair parts as they are available.
Emerson also offers service contracts for customers. “Any service provider can provide long-term support, but it is especially important that Emerson is there when our customers truly need us,” Lanes says. “Emerson has set up their service organization with their customer needs in mind, which means we must be as local as possible to react to unplanned shutdowns. We plan for facilities with customer locations in mind, and where we cannot, we find a 3rd party service provider, who we accredit and audit to service our valves, in which case we name an accredited service provider. If we need a specialized resource, we can use remote assistance via augmented reality for a local technician can video conference with an Emerson expert.”
With no way to know when or if these challenges are going to recede, Bailey said they are urging customers to look ahead three to five years at their systems and key components, not just until their next shutdown. “I think that’s where everybody needs to go,” Lanes says.
When asked if there were certain valves that they would always recommend either repair or replace, both Bailey and Lanes agree that smaller, less engineered valves are easier to replace, as are valves that are flanged or socket-welded.
“Small lower cost isolation valves have generally been run-to-fail and repair-by-replace,” Lanes says. “With all types of valves, even with control valves, repair-by-replace is attractive when the cost of labor approaches a significant percentage of the cost of a new assembly. A new valve offers customers a high level of assurance, whereas some risk comes with repair, especially a non-OEM repair.”
Is ESG impacting these decisions?
Environmental, social and governance (ESG) concerns are also top of mind for many plants as they have committed to their shareholders to move toward zero emissions and to be more mindful overall with their resources. Emerson has set aggressive goals for itself as a company and plans to attain 20 percent greenhouse gas emissions reduction by 2028 across its own facilities, as well as a 30% reduction in carbon emissions for its customers. They have appointed a chief sustainability officer to lead and manage their strategy and assist their customers with their objectives. With this focus, Lanes expects to see changes. “With the focus on ESG, we anticipate customers may look to increase their cost threshold to repair a valve rather than replace.” He says Emerson has already seen this trend across all valve types such as control valves, pressure relief valves, and isolation valves.
While A.V.P. and other valve repair companies may not be seeing this as a primary issue today, that will likely change. As climate change and sustainability are issues that every company is being tasked with addressing, especially for the larger public companies and utility companies, this will become a driving force in the coming years. With government mandates and regulations, corporations are going to be forced to address these issues across all parts of their operations.
Employee retention
Employee turnover has had a noticeable impact on A.V.P.’s customers according to Bailey. His team prepares reports on their installed products and supplies them to customers well in advance of planned shutdowns. “We pass these reports on to our customers, but then two years later when the next shutdown occurs, they’re gone and it’s gone by the wayside and wasn’t shared with their successor. Since we are proactive, we review the reports regularly and if we see that the valve needs to be replaced next turnaround we follow up. It requires a lot more communication than what we had in the past, and a lot more of my employees’ time to do all the follow up,” he says.
Bailey says both he and his customers are having trouble finding employees. “The average age of my workforce is 45-50 years old. I can’t find young people who want to do the work. We have local trade schools and union shops that have zero participation in their training programs right now, and some have closed. When I was a kid you had to have a relative doing these jobs to get in to these companies. I’ve already started to help pay for tuition for training programs for people, as long as they commit to coming to work for me when they complete the program.”
A.V.P. has also changed its business model, adding more capabilities to help alleviate supply chain delays and staffing shortages. “We’ve changed our business, too,” Bailey says, “and are now stripping down valves and re-Stelliting control valves ourselves, as well as high-temperature gate valves, to be able to meet our customers deadlines and get them back online in time.”
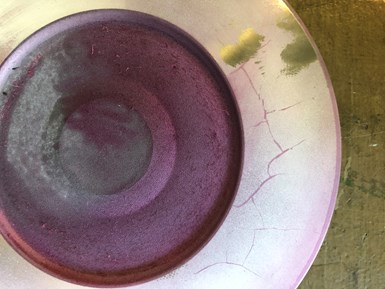
A parallel slide gate valve disc from an A.V.P. customer that required stripping, re-stelliting and post-weld heat treatment for a total repair.
Photo Credit: A.V.P. Valve Inc.
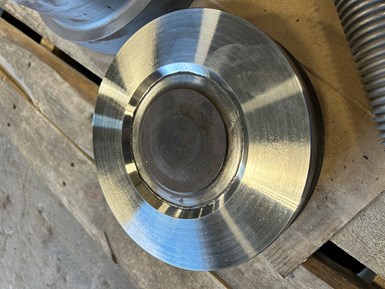
The same disc after it has been repaired.
Photo Credit: A.V.P. Valve Inc.
“It has become imperative that we all work together,” Bailey says. “We help as much as we can to be successful and serve our customers that’s what these shops are, we’re customer service on a very, very high level. And during outage season—and always—that’s critical.”
While there may not be a direct link between the Covid pandemic and a company’s decision to repair or replace valves, there is no doubt there was a major impact on the industrial workforce and supply chain that forced companies to pivot the way they approach not just shutdown preparation but all parts of their business. New product introductions such as Emerson’s trim cartridges and all the predictive and monitoring tools available today definitely help, but clearly that isn’t enough.
With an already graying employee population in the industrial world, companies need to act with urgency to ensure the successful future of their operations.
RELATED CONTENT
-
In the Air: Wireless Trends in Smart Pneumatics
In today’s wireless world it’s no surprise that automation and manufacturing spaces have embraced—and sought out—the connectivity and convenience that wireless technologies offer.
-
The Valve Industry Finds Value in ESG Initiatives
The valve manufacturing industry in North America is one of the industries that have embraced this new way of thinking and is leading the way with the integration of environmental, social, and governance (ESG) initiatives. These initiatives range from valves designed to mitigate climate change to community involvement activities.
-
Gaskets Are Not Created Equal
Gaskets are near the bottom of the food chain of valve components; trim, body materials and packing seem to get a lot more press.