Materials Can Impact Product Design Life and Produce Safer Drinking Water
Some manufacturers are investing in R&D to improve products by using new materials to extend product life and value.
#components #water-wastewater
As water utilities are looking for ways to do more with less, some manufacturers are investing in research and development to improve products by using new materials to extend product life and value. A simple material choice can impact the design life, function and performance. One change that has all three beneficial outcomes for water distribution is moving from Nitrile (Buna-N) to ethylene propylene diene monomer (EPDM) for valve seats.
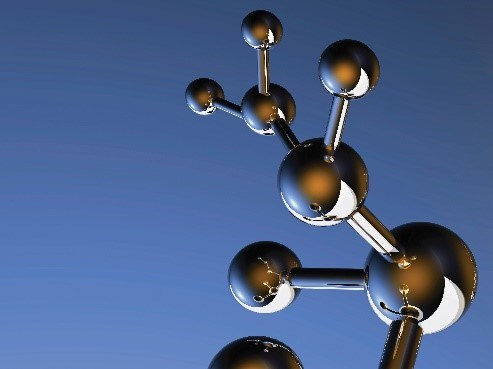
Nitrile rubber, also known as nitrile butadiene rubber (NBR) and acrylonitrile butadiene rubber is a synthetic rubber derived from acrylonitrile (ACN) and butadiene. NBR is a general-purpose, oil-resistant polymer that has good resistance to solvents, oil, water and hydraulic fluid with good compression set properties. It also has acceptable resistance to abrasion and good tensile strength in laboratory tests. The resistance to solvents, particularly oils, has made NBR a popular elastomer candidate for raw water applications, particularly where pollution and illegal dumping have allowed petrochemicals to infiltrate freshwater supplies. NBR is also used in wastewater applications where resistance to solvents and oils is important.
These properties are why NBR has been widely used for elastomeric seats in multiple types of valves including butterfly, rubber seated ball, and resilient seated check and gate valves in North America.
It has always been the mission of water utilities to provide safe drinking water, but now municipalities have to perform more testing for contaminants and seek a broader spectrum of treatment solutions. One treatment becoming more common is the use of chloramines to disinfect drinking water. This has been a standard treatment practice in other parts of the world, and as a result, water utilities have discovered that increased chloramine use leads to substantially higher rates of valve seat failure. It became evident that chloramine usage caused NBR degradation, characterized as mass change due to the rubber swelling. Mass change is the result of excessive water absorption. Other failure modes detected were increased susceptibility to breaking stress and strain, along with increasing hardness where the rubber would simply lose its elastomeric properties.
When the integrity of any elastomer is compromised, chemicals or additives can leach into the drinking water. When certain standard minimum concentrations are detected, the rubber compound is designated unworthy for use in drinking water applications, per the guidelines set forth in NSF/ANSI 61: Drinking Water System Components–Health Effects. In order to ensure rubber compounds are safe for use in drinking water applications, they should be thoroughly certified to the NSF standards as appropriate.
Shifting to a Safer and More Reliable Elastomer
As the trend in chloramine treatment increases in North America, a new approach is needed to ensure drinking water is safe and that valves continue to perform their important function without having to send out crews to replace failing seats, which could result in a service disruption. EPDM appears to not only be a suitable replacement, given the changing water environment, but a superior performing elastomer in general when compared to NBR. However, not all rubber compounds perform the same. Some NBR compounds perform very well under adverse conditions, as noted in AWWA M75-Elastomers for Waterworks: Pipes, Valves, and Fittings. The same can be said for Styrene-butadiene rubber (SBR), natural rubber and neoprene rubber.
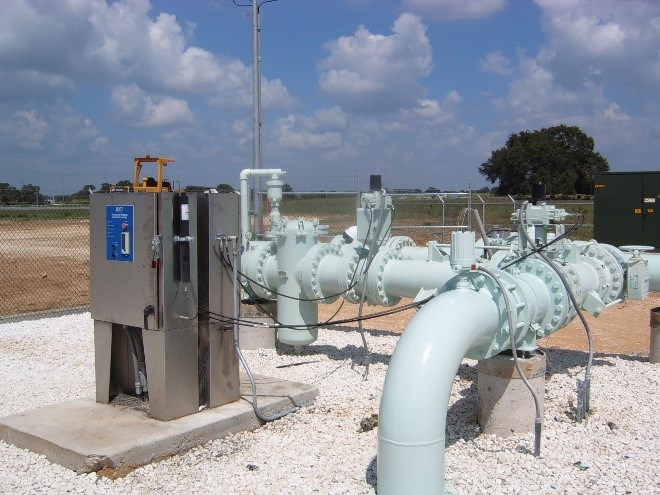
With the growth of chloramine treatment for drinking water, valve manufacturers need to ensure their valve seats are made of materials that will withstand the new chemicals.
Photo Credit: Henry Pratt Company
The most common way to confirm the integrity of a specific rubber compound is by testing under lab conditions. Many formulations of peroxide-cured EPDM are favored as less susceptible to chloramine degradation followed by many formulations of NBR, SBR, natural rubber and neoprene rubber. As new methods of disinfection come into play, manufacturers of components for water infrastructure will need to adapt and innovate products to better meet the needs of the municipal water industry.
The decision as to what rubber compound to use is commonly based on past practice and often outdated specification language. Given research and the industry’s desire to continuously innovate the functionality and extend the product life of water infrastructure solutions, companies are moving to EPDM as the standard seat material for their valves. EPDM has the additional advantage of being readily available and globally sourced, reducing the challenges of supply chain issues with NBR that have arisen since the start of the pandemic.
As materials improve and industry standards evolve, utilities often wait to adopt these changes until they upgrade facilities or perform routine maintenance that requires replacement parts. The latter is where utilities have an opportunity to adopt better designs and materials, increase the design life of existing infrastructure, and reduce the frequency of maintenance as a result. Knowing what materials and design improvements are available for new builds or plant upgrades is key to ensuring utilities are well positioned to handle the challenges of today and the evolving landscape of delivering safe drinking water to all citizens.
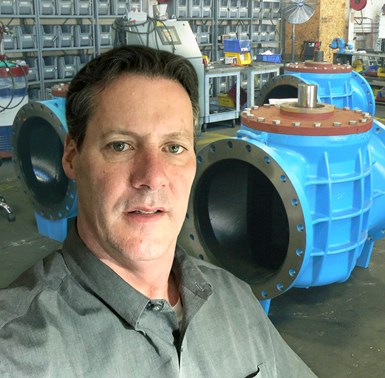
Photo Credit: Henry Pratt Company
Timothy Fallon is the technical sales manager for Henry Pratt Company (a Mueller brand).
He has been in the valve industry for over 25 years and has a strong technical understanding of valve engineering to ensure customers have the optimal flow control solution.
RELATED CONTENT
-
The Diverse Role Valves Play in the Chemical Industry
The chemical industry is extremely diverse with more than 60,000 known products. Like all process industries, the chemical industry needs valves designed for safe, efficient and reliable process operation.
-
Paint & Coatings
A walk through a typical valve distributor’s warehouse will yield a contrasting view of either silver or black products.
-
Proper Care of Knife Gate and Slurry Valves
How to resolve—and avoid—field failures of knife gate and slurry valves