PFAS Chemicals and PTFE: Should the Valve Industry Be Concerned?
Legislation moving through Congress could affect the future use of thousands of PFAS chemicals (per- and polyfluoroalkyl). The house passed H.R. 2467 in July of 2021 and, though the bill is general in nature, it assigns the responsibility to the Environmental Protection Agency (EPA) for determining which PFAS chemicals will be controlled or banned altogether.
#materials
Legislation moving through Congress could affect the future use of thousands of PFAS chemicals (per- and polyfluoroalkyl). The house passed H.R. 2467 in July of 2021 and, though the bill is general in nature, it assigns the responsibility to the Environmental Protection Agency (EPA) for determining which PFAS chemicals will be controlled or banned altogether. While the bill has not yet passed the senate, similar legislation has already become law in eight states. It is state legislation that is most concerning to both the valve and sealing industry, since states usually do not have the resources to perform deep research into the issue and tend to revert to a shotgun approach.
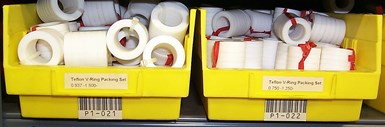
PTFE is used to manufacture packings for demanding corrosive services as well as ultrapure applications such as food preparation.
Of concern to our industry is that all PFAS chemicals, of which there are more than 4,500, will be lumped together along with a valve industry mainstay, polytetrafluorethylene (PTFE). If this occurs the valve industry would have to find an effective replacement for most floating ball valve seats, many gaskets and seals, as well as components that make fugitive emissions packings effective.
VALVE INDUSTRY PRODUCTS THAT USE PTFE
As a refresher, here are the primary areas where PTFE is a key ingredient in the product mix of the valve industry:
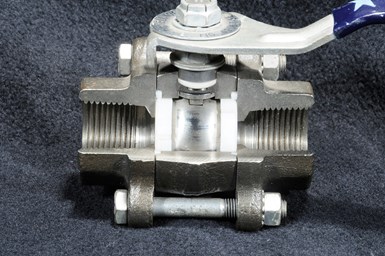
The ball valve industry relies heavily on PTFE seated ball valves for many applications in a multitude of industries. Replacing PTFE in all ball valves would be a difficult proposition.
- Ball valve seats. Without the introduction of PTFE resilient ball valve seats in the late 1950s, the floating ball valve industry would not be the giant that it is today. These highly chemical-resistant ball valve seats assure zero or near-zero leakage in many applications in some of the most dangerous and volatile services in industry.
- Liners for valves and piping. These thin liners applied over otherwise corrosion-susceptible steels and piping allow the components to operate in extremely harsh service environments.
- Packing materials. PTFE packings have been a material of choice for decades, serving as excellent seals for a variety of service applications, including food-grade applications.
- Gaskets and seals. Like the PTFE packing materials PTFE gaskets and seals fill a vital role as sealing materials for many valve types and service applications.
Some valves are lined with PTFE to make their wetted areas resistant to harmful corrosion-causing fluids.
- Lubricant for low-emissions packings. Today’s sealing technology relies on PTFE as an integral ingredient in low-emissions packings. Without their critically important PTFE binders and lubricants, low-emissions packings ability to protect the environment from dangerous volatile organic compounds (VOCs) would be seriously hindered.
PFAS PROBLEMS ARE CAUSE FOR CONCERN
There is a genuine problem with some PFAS chemicals that are primarily used in commercial applications. Harmful, cancer-causing PFAS chemicals and compounds have been found in such innocent items as stain and water-resistant products, non-stick cookware coatings and fire-fighting foam. Dangerous polytetrafluoroethylene (PFOA) and perfluoro octane sulfonic acid (PFOS) chemicals have been the primary culprit in these issues. The leachability of some of these chemicals into the water table has also been well documented.
It is important to note that the major U.S. manufacturers of PTFE products for the industrial sector do not use either PFOA or PFOS in their PTFE manufacturing processes and have not done so since 2002. According to Fluid Sealing Association (FSA) president, Thom Jessup (EGC Enterprises), “If made by a reliable source, today, PTFE does not contain PFOAs or other dangerous chemicals.”
STANDARDS AND TESTING
One issue that is slowing an organized approach to control of PFAS chemicals in solid valve components and sealing materials is the lack of a standard for determining their level of concentration in products. Some FSA and European Sealing Association (ESA) member companies are working on a testing protocol to determine if any of the dangerous substances are present in their products. Since the issue first surfaced in the late 20th century, the measurement process for determining the percentage of PFAS present has gone from parts per million (ppm) years ago to parts per trillion (ppt) today, meaning that acceptance criteria for a proposed standard written today would be much more precise.
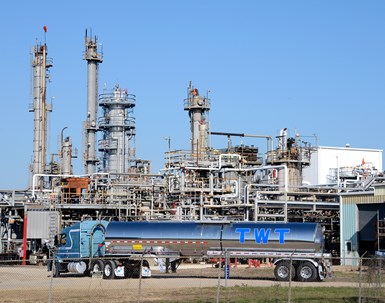
Fugitive emissions packings laced with PTFE lubricants have helped industry reduce hazardous emissions that have brought back blue skies to many industrial sites all over the world.
Many FSA members have been testing for harmful PFAS chemicals in their products for more than a decade. Hopefully, cooperative work will begin on creating a standardized test for confirming that the PTFE components like those used in the valve and sealing industries are indeed safe for their intended use. Such a standard would also give guidance to PTFE producers in developing countries, where lowest cost sometimes trumps quality assurance and health and safety-first manufacturing techniques. The EPA has proposed, but not yet implemented, regulations for imported products that contain PFOS.
“Throwing a blanket over all PFAS chemicals and the products made from them is wrong,” says Ron Frisard (A.W. Chesterton), who serves as chair of FSA’s Gasket Division. “What is needed is a commonsense approach to the problem.” The phrase echoed throughout the COVID-19 epidemic has been “follow the science”. Hopefully, those in charge of creating the rules and regulations concerning the PFAS issue will follow the science as well and not just respond with a quick emotional solution.
About the Author
Greg Johnson is president of United Valve. He is a contributing editor to VALVE Magazine and a current Valve Repair Council board member. He also serves as chairman of the VALVE Magazine Advisory Board, is a founding member of the VMA Education and Training Committee and is past president of the Manufacturers Standardization Society. Reach him at greg1950@unitedvalve.com.
RELATED CONTENT
-
Editor's Product Picks
Neles introduces valve-sizing and selection software for all intelligent automated process valves.
-
The Biggest Valves: Sizes Growing in Step with Greater Demand
Valve manufacturers that have the expertise, skills, equipment and facilities to produce large valves are rare.
-
The Final Control Element: Controlling Energy Transformation
When selecting control valves, be sure to properly evaluate the process conditions to identify potential issues and select the proper management techniques.