How the EPA's Emissions Rule May Impact Actuator Choices
The move toward net zero emissions by 2050 was just released as part of the COP28 meeting in Dubai.
#actuators #standards #ball-butterfly-plug
Climate-related disclosures are becoming an essential and expected element of corporate communications, and all signs point to these disclosures becoming mandatory. Investors, communities and stakeholders are pressuring companies of all sizes to act on the environmental and social aspects of their performance. Focusing on environment, social and governance (ESG) efforts could be a differentiator when it comes to securing new contracts or customers for oilfield services. The recent surge of focus on ESG matters by investors and other affected stakeholders has only been intensified by current public health, economic and societal crises.
Essentially, ESG is meant to be a way by which companies can be assessed or ranked for a wide variety of factors that measure the non-financial, social impacts of their investments and operations. At the same time, ESG is being used to provide socially conscious investors with a range of business and investment opportunities.
Some of the ESG target highlights that can shape the industry are:
• New targets to reduce methane and greenhouse gas (GHG) emissions intensity from its operations by 30-50% by 2030, and net zero by 2050.
• Advancing the commitment towards new technology along with diversity, equity and inclusion.
• Expanding safety programs to include advances in targets for health and safety.
Along with the new ESG requirements, many gas utility, transmission and midstream and gathering companies, and gas utilities are being required to install rupture mitigation valves (automatic control valves or remote-control valves) to meet Pipeline and Hazardous Material Safety Administration’s (PHMSA) “Final Valve Rule.” In addition, the Environmental Protection Agency, under the direction of President Biden, is proposing changes to the Clean Air Act, 40 CFR 60. First proposed in the Federal Register on November 15, 2021, and after a year of comments, the EPA released an update that was printed in the Federal Register on December 6, 2022. The final changes were released on December 2, 2023, in conjunction with COP 28 in Dubai. The EPA is implementing “New Source Performance Standards” (NSPS, also known as NSPS OOOOb) for greenhouse gas and volatile organic compound emissions from the oil and gas industry. NSPS OOOOb will be backdated to December 6, 2022, the date the supplemental proposal was released. The EPA is also implementing new emission guidelines (also known as EG OOOOc) for the states to follow in establishing standards to reduce greenhouse gas emissions. One area the EPA is targeting is the reduction of methane and volatile organic compounds (VOCs) by disallowing the use of natural gas-driven controllers at new, reconstructed and modified sources of emissions. This proposed rule was sent to the Office of Management and Budget (OMB) at the White House on September 28, 2023. The OMB should have this finalized and printed in the Federal Register by late 2023 or early 2024. Once enacted, owner/operators of oil and gas facilities will have 12 months to comply with NSPS OOOOb. The states will have two years to submit their Emission Guidelines to the EPA for approval and then owner/operators will have three years to comply with that state’s emission regulations.
With thousands of gas-powered actuators currently operating in the field, valve operation in the gas industry can be a major source of greenhouse gas emissions. Until recently, there were few viable alternatives available to meet performance requirements within the existing pipeline infrastructure. Historically, pipeline valves are operated using standard efficiency gear operators, remote controlled actuators or automatic controlled actuators as determined by the application, valve torque, available operating media and preference of end users. In the case of larger diameter ball valves, even when these valves are operated infrequently, “convenience actuators” are often installed for the health and safety of personnel.
These convenience actuators are installed at substantial installation cost and maintenance. Driven by “human factor specifications,”1 this approach is taken to keep operations personnel from turning handwheels hundreds of rotations to open or close a valve, as is the case with standard efficiency gear operators. These convenience actuators are often low-pressure pneumatic (with regulators and relief valves), gas/hydraulic oil (also referred to as gas over oil) and direct gas actuators. Unless instrument air is available in the case of low-pressure pneumatic actuators, the above listed actuators require the use of natural gas from the pipeline to operate. During operation of pipeline-gas assisted actuators, natural gas exhausts to the atmosphere. While once considered acceptable, this methane venting is now considered fugitive emissions of greenhouse gases.
Quantitative and verifiable reduction of greenhouse gases is a prime environmental initiative in corporate ESG sustainability and is rapidly gaining clarity and traction. This new focus is driving the design of new solutions using high-performance manual and electric alternatives to gas-powered valve actuators. These next generation actuator packages are key to achieving aggressive and responsible ESG goals by reducing Scope 1 and Scope 2 greenhouse gas emissions. New products on the market, such as high-efficiency worm, planetary and spring return gears, are finding a place in energy and industrial applications. A high efficiency gear is loosely classified as any gear that is greater than 50% efficient. Standard-efficiency worm gears, most prominent in valve actuation, are typically 35% or less efficient by design, as this makes the gear set inherently self-locking, meaning torque driven from the valve stem through the output of the gear will be transmitted through the gear train to the input (back driven). To overcome backdriving/non-self-locking gear trains, an anti-back drive device must be employed in many applications to make these advanced actuators suitable and compliant. With the proper design, the use of high-efficiency gears provide valve actuation that can reduce power consumption or work by more than 300% in many applications while eliminating the venting of greenhouse gases.
High-efficiency worm and planetary gears can significantly reduce the work required to operate valves over standard efficiency worm gears. The benefit for the customer is easier manual operation compared to that of a standard efficiency gear. An additional benefit is decreased operation time in manually intensive operations such as pig launching and receiving.
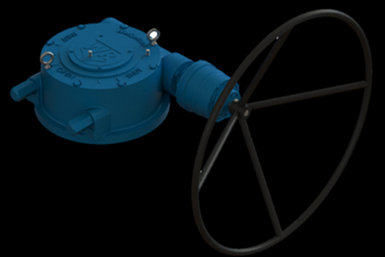
Figure 1: High-efficiency worm gear.
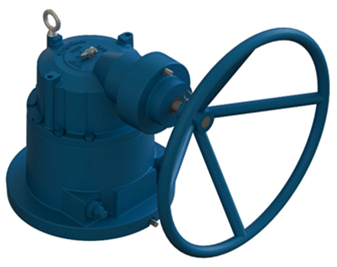
Figure 2: High-efficiency planetary gear.
High-efficiency gears can also be coupled with electric actuators to reduce operating times over conventional gears and power consumption by as much as 70%. But remember, the cleanest energy is that which is not consumed. The use of high-efficiency gears, especially planetary gears, are being used to significantly reduce power consumption while still meeting performance requirements; a sample calculation of the power consumption for a standard-efficiency worm gear compared to a high-efficiency planetary gear utilizing 16-, 20-, and 24-in. 900 ANSI valves is shown below. The same electric actuator was used in all cases to illustrate the differences.
Figure 3: 3 CHARTS GO HERE
The following graphs show power consumption per cycle, over a 10-year period, and over a 30-year period.
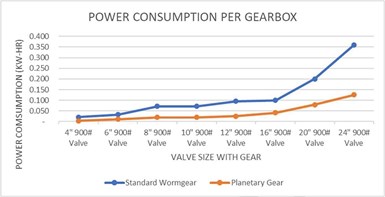
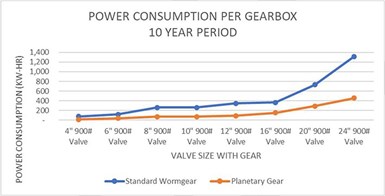
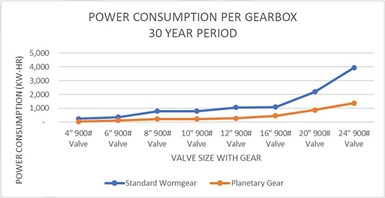
As one can see from these calculations, power consumption is often reduced by more than 50%. This reduced power consumption of this sample project results in a lower carbon footprint if conventional power generated using fossil fuel is required. This is shown in the chart below.
Not only does high-efficiency planetary gear technology help reduce the scope 2 GHG emissions compared to a standard-efficiency worm gear but, in many cases, the reduced power consumption allows for the use of a DC motor in conjunction with a renewable energy source such as a solar panel and an uninterrupted power supply. This enables the creation of an “off the grid” solution. This can be especially beneficial in remote areas where a zero-emission solution can be provided, eliminating any scope 1 and 2 emissions, while dramatically reducing the infrastructure cost of bringing power to those remote areas.
The cleanest energy is that which is not consumed.
Another new technology that is gaining traction is the development of mechanical spring-return or failsafe gears. Spring-return gears can be used in a multitude of configurations to fulfill different operating conditions that historically required the use of hydraulic fluid and/or pipeline power gas. These engineered gears can be used in manual applications, manual-reset automatic control applications, manual-reset remote control applications, and when coupled with a motor operator, spring-return gears can be used for remote fail-safe ESD applications. Current spring-return gears out in the market are built using a high-efficiency planetary gear platform.
Spring-return gears can be operated manually using a lever and spring combination in one direction and the handwheel for the other. This is an emission-free solution to a convenience gas-over-oil actuator that uses a lever-operated solenoid valve to open and close the valve or a self-contained hydraulic spring-return actuator. The operator would use the lever to stroke the valve in the “fail direction” by manually actuating the trigger release mechanism that holds the spring. This setup would require the operator to stroke the valve back to its “ready” position using the handwheel. The benefit to the employee operating the valve in a manual fail-safe application is reduced operation time and workload of the planetary gear to compress the spring versus a standard gear or hydraulic pump. The benefit for the organization is less physical work and stress for the employee compared to a commercial gear, while at the same time reducing the organization’s methane emissions to zero for each valve stroke.
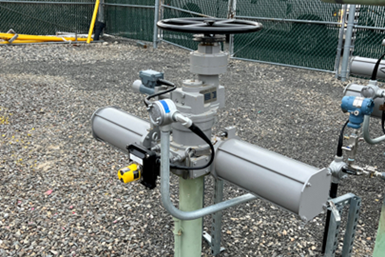
Figure 5: Manual reset spring-return gear.
Manual reset spring return gear
Spring-return gears can be used as manual reset, standalone emergency shut-down devices. These can be designed to operate utilizing line pressure from a high- or low-pressure pilot or pressure switch in an automatic control strategy, or by receiving an electric signal from the operator’s control room in a remote-control strategy. In either of these configurations, the gear would be set up to go to a “fail position” when the signal was received — the spring would be released allowing the valve to travel to its fail position. The valve would again need to be manually reset to the “ready” position by operating the gear using the handwheel. This allows for quick operation in the case of an upset condition while keeping an operator in the control room from resetting a valve to its ready position without someone first going to the site to identify what caused the upset condition, a common industry application.
Spring-return gears can also be coupled with an electric actuator to provide an all-electric, mechanical fail-safe actuator. Since no gas power is required for this type of setup, valve operation is inherently emission free. Spring return gears are independent of the motor operator and therefore can be used with almost any multiturn electric actuator manufacturer, allowing the end-user to maintain conformity of products in their facility or pipeline, helping with spare part reduction and operator training/qualification.
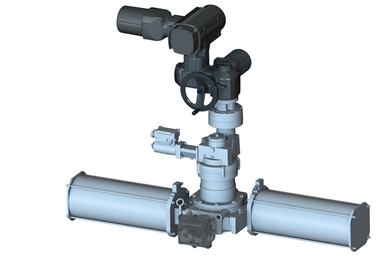
Figure 6: Spring-return gear with actuator.
In an electric fail-safe application, not only does the customer get the benefit of an emission-free mechanical fail-safe device, but they also get the benefit of reduced power consumption, reduced operating times and reduced infrastructure costs. By using the mechanical advantage of the planetary gear, the output torque required by the actuator is reduced allowing for a smaller motor that utilizes less power.
In short, electromechanical/manual-mechanical alternatives to gas-powered actuators can help achieve environmental objectives, manage longer term asset costs and provide operational safety in the following ways:
- Eliminate exhaust emissions
- Reduce leak paths of tubing and fittings
- Eliminate valve creep in ESD valves due to temperature change and piston leak
- Reduce maintenance over the life of the asset
- Reduce the amount of work required to manually open or close a valve
- Reduce power consumption of electric actuators
- Assist in meeting performance requirements such as speed of operation
Every company and individual has a direct and vital role to play in delivering a shared energy future that is more suitable, just and ultimately sustainable. This requires continued collaboration with stakeholders, challenging the status quo and pushing the boundaries on innovative thinking by providing change in society.
1https://www.valvemagazine.com/articles/the-human-factor-in-valve-operation
SIDEBAR: Explaining Scope 1, 2 and 3 Emissions Across a Value Chain
The Greenhouse Gas (GHG) Protocol, a multistakeholder partnership of businesses, nongovernmental organizations (NGO), governments and others was convened by the World Resources Institute and the World Business Council for Sustainable Development (WBCSD). The mission is to develop internationally accepted standards and tools for GHG accounting and reporting, including definitions of how to translate business activities into emissions figures, and is the leading standard used by many global organizations. Organizations, both nonprofit and for profit, have developed toolkits and templates to guide companies in how to measure and report on their GHG emissions. At the core of this is dividing and defining different emissions “scopes” into scope 1, scope 2 and scope 3) for accounting and reporting purposes. The primary emissions measured as GHG emissions for the reporting include: CO2, CH4, N2O, HFCs, PFCs, SF6 and NF3.
Scope 1: Direct GHG emissions
These emissions occur from sources and facilities owned or controlled by the company, including its furnaces, vehicles, emissions from production, etc.
Scope 2: Electricity Indirect GHG emissions
This measurement comes from upstream activities including supply chain measures. Among the factors tracked for Scope 2 are purchased goods and services, capital goods, transportation and distribution, waste, business travel, leased assets, and employee commuting contributions to GHG.
Scope 3: Indirect GHG Emissions
These activities occur downstream from a company, and include processing, transportation and distribution of completed, sold products; how products are discarded or recycled at the end of their useful life, leased assets, investments and franchises.
What is required to be reported? For now, in many cases, nothing. That is still being legislated and determined by organizations from local municipalities to global gatherings such as United Nations Climate Change where nearly 200 parties came together to develop suggested solutions for a greener future for us all.
awk Industrial Sales Inc. He has over 30 years’ experience in the valve and actuator industry. His focus is on methane mitigation in valve operations for the oil and gas industry.
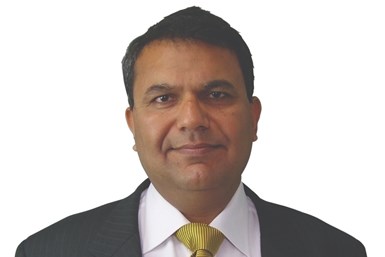
Gobind N Khiani is a distinguished alumnus of the University of Calgary. Along with a Fellowship, he has been on the Board of Directors for Energy Sustainability Training for Young Engineers and Geoscientists and Canadian Prairie Group of Chartered Engineers since 2019, and also serves as chairman of the end-user group at API 609 and vice chairman of Standards Council of Canada, and is past chair of the CBEC of APEGA.
RELATED CONTENT
-
Understanding Torque for Quarter-Turn Valves
Valve manufacturers publish torques for their products so that actuation and mounting hardware can be properly selected.
-
Actuator Issues? Use This Checklist!
While there may be 40 reasons valve actuators may stop working, there really is only a handful of components that can cause the problems. So, if you have an actuator on the fritz, here are the five things you need to check.
-
Ball Valve Coatings: Different Coats for Different Apps
Coatings protect valves and actuators against wear, erosion, chemical attack and other forces that threaten their durability and effectiveness.