Valve Technology Reduces Compressor Surge Risk
With demanding performance requirements and targets for reducing emissions placing plant compressor equipment at risk of damage, proven anti-surge and compressor recycle valve technology can help the oil and gas industry avoid disruptive and costly unplanned compressor damage and consequently downtime.
#valvehistory #gate-globe-check
With demanding performance requirements and targets for reducing emissions placing plant compressor equipment at risk of damage, proven anti-surge and compressor recycle valve technology can help the oil and gas industry avoid disruptive and costly unplanned compressor damage and consequently downtime.
To address these concerns, IMI Critical Engineering has developed an integrated anti-surge and compressor recycle valve that combines multiple, co-acting technologies to balance efficient production and equipment health. The valve comprises of IMI CCI’s patented DRAG Control Valve technology with SC/V actuators and smart, high-performance FasTrak or QuickTrak controllers and positioners. The solution’s individual parts, developed in-house at IMI, continually interact to reduce the chance of cycle trips to optimize performance at start-up and during operation.
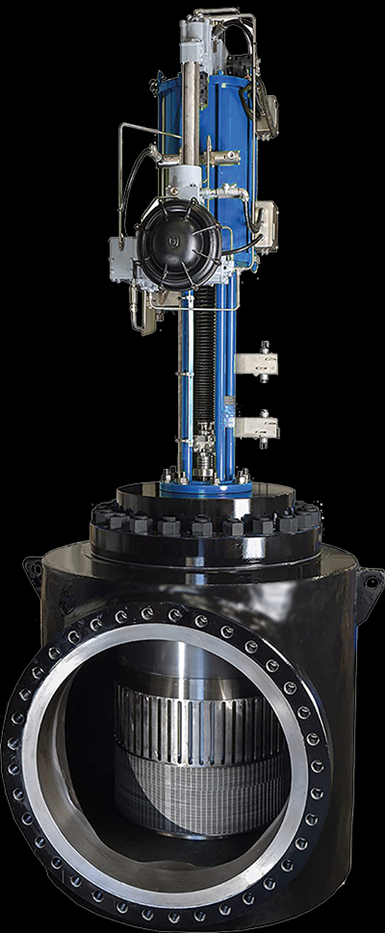
Designed for operations in the oil and gas sectors, the valve also uses a high number of stages for small openings at low flow conditions. As a result, greater velocity and flow control is provided, meaning that fewer cycles are required to achieve product compression targets, reducing the carbon footprint. This provides another way for the industry to reduce emissions by making processes more efficient.
“In demanding applications, the valve manages high dynamic forces, so failure risks must be minimized for the best possible performance,” said Mike Semens-Flanagan, global engineering director at IMI Critical Engineering. “Similarly, valve issues including vibration, noise and erosion caused by the wide differential pressures that occur during these operations can impact nearby equipment if not addressed.”
Semens-Flanagan continues: “Having greater control over compressor systems is crucial to ensuring optimal flow levels through the valve and improving plant sustainability in line with ever-tightening environmental legislation. Our unique, fully integrated anti-surge and compressor recycling valve is an excellent example of this approach in action.
For more information on IMI’s anti-surge equipment portfolio, visit the company’s website.
RELATED CONTENT
-
The Fundamentals of Gate Valves
The venerable gate valve remains a primary choice for many service applications.
-
VMA Looks Back at 2012 and Forward to 2013
Contrary to dire predictions, the end of the Mayan calendar signaled only the end of one cycle and the beginning of another, while the end of 2012 signaled the end of another banner year for the Valve Manufacturers Association and the beginning of an exciting 2013.
-
The U.S. Valve Industry in World War II
While valves didn’t directly sink ships or shoot down planes, the American valve industry played an important role in winning World War II for the allies.